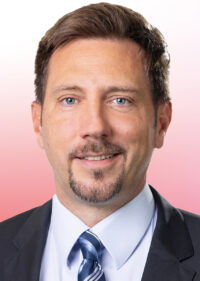
Ivor Vidjen, global head of strategy and business development for IEC low voltage motors at ABB, explains the importance of choosing the right electric motor technology for the delicate process of battery manufacturing.
Batteries are a cornerstone of the green transition and demand for more powerful, longer-lasting and faster-charging batteries will continue to soar, with a CAGR projected to surpass 30% growth until 2030.
An unsurprising trend is that batteries for electric vehicles (EVs) will account for the bulk (80%) of lithium-ion battery demand. This is because EV demand itself is skyrocketing, with the International Energy Agency projecting the global fleet will reach 250 million by 2030 and 525 million by 2035.
Despite its association with the global drive to decarbonise industry, the battery sector faces growing sustainability challenges due to the energy-intensive production of lithium-ion batteries. As eco-conscious consumers demand greater transparency, electric mobility is under increasing scrutiny –not only for its on-road emissions, but also for the environmental impact of its supply chain.
It is well known that much of an EV’s carbon footprint stems from the energy used in mining and processing raw materials like lithium, cobalt and nickel. What is often undersold, however, is the energy used by industrial electric motors to power the mixing equipment essential in battery manufacturing.
As major automakers commit to reducing the carbon impact of their battery supply chains, battery manufacturers must respond by recognising the competitive and environmental advantages of energy efficient motors in the mixing process.
Production that performs
Battery manufacturing begins with the mixing of raw materials into a slurry to coat electrode current collectors. This slurry, made up of active materials, conductive additives, solvents and binders, is subjected to advanced rotating machinery like intensive mixers, planetary mixers and dispersers.
Electrode slurry is dense and viscous, which demands high torque and power density for effective agitation and blending. Connected to an average motor, a planetary mixer might consume 8,000kWh per day to shift 20m3 of slurry. That is the same as just over 1,000 average British homes. Efficiency gains in the motor therefore have the potential to significantly cut energy consumption.
Synchronous reluctance motors (SynRM), for example, offer the torque and power density needed, while slashing carbon emissions to the absolute minimum. Rated at IE5 by the International Electrotechnical Commission – meaning they are 40% more efficient than common IE3 induction motors – they are even achieving the anticipated IE6 hyper-efficient level.
The rotor in a SynRM has neither magnets nor windings and suffers virtually no power losses. This makes the motor run cooler, which reduces maintenance needs and lowers its total cost of ownership. Motors should provide reliable, consistent performance with minimal downtime to avoid interruptions in the manufacturing process, as production integrity and consistency are paramount for the final performance and longevity of the battery.
Taking the heat
Excessive heat generated by motors could negatively impact the sensitive chemical processes involved in battery production and present a safety risk. Motors that operate efficiently with minimal heat output are essential. In cases where materials might be volatile, using motors that can mitigate and withstand industrial hazards is a must.
As a baseline, IE5 SynRM technology offers up to 30°C lower winding temperatures and as much as 15°C lower bearing temperatures than IE3. Furthermore, increased safety low voltage motors are specifically designed to prevent sparking or excess temperatures in any part of the motor during normal operation. Flameproof and dust ignition-proof motors are similarly resilient to the dangers of flammable or explosive environments – both very possible during mixing.
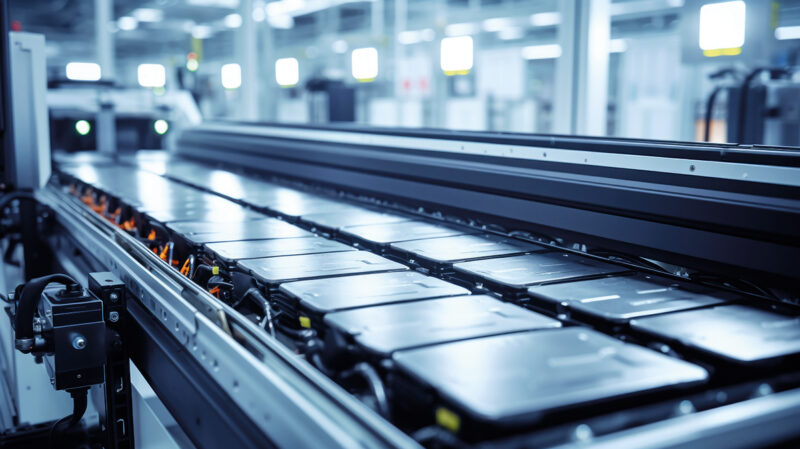
Uniform blend
Achieving a uniform blend through precise mixing is crucial for minimising impedance and optimising electrode performance, thereby enhancing the battery’s efficiency and durability. Motors must provide precise, consistent motion to ensure uniform particle distribution within the mix. Any inconsistencies in mixing can lead to issues in the final battery cells, as lithium ions are not able to diffuse evenly through the electrolyte.
Low voltage motors help ensure that active materials are homogenously distributed, while needing less power than other motor types to produce the necessary torque. Coupled with a variable frequency drive, they are able to quickly and precisely control mixing speed as required.
Speed control with a SynRM in a power train is extremely accurate due to the synchronous nature of the motor, which achieves servo-like performance due to its low rotor inertia. Furthermore, low voltage motors like SynRM are compact, making them easier to integrate into existing systems without substantial modifications.
Meeting global demand
South Korea’s growth in the EV battery manufacturing market has been accompanied by company investment in increased energy efficiency and safety in the mixing process.
Globally, the industry must pursue state-of-the-art electric motor technology to minimise energy consumption, lower maintenance costs, and reduce safety risks. EV manufacturers will soon have zero tolerance for any factors that jeopardise the quality of the batteries they purchase, and they will increasingly place importance on environmental credentials at every level of the supply chain.
Batteries are pivotal in the development of electric mobility. By ensuring precise control, energy efficiency and reliability in the battery factory, advanced low voltage motors are poised to supercharge the growth and sustainability of the EV industry worldwide.