As BEST readers are fully aware, most current commercial designs of lithium-ion batteries use flammable, solvent-based electrolytes. There are regular reports of these particular designs catching fire in use, on charge, and even when being transported. One company that claims to have found a solution that is both technically and commercially realistic is Nuvvon. Technical Editor Dr Mike McDonagh reports.
Putting lithium fires out, and keeping them extinguished, is still a major headache for most fire authorities. For this reason, the industry is racing to find electrolyte chemistries that are both safe and able to provide ion transport at least as effective as the existing solvent-based liquids.
The other race is to find an architecture for lithium-ion designs that will enable the use of a solid lithium anode in order to raise the energy density of lithium-ion batteries to a whole new level. One solution to achieving this is to combine a lithium-metal anode with a solid electrolyte. This would have the twin benefits of providing the safety and energy density required to make EVs a true alternative to the current internal combustion engines of road vehicles. That is of course, provided the costs are commercially viable.
It is worth pointing out at this stage that there are major speed bumps in this race, which so far have proved a major impediment to the commercial introduction of a solid-state lithium-ion battery. These problems have been discussed at length in one of my previous articles on lithium-ion batteries, to be found on bestmag.co.uk. However, for now, it is sufficient to point out several key issues:
- The high solid/solid electrode/electrolyte interface resistance and its degradation on cycling
- Dendrite formation on nucleation sites leading to short circuits and spontaneous combustion
- Formation of an effective solid electrolyte interface (SEI) layer
- Sufficient electrolyte conductivity to enable the high power and high energy requirements available from SS lithium-ion batteries to be realised
- Manufacturing processes that meet commercial output and price requirements.
Using a polymer as the solid electrolyte overcomes most of the interface and dendrite problems, but traditionally they suffer from low conductivity, and independent researchers have identified a new generation of polymers that give enhanced performance (Fig 1).

As with all innovations, there are often practical considerations of supply, manufacture and cost that can prevent innovations from becoming commercial. Nuvvon is engaged in developments to simplify and consolidate manufacturing processes that, they say, will enable production of pouch cells that do not require external pressure to maintain a low impedance interface between electrodes and electrolyte (Fig 2).
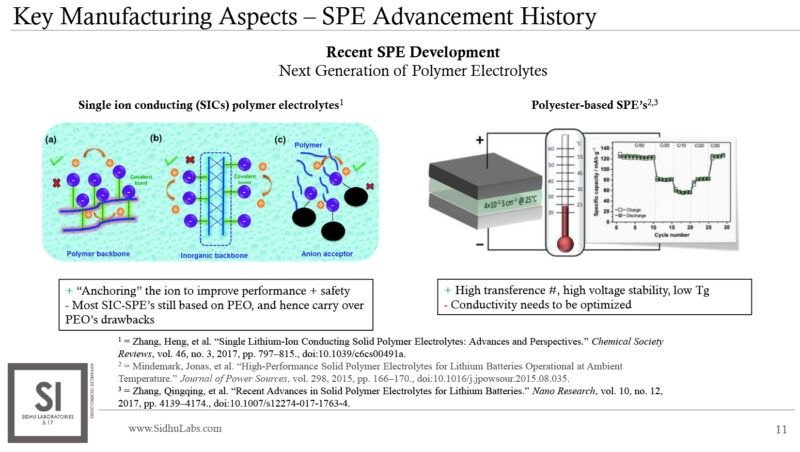
That seems remarkable, as do their assertions of faster manufacturing with lower reject rates and lower costs.
After an initial contact with Jonathon Lex, the COO of Nuvvon, I decided that it was necessary to ask some detailed questions. The following is a transcript of the interview with its president and head of innovation, Manveer Sidhu. It is in summary form with my questions followed by the answers from Sidhu.
Is the electrolyte also the separator or are they two products?
NUVVON: The solid polymer electrolyte (SPE) is both the separator and electrolyte. The SPE membrane is responsible for ensuring the battery does not short circuit (i.e. anode and cathode making contact) and providing a channel for lithium ions to migrate between the electrodes. Hence, the overall components are reduced to three (anode, cathode, SPE).
Is the electrolyte suitable for both solid Li anode and interstitial type, e.g. NMC/LiFePO4 types?
Yes, the SPE is suitable for both lithium-metal anodes and metal oxide-based cathodes. The SPEs from Nuvvon can operate with highly reactive cathodic materials such as NMC811 and spineltype LNMO.
How does the Nuvvon electrolyte compare with commercial liquid electrolytes for both ion mobility and conductivity?
When taking into account the inactive separator material utilised in the conventional carbonate liquid electrolyte, Nuvvon’s proprietary SPE technology exceeds that of the liquid electrolyte (8*10-4 S/cm vs. 4.65*10-3 S/cm for the liquid electrolyte and Nuvvon SPE, respectively).
Have any tests been done on cells other than conductivity?
Yes, other electrochemical measurements have been performed. Notably, electrochemical stability window (ESW), transference number, ageing performance at 80℃, and electrode compatibility tests have been undertaken.
What size cells have been tested and what was the construction of the anode and cathode?
To date, pouch cells of the dimensions 50mm x 50mm have been fabricated and independently tested. The anode in all cases has been lithium-metal, and the cathode has varied (either LFP, NMC811, or LNMO).
What pressures are required to maintain interface contact?
Atmospheric pressure (1 atm) is suitable for cell operation. This is profound as competing solid-state electrolyte technologies such as oxides and sulphides require immense levels of pressure (> 3.4 atm) to ensure intimate contact (Fig 3).
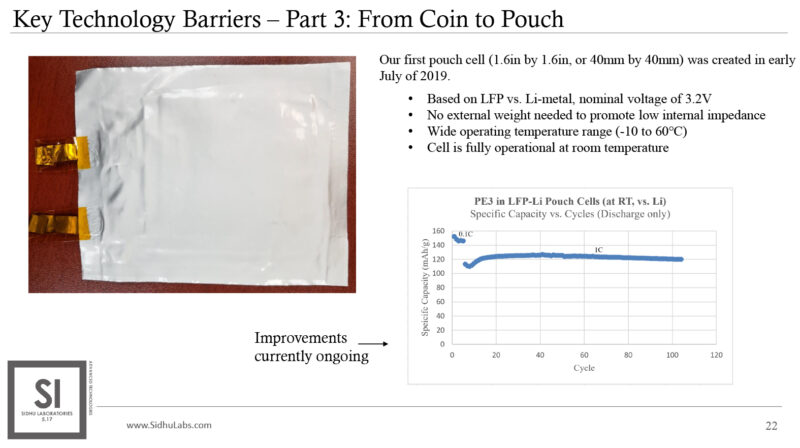
What electrode surface conditions are required to enable good, low-resistance contact with the electrolyte?
The electrode surface should be smooth and free of any impurities that may otherwise create nucleation sites for dendrites.
How thick is the layer and is it compressible to allow electrode surface irregularities that may occur during cycling?
At this time, the coating thicknesses are confidential. Nuvvon’s SPE technology is capable of being compressed without jeopardising cell survivability.
How does it cope with possible volume changes in intercalation cells?
The SPE technology from Nuvvon is capable of forming dimensionally stable films that are capable of being subjected to considerable stress prior to permanent deformation. The SPE technology has proven to be stable against lithium anode “breathing”.
Has the polymer/electrode surface resistance been measured?
The electrode-electrolyte interfacial resistance has not been measured; however, it is expected to be low because of two observations. First, high C-rates are capable of being performed (up to 3C) without significant deterioration. Second, post-mortem analysis reveals that the electrodes exhibit very strong adhesion to the electrolyte.
Are there any problems with dendrite growth?
No, there are no issues with dendrite growth. This is because of the specialised SPE coating Nuvvon applies to the lithium-metal surface, which promotes a highly stable SEI.
Are there any cycle results with charge and discharge conditions available for comparison?
There are currently no direct comparisons, however in the next few weeks, there will be. Nuvvon intends to compare NMC811 stability of conventional liquid electrolytes with the company’s SPE technology.
Does the polymer/electrode interface resistance increase with cycling, perhaps due to loss of adhesion?
No, the polymer/electrode interface does not exhibit a resistance increase over cycling. There are no delamination characteristics observed (Figs 4 and 5).
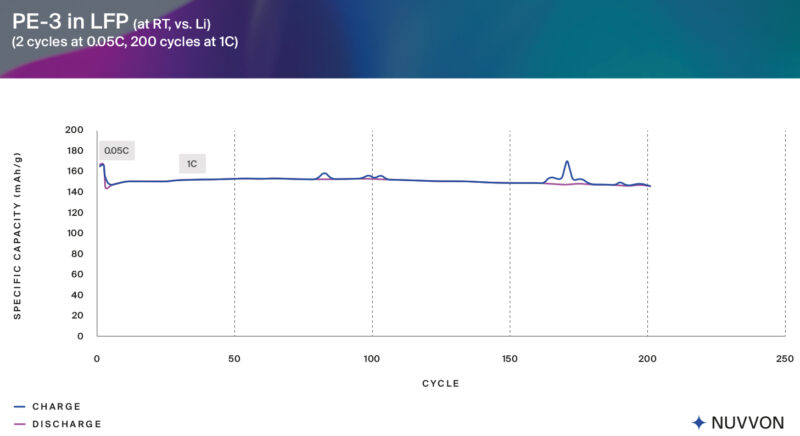
Fig 5: Nuvvon’s improved polymer electrolyte (PE-3) cycle tests with LFP pouch cell architecture.
What is the failure mechanism on life-cycle failure?
Over time, the SEI will tend to grow thicker, causing insulating-like behaviour and impeding lithium-ion transport in the polymer electrolyte. Such overgrowth of the SEI is the leading failure mechanism.
How does the polymer affect the formation of the SEI layer, both in formation and test cycling?
Nuvvon’s SPE technology plays a critical role in SEI formation. Nuvvon has a specialised polymer coating for the lithium-metal anode, and this is necessary in order to promote homogeneous lithium-ion flux. Without this coating, dendrites will occur as a result of poor SEI formation. In regard to test cycling, fewer parasitic reactions and longer cell cycle life can be observed when the lithium-metal anode is coated and protected.
Do you have plans to commercialise – if so, when?
Within 24 months, Nuvvon expects to be producing or licensing cells for portable electronics. Within another 12 months, Nuvvon will be producing or licensing cells for automotive and grid storage applications.
What further hurdles do you need to overcome to be commercially available?
The largest challenge Nuvvon anticipates is securing a steady supply of high purity raw materials involved in the fabrication of the solid-state battery. For example, high purity lithium metal foils and salts are necessary for the long-term operation of solid-state batteries. Sub-par lithium foils and salts will result in poor cell performance and negatively affect production yields.
Interesting breakthroughs
The above interview was followed by an informal interview a couple of weeks later where confidential information and results (not to be published yet) were discussed.
However, there were some interesting breakthroughs that can be mentioned. One of these was the realisation that the Tg (glass transition temperature) of the polymetric electrolyte was key to securing a low-resistance electrode/electrolyte interface with minimal external pressure, as shown in Fig 6.
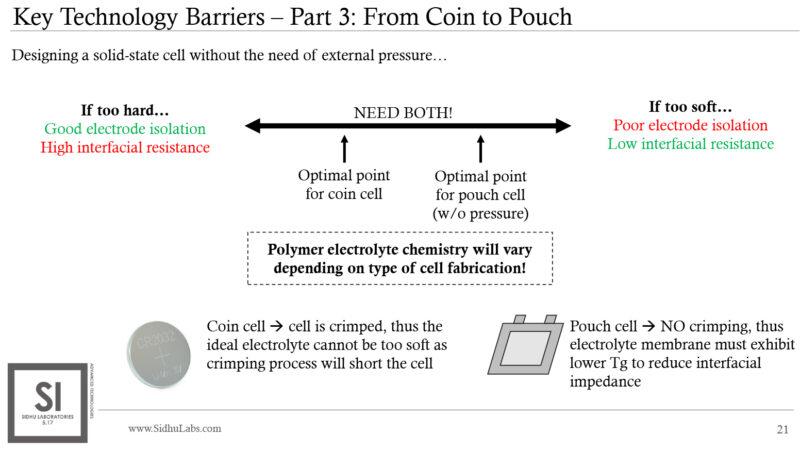
This led to the development of separate hard and soft coatings for the anode and cathode respectively. And of course, this Tg disparity between the coatings also helps to reduce their mutual interface resistance in the built cell. The latest public data from Nuvvon for its LFP pouch cells shows good cycle resistance and is a promising platform on which to develop an EV design.
It was also revealed that Nuvvon is planning to complete further trials which will shed considerably more light on its manufacturing and commercial status. If all goes well, BEST will be reporting those results in the spring edition. However, based on the assertions of Nuvvon and the results published so far, it is fair to conclude that it seems to be on the right path.
Certainly, in the author’s opinion, it is concentrating on the right areas and the right outcomes to give the industry what it needs to push battery storage and EV power to a higher commercial status.
However, it has some way to go, and as I know only too well from my own 45 years’ experience, there is a vast difference between prototype and full-scale commercial production. That being said, Nuvvon does appear to be a company that is, with some justification, anticipating a successful entry into the commercial lithium-ion battery market.