With rising sea levels a global concern we’re all looking for a faster transition to renewable energy and supporting that with batteries. Zinc may not be the obvious choice for energy storage but it is cheap and has a high specific energy density. Dr Mike McDonagh evaluates the current status and outlook for zinc-based electrochemical storage for its potential in large-scale secondary batteries.
Whilst the term ‘galvanising’ is a plain misnomer for dipped zinc coatings, it does hint at the heritage of zinc as the first recorded metallic electrochemical battery, invented by Volta in 1800. There is some evidence that this invention was inspired by Galvani, who discovered that using iron and bronze tools simultaneously caused twitching in a dead frog undergoing dissection.
These primary batteries of Volta were stacks of intermittent zinc and copper plates, interleaved with cloth soaked in alkaline solution called ‘Pila’. Whilst they were not rechargeable, they did show the principle of electricity generation from metallic electrodes in an electrolyte.
Zinc popped up again in 1836 as the Daniels cell, which consisted of copper and zinc with an acidic electrolyte. This was more portable but again not rechargeable. The primary zinc battery has undergone evolutionary development, but at the end of the 19th century the first rechargeable zinc battery was invented, based on liquid zinc bromide. In 1901, Thomas Edison held one of the first patents with a nickel-zinc rechargeable battery.
Many practical difficulties with zinc-based rechargeable electrochemistry resulted in little development activity for over a century. However, current global pressures on finding solutions for electric vehicles, renewable energy storage, peak levelling energy storage etc., have created renewed interest in zinc as an electrochemical storage material.
Why zinc?
The obvious choice of metal would usually be from the top left of the periodic table, where the greater ionising energy (which provides the highest electrochemical voltages), and the lightest elements, are found.
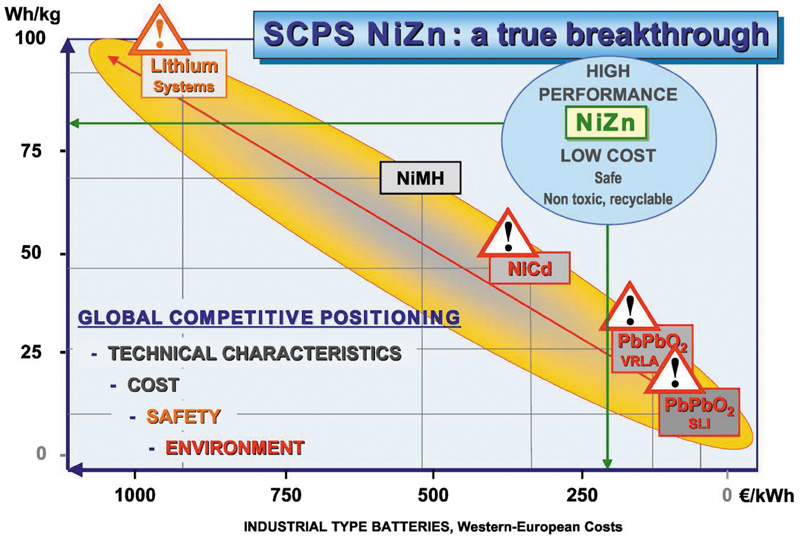
The reasons are two-fold: the relative cheapness and global abundance of zinc, and the attraction of it as a divalent electron carrier. It is this 2e- charge-carrying ability of the zinc ion that effectively doubles the current available during the electrochemical reactions. This means higher amps/kg and therefore higher specific energy density. There is also the remarkably low internal resistance that facilitates fast charging and high discharge currents. These are attractive features in applications that need instantaneous power and have limited recharge times— in other words, energy storage, UPS and standby power. Fig 1 shows a comparison between various established battery chemistries and nickel-zinc, for energy density and cost.
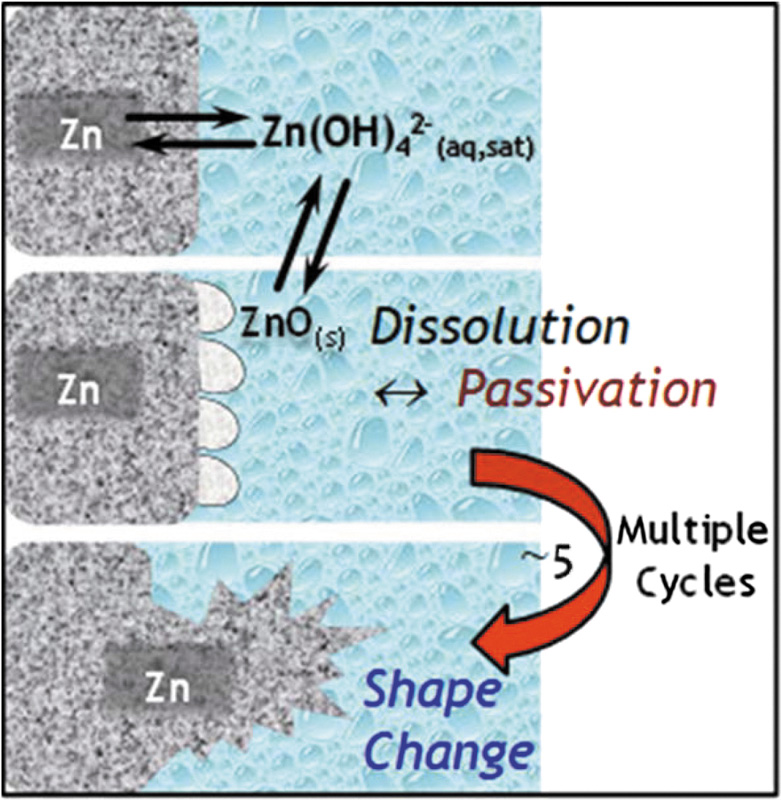
As mentioned, the 20th century saw zinc rechargeable batteries left behind by the familiar rechargeable chemistries of lead-acid, nickel cadmium, nickel metal hydride and, more recently, lithium-ion. Despite the zinc in primary battery demand remaining strong, due mainly to the safety, cost and abundance of the constructional materials, the rechargeable versions have not seen commercial take-up. The main reasons for lack of progress for the rechargeable nickel-zinc design can be appreciated by examining firstly the reversible electrochemistry of the battery, shown in Fig 2. The two points to note are:
- At the anode, zinc is oxidised during discharge into the soluble zinc hydroxide, and then plated out as metallic zinc on recharge
- At the cathode, nickel is reduced on discharge to the hydroxide, then oxidised on charge to form the oxyhydroxide, which is relatively insoluble, and also an insulating material.
These two reversible reactions, which result in a respectable 1.7V per cell (NiCd is 1.2V/cell), provide both the attraction and the rejection of this chemistry. The reactions seem innocuous enough, but in the standard electrolyte, they have serious shortcomings.
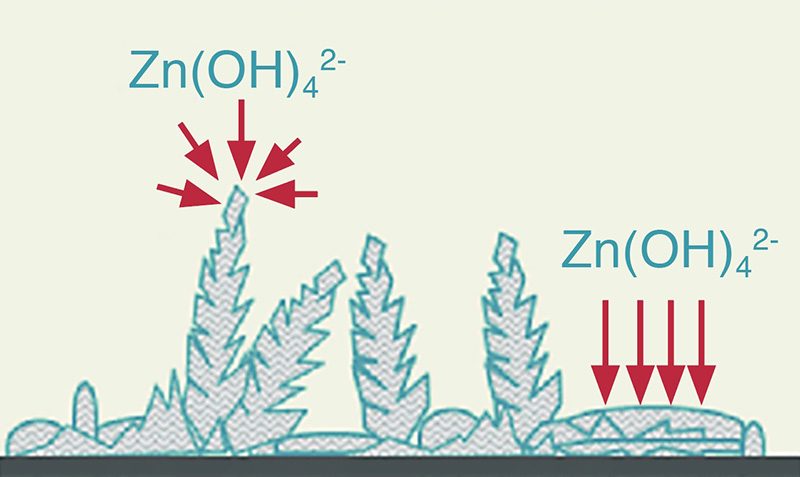
The problem is the zinc anode, and that, in turn, is very dependent on the electrolyte solution. Fig 2 is a schematic representation of the issues that have bedevilled the commercial rollout of large-scale nickel-zinc batteries. The production of a passivating layer and the inconsistent deposition of zinc— leading to separator piercing zinc dendrites (Fig 3)— are the two main afflictions that have been thorny obstacles to progress in developing large-scale aqueous batteries. Added to this is the cathode charging reaction, which produces non-conducting compounds that gradually increase the internal resistance and seriously hinder the battery’s recharging capability. Until recently these have been viewed as fairly intractable problems, with little commercial pressure to resolve the underlying causes.
New storage demands
However, times and circumstances change. There is now a clear need for a higher energy-density battery, which is also safe, non-toxic and easily recycled. Add to that a low cost of ownership and we may just have defined the basic elements of zinc battery electrochemistry. Fig 4 is a comparison of nickel-zinc chemistry with established electrochemical couples as a function of depth-of-discharge (DoD). The superiority in energy density even at a low DoD of 50%, which hints at a very long cycle life, illustrates the attraction of this couple.
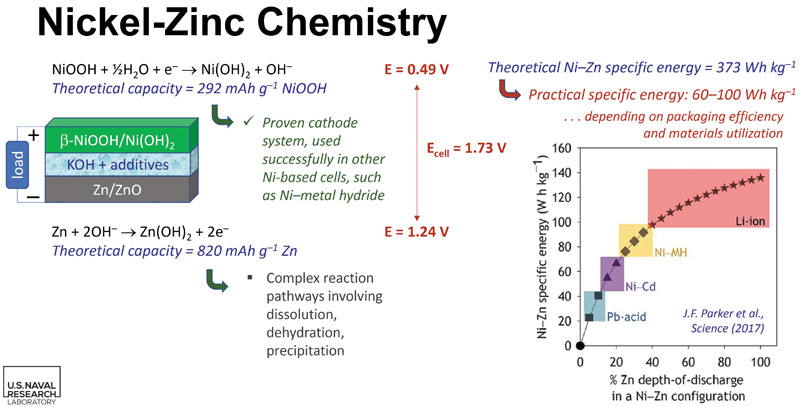
Because of these advantages, there are a growing number of companies who are exploring different methods of utilising zinc in rechargeable batteries. These are, basically, metal-zinc couple, zinc-air, zinc flow and zinc-ion options.
Nickel-zinc
One advanced option for the metal-zinc option is being marketed by ZincFive who have elected to go for the mature nickel-zinc chemistry using the aqueous electrolyte with its previously described life-limiting faults. With their technology, the dendrite formation and passivation problems have been resolved in two main ways:
- New electrolyte formulation
- New anode/cathode materials
There is little detail available due to commercial restriction, but there are results that have given ZincFive the confidence to bring their technology to market. In their own words: “Before ZincFive was able to make available the advantages of the nickel-zinc battery chemistry they needed to solve the technical problems associated with the instability of the zinc electrode in a rechargeable cell. The cornerstone of this solution was found in a patented electrolyte formulation that reduces zinc solubility and prevents dendrite shorting problems.
The capabilities of the cell were further enhanced with patented advancements in both the positive and negative electrode composition that eliminate the inclusion of toxic material.”
There is very little information available for the details of the ZincFive technology, but the company has been funded to the tune of $13 million earlier this year, taking the total to over $40 million. They are also in early stages of commercial production with their UPS Stealth battery approved for use by Oregon department of transport as part of their ‘Green Sheets’ product list. According to ZincFive, the energy density is close to 100Wh/Kg, has a high-rate performance that exceeds lithium-ion and with a comparable cycle life. In addition, it is more environmentally friendly than other chemistries and should be cheaper to manufacture once economies of scale are able to kick in.
Zinc-air
The next most commercially developed chemistry is the zinc-air battery. In widespread use as a primary system, it has many advantages as a large-scale secondary battery. Unfortunately it also comes with the zinc element headaches.
A generic chemical reaction for a metal air battery would be:
Αnode: Μ ↔ Μ+ + e–
Cathode: xΜ+ + Ο2 + xe– ↔ ΜxΟ2
(x = valency, normally 1 οr 2)
In the case of Zn-air there is a more complex situation:
Cathode: Ο2 + 2Η2Ο + 4e– ↔ 4ΟΗ– Oxygen reduction with catalyst
Αnode 1: Ζn + 4ΟΗ– ↔ Ζn(ΟΗ)42- + 2e– Ζn oxidation
Αnode 2: Ζn(ΟΗ)42- ↔ ΖnΟ + Η2Ο + 2ΟΗ–
Overall: Ζn + 2ΟΗ– ↔ ΖnΟ + Η2Ο + 2e–
E = 1.26V vs. SΗΕ
The above chemistry provides two principal sources of frustration. The first is the precipitation of excess zinc hydroxide in high concentrations of KOH, which causes passivation and creates a bothersome sludge that needs removing. The second is our old friend the non-uniform re-deposition of zinc with the usual dendrite and shorting consequences.
Add to this the take up of carbon (from the atmosphere) by the aqueous electrolyte to form K2CO3 and KHCO3. These products deposit on the air electrode to block or reduce oxygen transfer, which gradually reduces the cell performance. These problems alone provide serious obstacles to realising a commercial battery.
Added to these woes, the KOH electrolyte— widely used in zinc-based batteries to meet the requirements of low cost and high ionic conductivity— is affected by environmental CO2 and relative humidity. Both of which combine to form K2CO3, which adversely affects the air electrode.
There is also the problem of evaporation of electrolyte or the absorption of water from the external environment. The former makes the battery expand, and the latter affects the transfer of OH–.
Despite these considerations, there are solutions being proposed that are based on electrolyte and electrode material modifications that may also incorporate electrolyte flow in their strategy. Private companies are beginning to emerge which are at early-stage commercialisation and have received substantial private and public funding.
Zinc flow
One company that is in an advanced commercial position is EOS who have gone down the electrolyte and electrode modification route. They have teamed up with a nuclear power plant supplier (Holtec), to form a joint venture large-scale manufacturing company called Hi-Power LLC. They are manufacturing and supplying a battery called Znyth® (zinc hybrid cathode), which employs a unique zinc-halide oxidation/reduction cycle to generate output current and to recharge with minimal degradation.
The battery design includes three key components: bipolar electrodes (titanium current collector and carbon felt), injection-moulded plastic frames and an aqueous, non-flammable electrolyte. The battery is sealed, static, and tolerant to temperature extremes and abusive conditions. The Znyth technology does not require precious metal catalysts, nor does it employ rare earth metals. There are no tanks, plumbing or electrolyte outside the battery case, no pumps or high-pressure seals and no membrane to foul or damage.
EOS claims their technology, principally aimed at BESS, renewables and off-grid applications, can achieve more than 5,000 cycles with a $160 per KWh price tag. It is also safe, non-flammable, contains no toxic materials and is 100% recyclable using existing technology.
Moving on to the redox flow type of battery (probably the next commercially sound option for zinc-based energy storage), we have the zinc-bromine couple that is already being rolled out in energy storage applications. Fig 5 shows the basic principle of a flow battery with two tanks of separate electrolyte, the anate and cathate, forming an electrochemical couple with a voltage and electron flow.
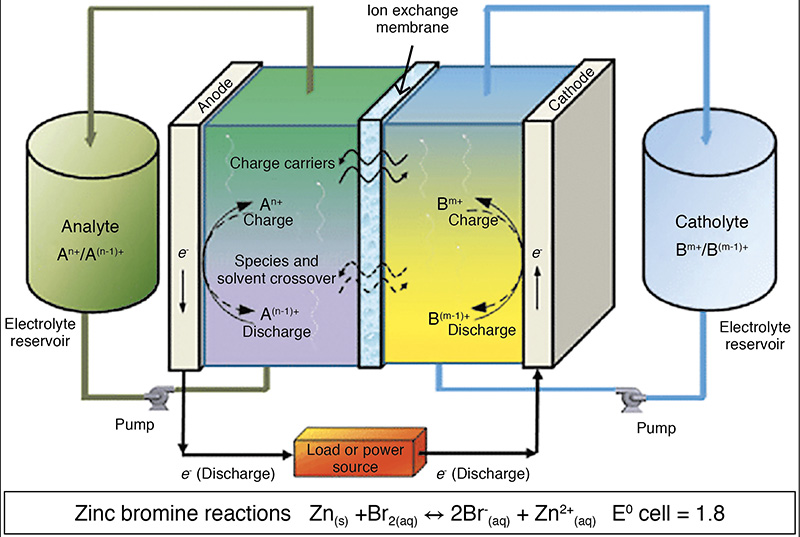
- At the negative electrode zinc is the electroactive species. It is electropositive, with a standard reduction potential E° = -0.76V vs SHE.
- In the zinc-bromine flow battery the negative electrode reaction is the reversible dissolution/plating of zinc:
- Ζn(s) = Ζn2+(αq) + 2e–
- At the positive electrode bromine is reversibly reduced to bromide (with a standard reduction potential of +1.087 V vs SHE):
- Βr2(αq) + 2e– = 2Βr–(αq)
- The overall cell reaction is therefore:
- Ζn + Βr2(αq) = 2Βr(αq) + Ζn2+(αq)
The measured potential difference is around 1.67 V per cell compared to the theoretical value (+1.087 – (-0.76) = 1.847), based on the SHE values above.
The two electrode chambers of each cell are divided by a membrane (typically a microporous or ion-exchange variety) with the bromine to form an oily red liquid and reduce the Br2 concentration in the electrolyte.
During charge, metallic zinc is plated (reduced) as a thick film on the anode side of the carbon-plastic composite electrode. Meanwhile, bromide ions are oxidised to bromine and evolved on the other side of the membrane. Bromine has limited solubility in water, but the organic amine in the catholyte reacts with the bromine to form a dense, viscous bromine-adduct oil that sinks to the bottom of the catholyte tank. The bromine oil must later be re-mixed with the rest of the catholyte solution to enable discharge.
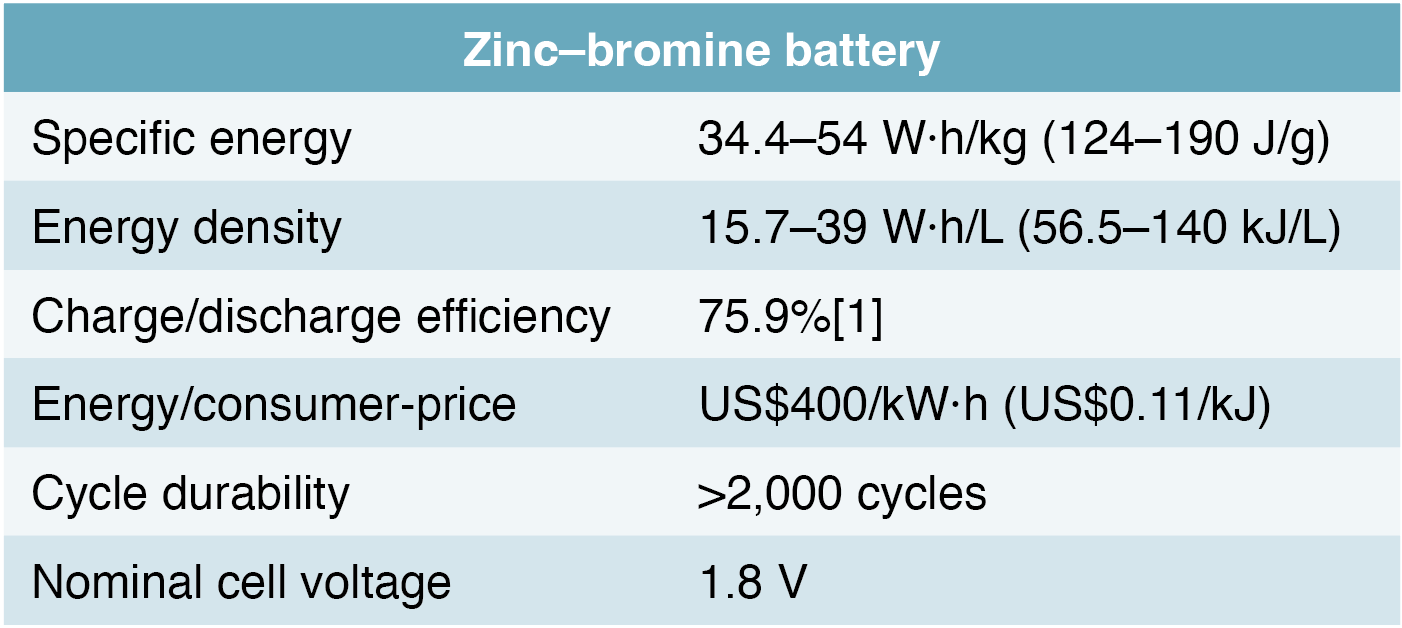
The zinc-bromine redox battery offers one of the highest cell voltages and releases two electrons per atom of zinc. These attributes combine to offer the highest energy density among flow batteries Table 1 shows the electrical properties and approximate current USD/kWh cost for this technology.
However, the high cell voltage and highly oxidative element (bromine) demand cell electrodes, membranes, and fluid handling components that can withstand the chemical conditions. These materials are expensive. Repeated plating of metals in general is difficult due to the formation of (you guessed it) dendrites, which puncture the separator. Special cell design and operating modes (pulsed discharge during charge) are required to achieve uniform plating and reliable operation.
Zinc-ion
The final category under scrutiny in this article, and new kid on the block, is the zinc-ion battery or ZIB (yet another acronym to add to the growing list of new battery technologies). Very similar to lithium-ion in its operation it uses a host cathode with mineral structure properties, loaded with zinc ions that, during discharge, are transferred to a zinc anode.
The principle is identical to that of lithium-ion chemistries. Fig 6 shows the basic metal-ion construction: there is a cathode, which is a mineral type structure that acts as a host for the intercalating zinc ions, and an anode, which in this case is a metallic zinc electrode.
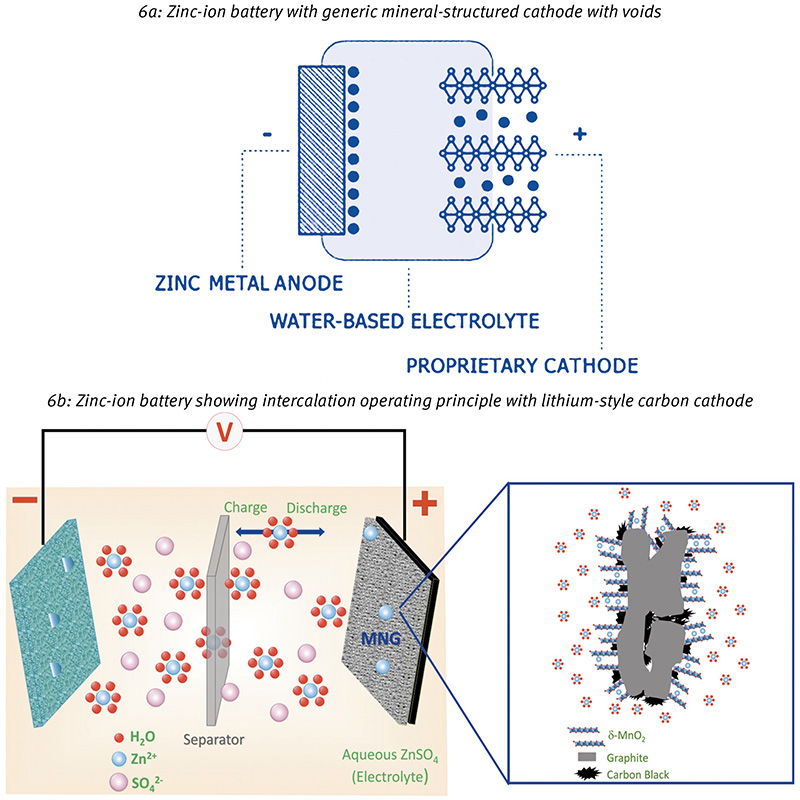
The exact chemistry of the intercalation reactions depends on the cathode materials. There are several candidates for this role currently under investigation, including manganese and vanadium oxides. Sound familiar? However, the anode reaction is not an intercalation. Instead, it is a straightforward stripping and plating process for discharge and charge respectively:
Stripping (discharge): Ζn(s) → Ζn2+(αq) + 2e–
Plating (charge): Ζn2+(αq) + 2e– → Ζn(s)
Zinc-ion battery chemistry is still under development but seems destined to use an aqueous electrolyte— either a mild alkaline or a mild acidic-safe non-toxic version. Fig 7 compares the coulombic capacities of metal anodes, showing that zinc’s electron transfer, at least, is in a class of its own compared with current metal-ion contenders. Measured energy densities at cell level exceed 300Wh/litre and 100Wh/kg. With a full cell voltage in the region of 1.9V it could well provide a high-performance replacement for lead-acid as well as lithium-ion.
As it stands, it combines a promised 1,000+ cycle life with a high energy density to place it in the realms of lithium-ion performance. There are still problems to iron out such as the old faithful of dendrite growth, which is the subject of much R&D at the moment. One early-stage company in the process of commercialising the battery is Salient Energy of Canada. They are are aiming to provide a safe drop-in replacement for lithium-ion batteries in energy storage applications, particularly for renewable energy.
If the commercialisation paths for the various forms of zinc-based batteries are successful, we could have a safe, low-cost solution for large-scale energy storage, with all of its associated benefits, in the next couple of years.
On the face of it, if the commercialisation paths for the various forms of zinc-based batteries are successful, we could have a safe, low-cost solution for large-scale energy storage, with all of its associated benefits, in the next couple of years. Not only would this greatly increase the rollout of BESS installations, it would also take some of the pressure off the lithium supply chain for the predicted plethora of global EV sales. Perhaps the funding decision-makers for emerging battery technologies will finally realise that there are many battery chemistry options, for the many battery applications, besides those based on lithium.