The ideal standard for an energy storage system is it’s safe, promotes decarbonisation, is degradation-free and operates within a closed-loop system. BEST speaks to Javier Cavada, CEO of Highview Power, about how liquid air energy storage is meeting those standards.
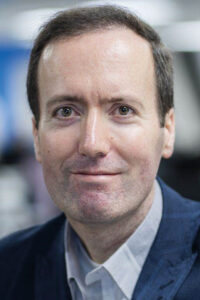
“Highview Power Storage has reached the point where it is aware of its own mortality, having a proven theory is all well and good, but selling a system from the next project is essential to the survival of the business as it runs the gauntlet between pilot and commercialisation,” wrote BEST in 2014.
We had just visited the company’s 350kW/2.5MWh cryogenic energy storage pilot plant, which uses liquid air as the storage medium and was then in its third year of operation.
The world’s first cryogenic energy storage system on the planet was built in Slough— the UK town immortalised in the John Betjeman poem, and made famous as the birthplace of ‘The Office’ television show.
Things have progressed since that visit: in June 2018 Highview launched its first grid-scale plant— a 5MW/15MWh demonstration site in Greater Manchester, UK. This June, the firm announced plans for a 500MWh plant in Chile through Highview Enlasa; a 50:50-owned joint venture between Highview and Chilean backup power generation company Energia Latina SA Enlasa.
NetZero goals are driving the need for long-duration energy storage, and we can’t get to NetZero without long-duration energy storage. Liquid air energy storage is suited to long-duration energy storage and it can be sited wherever there is a need for storage— in urban and rural locations alike.
It was clear to Highview, and also to the UK government, that technology is one of the fundamental pieces to resolve that technical conversation. It offers an equivalent to pumped hydro— at the scale and location needed— to resolve constraints, stability issues, avoid loss of frequency and provide support to systems with renewable power.
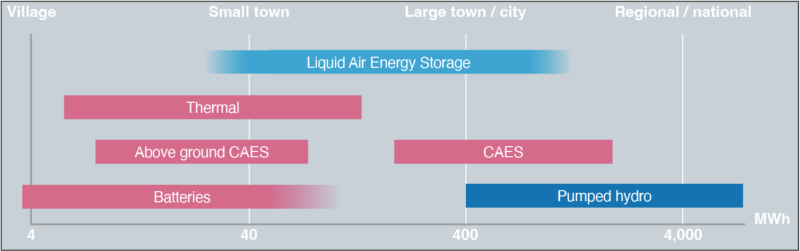
Executing a strategy
Dr Javier Cavada joined Highview as chief executive officer and president in September 2018, with the mission to drive the international deployment of the company’s proprietary liquid air energy storage technology, and execute its global expansion strategy.
Cavada joined from power solutions company Wärtsilä Corporation. He has also held a number of board-level roles, which include ongoing roles as chairman of the board of Gazelle Wind Power and board member at the US Energy Storage Association. He was also chairman of the board at Greensmith Energy, which was bought by Wärtsilä in 2017.
It was during his time at Wärtsilä that he began discussions with Highview, when he was looking at potentially investing in, or initiating a partnership between the companies. “I ended up jumping into the team to make Highview what it is today— it is a technology company with a development platform,” he says.
At the time Cavada joined Highview, the long-duration market did not exist.
“Five years ago the grid started to change its modus operandi because of the amount of renewable energy from wind and solar installations increasing to around 20%,” says Cavada.
“We need large-scale storage to balance the effects of excessive wind and solar. Our technology, like pumped hydro, is mechanically driven with a synchronous generator connected to the grid to provide power. We do what the coal-fired and the gas-fired power plants can do.”
Cavada does, however, highlight flow batteries as occupying an interesting niche area of the market, which is also long duration but tends to be low megawatts.
“Flow batteries are not good if you need a lot of megawatts,” says Cavada. “They have limitations in that sense. You will see that the applications that are being built are small, so there is a good niche for flow batteries. We occupy an area with way bigger megawatts than flow batteries. And we don’t have any hours limitation; the limitation is with the market.
“So that’s why we’ve been compared more with compressed air and pumped hydro. With those two, liquid air gives three long-duration technologies at larger scale compared to a battery. Costs drop significantly with scale, making it ideal for large-scale, long-duration applications. Lithium-ion is good for short duration, but it will take long duration storage to meet NetZero goals and address decarbonisation.”
The expansion model
Highview has a team of almost 70 people today and liquid air is happening all over the place in the market. Highview owns the technology IP and the platform, so the company has developed partnerships for development and deployment. This has enabled a faster rollout than if it had tried to do everything globally. We have licenced partners, financing partners, construction partners and supply chain partners, says Cavada.
Highview became global in the sense that they have projects with partners in the UK (Carlton Power), Spain (TSK), the US (Encore Renewable Energy), Chile (Enlasa), and Great Lakes Africa (Great Lakes and Southern Africa).
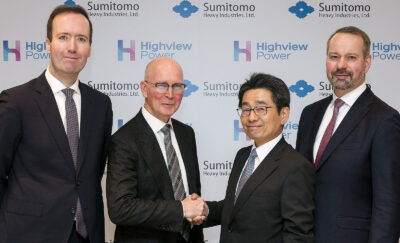
In 2020 Highview welcomed Japanese investor, Sumitomo Heavy Industries, into the company as a licensee. They are looking to develop a liquid air business in places like Japan and other Asian countries.
In the UK, developments are a lot more advanced, with a 50MW/250MWh— a minimum of five hours officially— project in the construction stage. The system could be scaled up to “several hundred megawatt-hours” and would provide important grid services to help integrate renewable energy, stabilise the regional electrical grid, and ensure future energy security during blackouts and other disruptions.
Driving towards NetZero
In the drive to meet NetZero goals, Cavada says liquid air energy storage technology can absorb enormous amounts of energy, enough even to resolve all the curtailment problems— the curtailment, the constraint, and the congestion.
“So in a way, we also solve the infrastructure and all the connection challenges,” he says. “This is a battery for the future too: it is not a battery of one or two hours, it’s a battery of five, ten, twenty hours. We could do days, but normally there is no grid today that needs days of storage.”
Globally more than 95% of the installed energy storage base is pumped hydro. The longest [battery] setup is in Portugal, which is three days, around 70 hours, of storage. Beyond those three days, all the lithium-ion that has been installed in the last four or five years, is being used for less than one-hour average duration— it’s forty or fifty minutes, says Cavada.
So, if the power markets need to move to an average of 10-15 hours, maybe an average of one day, liquid air energy storage systems are cost-effective at scale and can store energy for hours, days or weeks.
“In any grid, the UK for instance, fully relying on wind with storage, we’re not going to need more than 20 hours to resolve 365 days per year,” says Cavada.
“There may be one year where we don’t resolve one day. That’s why you will need a gas-fired backup for that last zero point something per cent. Seasonal storage looks logical but you need to know how much goes into efficiency loss— when you consume energy and then bring it back.
“So the idea is to get storage that is larger scale, long duration, but you are still operating it often. If it is not operated in several months, I would say it is not the right place to put the storage; and on top of that there are the interconnectors— to sunny and windy places.”
Economies of scale
The economies of scale work in a similar way to pumped hydro. The more megawatt hours you store, the lower the cost per megawatt hour. The sweet spot for liquid air storage starts from 50MW.
The reason is, the technology uses an industry-standard air turbine and generator. If you take a generator of 50MW and compare it to a generator of 100MW, you are doubling the rate, but only multiplying the cost by 1.4. The same happens with a megawatt hour.
“You’re not adding any additional equipment and the megawatts is still very high,” says Cavada. “That’s why we compare very well with things like batteries, which are— for the smaller and medium scale and always linear— going up. For us we are exponentially, going down. The higher the megawatt, or megawatt hours, the lower the unit cost we have.”
The pilot plant in Slough had a footprint of 25m x 25m (625m2), and scaling up would involve the addition of extra storage tanks for the cryogenic fluid. The Pilsworth grid-scale demonstrator plant had a footprint of 900m2. The project being installed at Carrington, UK has a footprint of 100m x 100m (10,000m²). A lithium-ion battery facility (not stacked) of the same scale and capacity would be approximately double the footprint.
The project being installed at Carrington, UK is a standard liquid air configuration— which starts at 50MW/250MWh and is economically scalable. Highview claims the technology has reached a levelised cost of storage (LCOS) of $140/MWh for a 10-hour, 200MW/2GWh system, and decreases from there with more megawatts or longer hours. Sumitomo says that CRYOBattery™ plants built at gigawatt-hour scale occupy 10% of the space of a lithium-ion plant and 1% of the volume of a pumped hydro plant.
For large-scale, long-duration applications costs drop to around half the cost of a comparable lithium-ion system with none of the degradation, recycling or safety issues.
A safe technology
Highview’s liquid energy storage system consists of three main components. The charging device uses off-peak or excess power to drive an industrial liquefier, which produces liquid air. Energy stored in the liquid air is held in an insulated tank at low pressure. The power recovery unit is where gasified liquid air is used to drive a turbine and generate electricity.
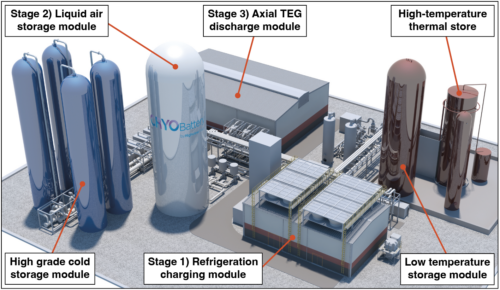
1) Charging system, 2) Energy store and 3) Power recovery— with hot and cold storage to improve efficiency
The liquid air energy storage process uses the Claude cycle, which dates back to 1902. Georges Claude proposed a cycle that involves a turbine and an expansion valve and has the peculiarity that the plant operates with a single fluid compressed at a single pressure level. The Claude cycle has been used in many air-liquefying facilities.
The technology works by first cleaning and drying air. It is then refrigerated to -196°C (-320˚F) through a series of compression and expansion stages until the air liquefies. The liquid air is stored in insulated, low-pressure vessels. These tanks are readily available from the industrial gases industry and, at a very large scale, from the liquid natural gas sector. Liquid air systems can store energy from four hours to four weeks.
Deployment requires the air to be exposed to ambient temperatures that cause rapid re-gasification and a 700-fold expansion in volume. This is used to drive a turbine and create electricity without combustion— no fuel is burnt in the process— resulting in the exhaust producing clean, dry air. Waste cold from this stage is captured by the cold storage. This is later recycled to enhance liquefaction efficiency. And in a similar way, heat generated from compression during recharge is captured by the thermal storage.
Safety is one of the biggest advantages— ambient air in and nothing but clean air out. At the end of life (30 years+), the technology (mostly steel tanks) is recycled.
“As a comparison, pumped hydro has no safety issues, but has environmental issues that are quite heavy, as we can see in Europe, Asia or America,” says Cavada. “In our case, we only utilise the air that we are breathing— and in the process, we clean out the CO2 from the air, because when we’re cooling air the CO2 becomes solid and is often sold to the brewing or soft drinks industries as a by-product. The water also becomes solid and we take it out, so at the end, you have pure air that you bring back into the atmosphere.
“At the end of the day, you’re getting clean air, and you’re keeping the air blended. An air separation unit is a standard process in the industry used to separate nitrogen and oxygen from the air, we don’t do that because oxygen is explosive and dangerous, but when it’s blended with nitrogen, which is the biggest component, it’s an inert gas.”
In terms of safety, Cavada gives the example of a truck crashing into, and fracturing, the tank. All that would be omitted is the cryogenic fluid, which is liquid air, evaporating slowly because of the difference in temperature.
So it’s not explosive, it’s the cleanest thing you could have, Cavada says, and because of the safety of our technology, it is freely locatable, so it will work in both rural and urban locations.
There is also no mining for raw materials— a big concern in the electrochemical battery industry—and no degradation.
“I have worked with batteries for many years. There is talk about second life and maybe manufacturing will solve the degradation,” he says. “But there is still the mining of lithium, cobalt and rare earths and they are not compatible with the desired standards.
“We can recycle as many times as we want. For large-scale, long-duration applications, we are extremely competitive with lithium-ion (up to half the cost). With our technology, costs dramatically decrease with scale, versus lithium-ion, which increases with scale because lithium-ion requires more batteries to scale.”