Batteries Event 2023, held in Lyon, France, in October, drew nearly 1,200 visitors, over 100 exhibitors and around 175 speakers shared industry insight. The imbalance in European battery supply and demand was laid bare. The organisers said the event, in its 25th year, was a great success. Andrew Draper reports.
Supply and demand imbalance
Presenting an overview of the rechargeable battery market and main trends for 2022–30, director of Avicenne Energy Christophe Pillot said car makers will invest more than $1.2 trillion in electric vehicles (EVs) and batteries up to 2030. Quoting Reuters and other sources, he said European and Asian auto makers have together invested more than five times as much as their North American counterparts.
Volkswagen was accounting in November 2021 for half of European investments, at $112 billion, he said. Chinese car makers made up around two thirds of investments in Asia, while Tesla, GM and Ford had approximately an even split of North American investments.
Avicenne forecast that EVs and plug-in EVs would achieve an 18% market share of all cars sold in 2023, amounting to some 14 million units. There would be “incredible growth,” he predicted: ≈30% in volume and ≈20% in value for the next 10 years.
The lithium-ion segment represents the area of highest battery growth and draws most investments, he said, while lead-acid batteries still represent 44% of the world market with almost 6GWh in 2022.
The lithium-ion battery market will grow from almost 730GWh in 2022 to 3.4TWh in 2030, he said. Cars and buses will account for half of that market (excluding China). Include China, and it becomes 75% of the market.
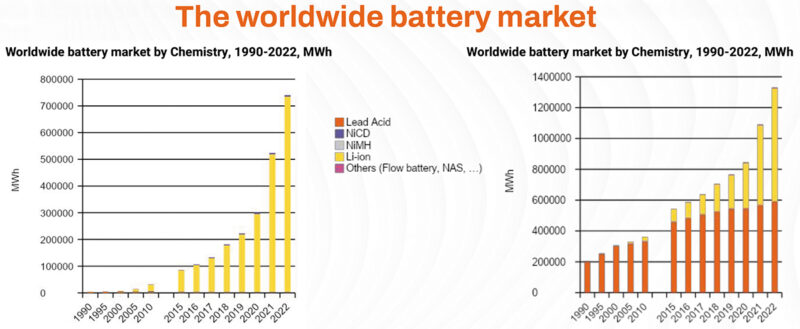
European production capacity: to >400GWH in 2025
But Pillot said in his presentation that Europe and North America will both face lithium-ion battery supply/demand imbalance. Gigafactories in the European Union will not have sufficient production capacity up to 2030: 1.5TWh of capacity has been announced in Europe for 2030, compared to 1.2TWh in North America and 5.4TWh in China.
The EU and North America will also face a shortage of raw materials, equipment and labour in 2030, he said. While recycling will potentially account for 15–20% of metal demand in 2030, on a very long-term basis this could rise to 90%, he said.
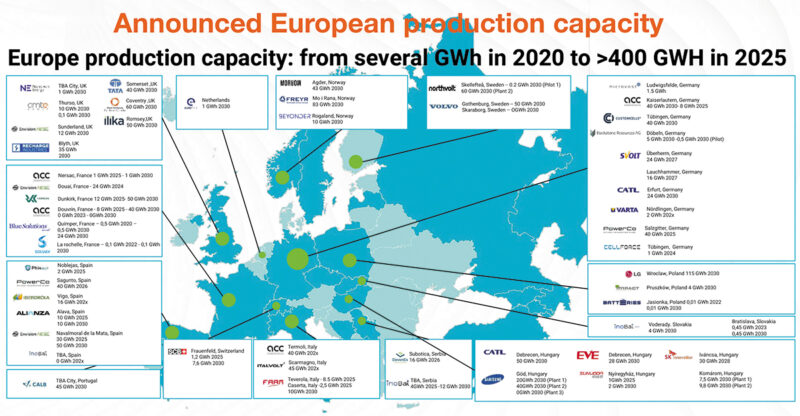
Zinc an alternative
Zinc batteries were proposed as an alternative to lithium in one of the sessions. Grégory Sacré, battery materials sales manager at specialty zinc materials provider EverZinc, said in his presentation that sustainable alternatives to lithium and lead are needed as the demand for batteries is seen skyrocketing with double-digit growth rates.
Sacré claimed most new lithium assets are of inferior quality to existing ones, leading to increased efforts to extract the desired metal. An excess of demand over supply for the EV industry is creating metal price volatility, he argued.
While lead battery recycling in developed countries is at some 95%, the process generates toxic lead emissions, he said. Zinc is “the perfect candidate” as an alternative, he added. Its target price is low ($50–100/KWh), availability is good with no geopolitical constraints, the recyclability is high and toxicity low, and there are no safety issues, he explained.
The demand for zinc in energy storage is set to rise to a 10% market share in 2030 from 1% in 2020 and 3% in 2025, he stated. Everzinc claims a 25% share of the supply of zinc for primary batteries. It has two production units, in Europe and Asia.
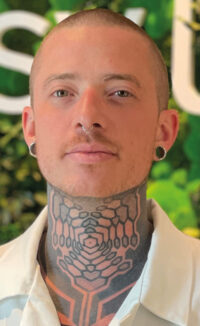
Dr. Vincent Caldeira, CTO at French R&D laboratory Easylzinc, shared with the audience his company’s progress in commercialising zinc. It launched 200 batteries in 2023 and has a calcium zincate pilot line under construction. It will turn out 50–60 tons per year and will be followed by an EU-funded pilot production plant in France, which will have output of an estimated 1,000 tons per year.
The company has patented a process to produce battery grade calcium zincate, a material that has never before been industrialised, he said. The material improves the cycle life of zinc electrodes, he added, by having a lower solubility in potassium hydroxide electrolyte than zinc oxide.
Europe will need to import 100GWh of batteries
Gert Meylemans, General Manager of EU battery manufacturers’ association Eurobat, told the audience that the market growth in dollar terms worldwide between 2010 and 2030 would be more than 10-fold. He said in his presentation: “Lithium and lead will be the dominant chemistries – lead to grow slowly, lithium with exponential growth, mainly thanks to e-mobility.”
He said Europe needs both lead and lithium batteries to try to meet demand for all applications. By 2030, demand will outstrip supply and Europe will need to import 100GWh of batteries.
By 2030 ICE vehicles, HEVs and PHEVs will continue to have 12V lead-based SLI batteries on board, he said. EVs will have 12V auxiliary batteries (both lead-acid and lithium-ion). Traction batteries will be 100% lithium-based by 2030, he said.
In terms of industrial/motive power applications, Eurobat’s forecast is:
UPS batteries
- lead-based batteries will remain dominant in 2030 (70%)
- 5.8% annual growth in volume up to 2030
Telecom batteries
- almost exclusively lead-based today, but lithium-ion market share of 11% by 2030
- small annual growth (6.7% in volume) up to 2030
ESS – grid and residential
- today, mostly lithium-ion batteries
- >30% annual growth in volume up to 2030
Motive batteries
- lead-based batteries (70% market share in 2022) still dominant today
- by 2030, lithium-ion will take over, with 57% share
- 5.1% annual growth in volume up to 2030.
While Europe is expected to remain strong in 2030, and competitive with the rest of the world, further investment is needed to maintain/improve production and for R&D, he said.
BESS lagging in Europe
Will Roberts, senior research analyst at research company Rho Motion asked the question whether BESS in Europe could catch up with China and North America. He said the BESS market took off in 2022 in China, with the US as the second largest market. Growth in BESS installations from 2022 to 2023 was 80%, with a total of 138GWh (subsequently updated to 133GWh). Projects are getting bigger, he added.

Roberts noted the EU support for energy storage, with several policy measures expected to have an impact. The Net Zero Industrial Act sets targets for manufacturing net-zero technologies in the EU. Batteries and energy storage are categorised as eligible technology, he said.
Last March, the EU proposed a reform of its electricity market. The aim is to protect consumers from price volatility, stabilise the market and boost investment in renewable energy and flexibility.
It has also made a number of recommendations on energy storage, including the removal of double taxation, introducing flexibility in energy and climate planning, identifying funding gaps, accelerating deployment of energy storage in islands and remote areas, and supporting research and innovation in energy storage.
Many EU members have received EU funding for energy storage projects under the bloc’s Temporary Crisis and Transition State Aid Framework. They include Hungary, Romania, Spain and Slovenia, he said. The framework loosened restrictions on state aid and aimed to prevent an exodus of clean tech activity to the US, attracted by the IRA tax breaks.
Energy storage targets at provincial or state level in the US and China are on track to be easily surpassed, said Roberts. Grid storage projects between 2021 and 2025 now exceed 500GWh, more than double the same time last year, he said. The market is quickly evolving and targets are struggling to keep pace. He said only a few member states in the EU have specific energy storage targets. The two largest storage states in the US, Nevada and Texas, also lack storage targets.
Still questions about sodium-ion
Pierre Tran-Van, electrochemist at France’s automotive Renault group, said in his presentation that there are still questions about sodium-ion, despite the fact it has matured over the years.
These relate to calendar aging, quick-charge capability and life-cycle assessments, which are not available as the supply chain is not yet fully mature, he said. Sodium salts are more soluble than their lithium counterparts and questions remain over electrolyte consumption over long durations.
Tran-Van said there are several signs that sodium-ion will be introduced in dedicated markets/countries, but there are still many challenges for sustainable mass adoption. He said more evidence is needed on C-rate in charging and its influence on durability, swelling and gassing.
Partial transitioning to sodium-ion “will certainly come in time,” he said in his presentation, adding the question is exactly when. The cost-benefit is not yet clear and the timing of mass introduction in passenger cars may depend on how conservative the development is handled.
Nicolò Campagnol, battery insights solution manager at consulting company McKinsey, said costs are falling but the data on this is scattered and shows a major difference between what is happening in China and elsewhere. Delays in starting production are common, he said.
This ranges from 3–30 months, and two planned facilities were even cancelled (one in Norway and one in China). Capex efficiency and ramp-up speed are major indicators of operational excellence among battery players, he pointed out. The best players significantly outperform the rest in terms of time to market (twice as fast), capex (three times better) and opex efficiencies (30% less), he said.
Internal shorts and thermal runaway
A presentation on thermal runaway by John Zhang, chair of the International Battery Materials Association’s international committee, showed that most thermal runaways in EV lithium batteries are caused by internal shorts induced by charging, parking or collisions. Within seconds, internal shorts can lead to white fumes, very hot spots and/or sparks, explosions and fire, he said.
If the heat rises enough, say to 140°C, it can propagate to the whole anode, he said. The reaction between anode and electrolyte can generate a large amount of explosive gas. That can end up being released with electrolyte solvent vapour. The heat transfer coefficient of the anode is much higher than that of the cathode, he said.
When sparks or extreme hot spots are generated, the explosive gas can violently react with oxygen and/or air when the cell case opens.
Zhang outlined several active approaches to reduce thermal runaway, including:
- ceramic coated separators (almost every manufacturer)
- insulating coating or taping on cathode mass free zone (Panasonic, Sanyo, Sony etc.)
- insulating coating on cathode slitting edges (Panasonic, Sanyo, CATL, ATL etc.).
He said a ceramic coated separator provides heat control as well as a higher energy density battery.
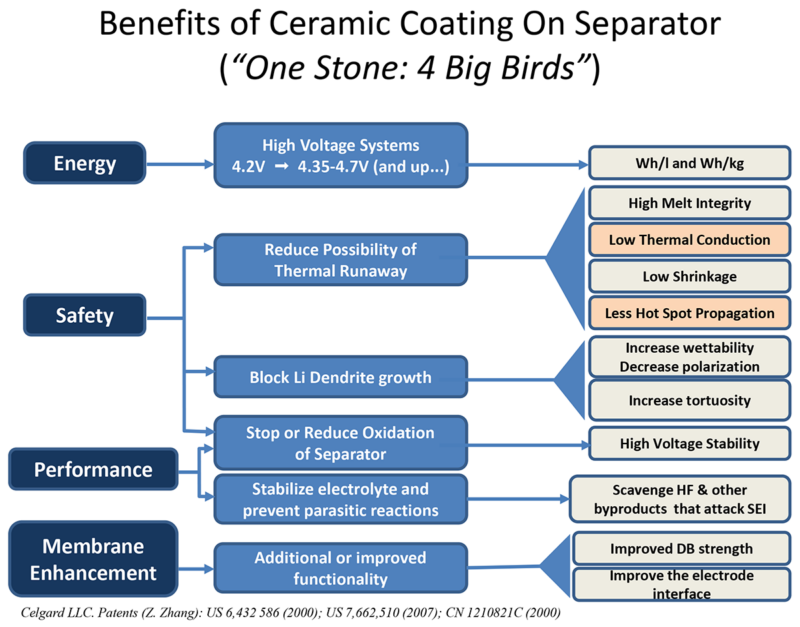
Dr. Kai Wörner, head of global manufacturing at PowerCo, shared his company’s approach to building gigafactories. It has a large demand pipeline as Volkswagen’s key battery supplier, he said. A unified cell design offers cell cost advantages and futureproofs technology strategy, while a standard factory design provides up to 30% capex advantage, he pointed out.
The company has vertical integration towards raw materials, he said, which ensures a secured supply chain. Having an experienced team with incentives provides a basis for global growth, he said. The funding structure is open to external investors and the company has a clear transaction price model, he added.
The event provided a good overview of market developments, numerous case studies by battery companies and gigafactory owners, critical materials supply, IP, chemistry and safety.