Tim Probert travels to Frankfurt’s Automotive 48V Power Supply Systems conference to find out if 48V will be placed alongside 42V in the file marked, ‘Great idea but too expensive/complex to implement’?
Changing the voltage level of electrical systems in cars is not an easy task. In fact, it is a real pain in the backside.
The last time there was a major upshift in car voltage levels was in the 1950s, when many manufacturers switched from 6V to 12V. Despite all the positive noises at the Automotive 48V Power Supply Systems conference in Frankfurt, this author is not at all convinced the car world is about to take the huge undertaking of converting to 48V quite yet.
Automotive 48V Power Supply Systems was an immensely repetitive conference. With speakers allocated 40 minutes, this was hardly surprising.
When conference proceedings start at 8.45 and finish at 6pm, it can seem like hard work just to stay alert. A tip for next year: less time for speakers, shorter days, please.
The message about the attractiveness of a 48V powertrain was hammered home and there is little doubt lower CO2 emissions and improved fuel consumption coupled with more low-end grunt for faster acceleration via the benefit of electric motors in a ‘mild’ hybrid application is a sexy prospect.
But we’ve been here before, of course. 42V was the ‘Great White Hope’ of the automotive industry (and, of course, the lead-acid battery industry). That is now a distant memory.
While 42V – three 12V lead‑acid batteries in series – was never going to be the solution, the cast-iron need for 48V – mostly driven by tight reductions in CO2 emissions – is not certain.
Car manufacturers make all the right noises but they know this is a monumental undertaking and, at least in private, they’ll tell you that they’d much rather squeeze a bit more out of a 12V AGM battery if they can get away with it.
The problem is the load requirements have almost risen to the point beyond the capability of 12V. The average load of BMW’s fleet has reached 250A and further increases are limited by the alternator’s capacity to withstand greater load without blowing up.
BMW has a target to reduce power consumption by 50% and the German giant would perhaps rather not go to 48V if at all possible but, for its larger vehicles at least, it is seems inevitable if power consumption continues to rise.

Trying to regenerate all the energy used by a 12V system in very short recharge period would require BMW to increase either the voltage or the current, which has already reached 250A. Although Ottmar Sirch, BMW’s power network and electrification project manager, suggested a possibility to reach 350A, in practice this seems too high— with an alternator made from gold!
It’s much ‘easier’ to increase voltage, said Sirch. He thinks there is little chance of avoiding a 48V dual voltage power supply in the next five to ten years.
However, even with this relatively lengthy timeframe, Sirch gave the distinct impression BMW was doing its utmost to avoid it. Indeed, BMW has pooh-poohed the European Commission’s proposal to set an average limit for new cars’ emissions of 95 grams of CO2 per kilometre by 2020 and, via Chancellor Angela Merkel, it has successfully lobbied for this limit to be delayed and watered down.
In 10-15 years, said Sirch, mild hybrids would be displaced by pure/plug-ins. Full hybrids would reach 400-800V (although this needs considerable protection for drivers, a 400V heated windscreen would make more than your hair stand on end!). BMW repeatedly hinted all this stuff was over the horizon rather than on the horizon.
What seems certain is that stop-start technology is not enough to satisfy more stringent CO2 emission reduction targets, particularly the tougher Worldwide-harmonised Light vehicles Test Procedures (WLTP). It needs recuperative energy harvesting/e-assist to get there.
BMW said 48V had the potential to reduce power losses by sixteen‑fold versus 12V due to resistance. This allows power equipment components to be made with smaller diameter copper wire.
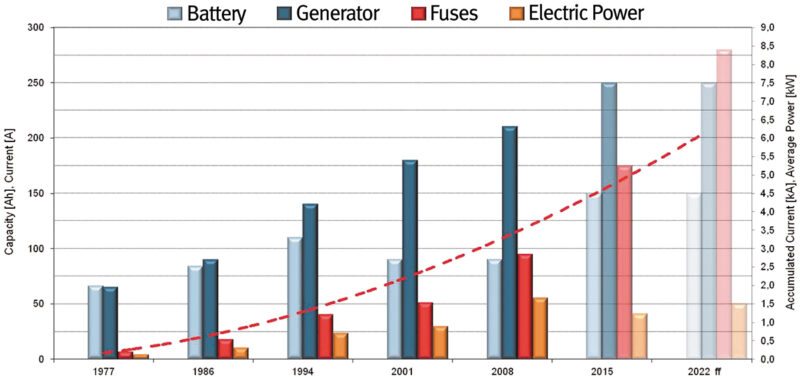
But 48V is not without problems. Aging of lithium-ion was said to be very problematic at low voltages.
Arcing looks to be a more pertinent issue. 42V cars found arcing to be a major problem; an investigation by Daimler found there is virtually no way to eliminate parallel arcing, but optimised wiring harness routing and PCB positioning can mitigate the problem.
Serial arcing can be avoided with circuit breakers. A BMW lab test found that using a capacitor at 50A load mitigated problematic arcing. Though not totally eradicating the problem, at least prevented constant arcing.
Sirch said a 7 Series car with 48V would add between €500-1000 to the production cost, below €500 at ‘serious’ volume. BMW pointed to 48V offering a potential 25-30kg wiring weight reduction, not a huge amount compared to a two tonne 7 Series, but every little helps.
In general, however, BMW seems a reluctant pioneer; it is very difficult to plan the switch to 48V and OEMs need to reach all the milestones, affecting almost all parts of the car, before proceeding. BMW is also wrestling with which cars to migrate to 48V, probably the 7, 5 and 3 Series, but possibly the 1 Series and Mini too.
Sirch said BMW was finalising plans to launch a 48V vehicle, but did not specify which car it would be (though likely to be a 7 Series) by 2020. However, during a coffee break chat with a representative of Thyssen-Krupp, the author ascertained that it had been working on a prototype 48V steering wheel for a 7 Series until BMW recently cancelled a tender for quotes…
Volvo
Where BMW leads the way (or not), others follow. Volvo has a target to reduce average fleet carbon emissions to 95g/km and it expects to reach average load of 250A within the next few years, up from 200A now.
Robert Eriksson, who leads Volvo’s electrical propulsion architecture technical team, said while 48V will never be enough for pure EVs and plug-in hybrids, there is a now at least a ‘standard’ offering for 48V across the industry, i.e. 48V/12V dual architecture, which could be used in mild hybrids and possibly micro-hybrids.
The WLTP emissions regime is more analogous to regenerative systems than the outgoing NEDC (New European Driving Cycle) regime. Yet while 48V regenerative systems deliver improved emissions, the results could not be described as dramatic.
Volvo developed a S60 prototype with a 48V lithium battery, 48V electric motor, 48/12V DC-DC converter and 48V electric distribution with a standard S60 diesel engine, bringing up weight by 5kg.
The result was a reduction in CO2 emissions from 140g/km to 131g/km on the NEDC cycle and from 155g/km to 143g/km on the WLTP cycle (WLTC), while increasing acceleration by 2.7 m/sec to 4.2 m/sec over 0.3 seconds.
Volvo has been grappling with various options for mild hybrids– should the regenerative system be connected to the wheel or belt connected to the ICE? Wheel connections are much more efficient in recovering energy during braking, but ICE-connected systems can be harnessed at speeds of up to 100 kph.
The Swedish car maker is also struggling to find a way to integrate a 48V system with existing 12V components. In an ideal world, there would be two sets of components, one 12V, one 48V, but of course this would prohibitively expensive and heavy.
So a 48V must be treated as a completely new system rather than a 12V system with four times the voltage. Like BMW, Volvo has found arcing to be a problem, but in the lab it found capacitors in the DC-DC converter practically negated the issue of serial arcing.
Eriksson finished his presentation by noting that while the automotive industry is on the limit of 12V, it is not at the end of the line…
Bosch
Like the car OEMs, Bosch sees the big push for 48V coming from CO2 reductions, not least the switch from NEDC to WLTC, and from 2018 it sees a real momentum gathering behind it. WLTC allows fewer cycles but more decelerating and longer periods of braking – that is why CO2 figures register higher than under NEDC.
Bosch is developing a ‘Boost Recuperation System’ (BRS), a 10 kW @ 48V unit that offers an 8-18g/km CO2 reduction. BRS works by ‘downspeeding’: working with the engine to reduce RPM without additional gears.
Bosch doesn’t believe there will be a total switch to 48V.
All OEMs are discussing 48V, not all will use it but all are considering it, and not just for premium vehicles, but also for mass market cars too.
There were more than a few eyebrows raised, however, when Boris Kuhlmann, of Bosch’s starter motors and generators division, projected 1.25m 48V cars on the road by 2018, and 3.25m by 2020.
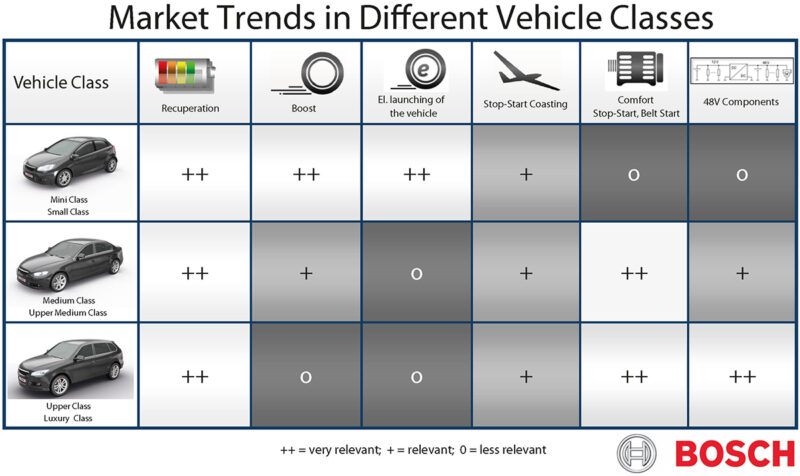
Ricardo
British engineering firm Ricardo also sees mass-market mild hybrids, including 48V, as inevitable over the next 10-12 years due to emerging hotel and ancillary loads.
For a firm like Ricardo associated with gas-guzzling motor sport, the sexy bit of 48V is the opportunity to give cars more low-end grunt, with faster acceleration and fuel cut-off at lower speeds, also opening up the possibility of downsizing engines thus further lowering emissions.
The industry rule of thumb is that it costs OEMs €50 per gramme CO2 saved, 48V could add €2000 to customer OTR price, meaning it may be something of a premium product.
Ian Whiting of Ricardo’s hybrid and electric systems division said all the necessary components such as batteries, inverters, DC-DC converters are there, but credible system costs remain a challenge. Whiting, rightfully, questioned if the 10-15% reduction in CO2 allowed by 48V was really enough in the long term?
Of course, 48V does not necessarily mean lithium. Ricardo is involved with the HyBoost 2 project, involving Ford, Valeo and ALABC, utilising an advanced lead-acid battery in a Ford Focus. However, this rather uninspiring project involving not a lead-acid battery firm but a lead-acid trade association may be little more than a ‘Don’t forget about us!’ ad for lead.
Whiting noted that a 12V lead-acid battery plus supercap allows 10% regenerative power, but with torque assist and a 48V battery, OEMs can further downsize engines.
Ricardo has developed its own lithium packs using A123 cells, which it says offer 120 000 miles of 8 years life under ‘normal’ driving conditions. Although frustrated with having to keep lithium within the 60-80% depth of discharge envelope, Whiting doesn’t really care what the battery is as long as it can do the job and does not add too much weight…
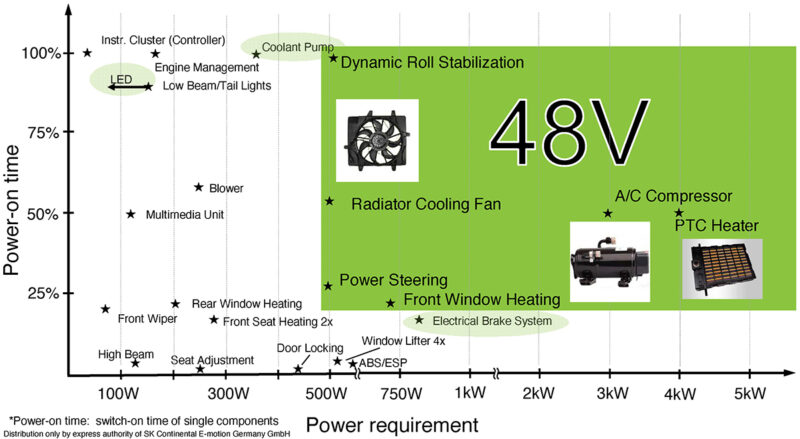
Continental
Continental is renowned as a tyre manufacturer, but that is by no means all it does. The German automotive supplier has developed a 48V lithium-ion automotive battery pack in a joint venture with Korea’s SK Innovation, called SK Continental E-motion, which began operations in January 2013.
For this venture, SK Continental eschewed industry standard lithium iron phosphate for NMC, due to the former’s hard-to-handle anode, flat voltage and relatively unimpressive power density. LMO is too prone to aging due to graphite electrode damage, while despite high power density, LTO was deemed too difficult to perform to a consistent standard.
The German-Korean joint venture also plumped for pouch cells due to improved safety, costs and cooling, although this is offset somewhat by a shorter lifetime versus hardcase cells.
SK Continental has found it a challenge to fight the right current collectors for its 13-cell (6Ah/10Ah) 280Wh/460Wh NMC packs, while conductive material is also problematic as it is “attacked” at high voltage. Whether this pack is targeted for use in 48V cars was not certain, they may find a more suitable home in industrial electric vehicles.
Automotive 48V Power Supply Systems’ panel discussion focused on the technical and practical problems of implementing 48V. There is an almost infinite range of topologies for a car’s 48V system architecture, we heard.
GM has its own 48V spec, while Toyota use three voltage levels for some of its 288V Lexus models. It is clear that there is no one‑size‑fits‑all solution and it will be a case of ‘horses for courses’.
At one stage a debate broke out about which components should be 12V and which should be 48V. BMW wants 48V components to be able to withstand a maximum voltage of 70V due to cycling spikes, particularly on start-up.
There was also debate about how the powertrain should be comprised. Different Tier 1 suppliers have different ideas about how the powertrain should be devised. Bosch does not believe in a starter motor for small cars, believing its BSG (belt-driven starter generator) is sufficient; Audi, for example, does, due to a lack of torque and possible cold start problems.
In 2011, Germany’s ‘Big Five’ – Volkswagen AG, BMW AG, Daimler AG, Adam Opel AG and Ford-Werke GmbH announced a programme to develop a dual architecture 48V system. A draft ‘LV148’ spec has been distributed to OEMs and suppliers, and LV148 is due to be updated following analysis of the resultant feedback, but as yet there remains no harmonised 48V spec.
The lack of standards is a problem for a move to 48V. Equipment manufacturers think 48V is a great idea, as they could sell a load of new kit, but car manufacturers are not nearly so sure.
Christian Kunstmann of Adam Opel AG even wondered out loud whether 48V is the best voltage level, and although the industry had the required 48V technology, do car manufacturers really want to use it? There were also questions as to the unproven lifetime expectation for 48V systems.
In contrast, Frost & Sullivan’s power supply systems expert Prana Tharthiharan was highly optimistic about 48V, perhaps seeking an opportunity to flog more of the market intelligence firm’s (questionably useful) ‘crystal ball’ reports. Tharthiharan’s crystal ball looked a little cracked in Frankfurt, as his presentation looked dated in light of revelations about OEM’s slowing progress.
Tharthiharan sees a 48V tipping point at 3 kW load and cited 2020 as the magic year (as so many others do in so many energy-related industries!) when it will become standard, with 2m European 48V vehicles expected on the road.
As for battery technology, well, Tharthiharan forsees big things for AGM lead-acid batteries, but he dropped a clanger by citing the Volkswagen-Valeo-ALABC ‘LC Super Hybrid’ project as lithium’s superiority for 48V. As ALABC’s Allan Cooper rightfully pointed out, the ‘LC’ in ‘LC Super Hybrid’ stands for Lead Carbon!
It was not all positive. Tharthiharan lamented the lack of suitable suppliers and he highlighted the move to 48V is largely a European phenomenon, with US OEMs showing almost no interest at all. However, it was also noted that Chinese OEMs and suppliers are actively developing a single voltage architecture for 48V…
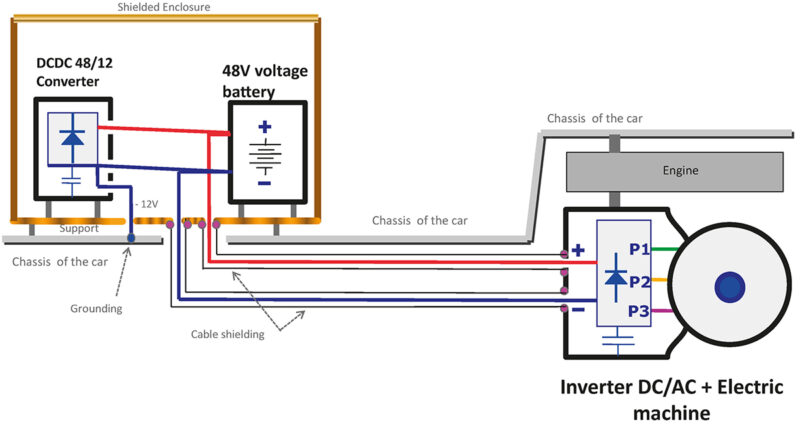
PSA
Amid great fanfare, France’s PSA (Peugeot-Citroen) announced in January 2013 it would launch an ‘Eco-Hybrid’ car in 2017, combining a 10 kW electric motor with a 48V lithium battery. At Automotive 48V Power Supply Systems, however, the poor bloke in charge of simulating electromagnetic compatibility (EMC) at PSA was less than enthused with 48V.
Salah Benhassine went into some detail into just what a pain in the arse a switch in voltage would be in terms of designing a car to accommodate 48V in terms of EMC.
Make no mistake, delegates were told, moving to 48V is a huge undertaking for the electrical systems, requiring new PCBs, cable shielding, wiring harnesses and so on.
The DC-DC converter and 48V batteries need a shielded enclosure, and it is difficult to incorporate this into the chassis while simultaneously offering protection and reducing significant electromagnetic interference. Connectors need shielding from both sides in the ‘global box’ [see diagram] and this is highly problematic.
Without cable shielding, current is distributed to doors and other places which may cause passengers problems. While not insurmountable, the need for filtering to mitigate magnetic induction is difficult to achieve, requiring dedicated R&D programmes and partnerships, as traditional cable shielding is not effective.
EMC problems and the need for more research are just one reason why the progress of 48V will be slower than the likes of Frost & Sullivan suggest. Driven mainly by EU emissions regulations, which are a moveable feast, means 48V looks on relatively shaky foundations.
As one delegate told me, “Now is the right time to start to think about 48V”. I believe he was right.