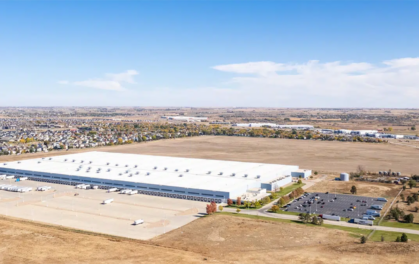

Directory
View our comprehensive directory of companies in the battery and energy storage industry.
View our DirectorySubscribe to bestmag
Find a wealth of information on the energy storage and battery industries with BEST Magazine. From all the latest news to in-depth technical articles, we have everything you need in print and online.
View Subscription Options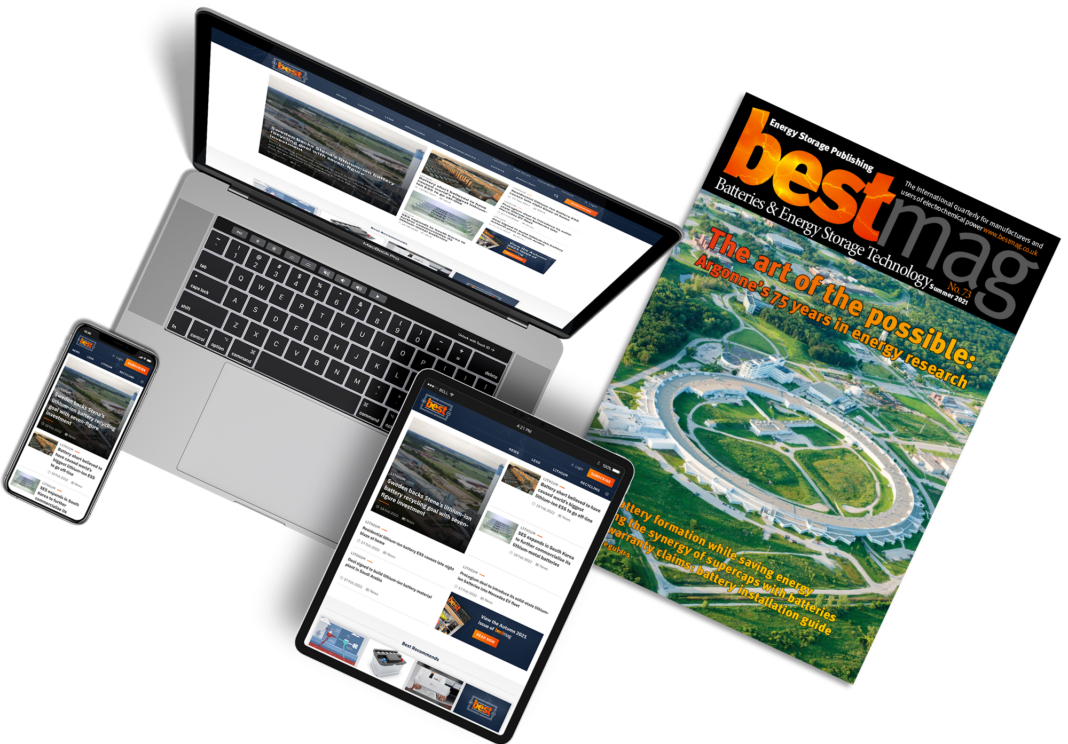