The importance of recycling is understood; the lead battery industry has known it for many years, the lithium-ion sector is steadily accepting it also needs a comprehensive, large-scale recycling scheme. Paul Crompton explores how the use of old battery packs in second-life energy storage systems is helping to delay the inevitable.
The usefulness of second-life battery storage depends on two things: its application-suitability and cost. Today, repurposing lithium-ion battery packs remains a cheaper option than recycling. For example, lithium obtained through mining is around 20% the cost of extracting it via battery recycling, according to Prescient & Strategic Intelligence.
While recycling remains costly, the materials supply chain for lithium-ion batteries grows ever more strained. This may shrink the cost gap between raw and recycled materials, but for now, the nascent lithium‑ion battery-recycling sector is in its infancy compared to the granddaddy lead-acid.
More and more battery packs are reaching the end of their first life as an electric vehicle (EV) drive train. In 2018, the California Energy Commission estimated that 45,000 batteries would be retired from the state by 2027.
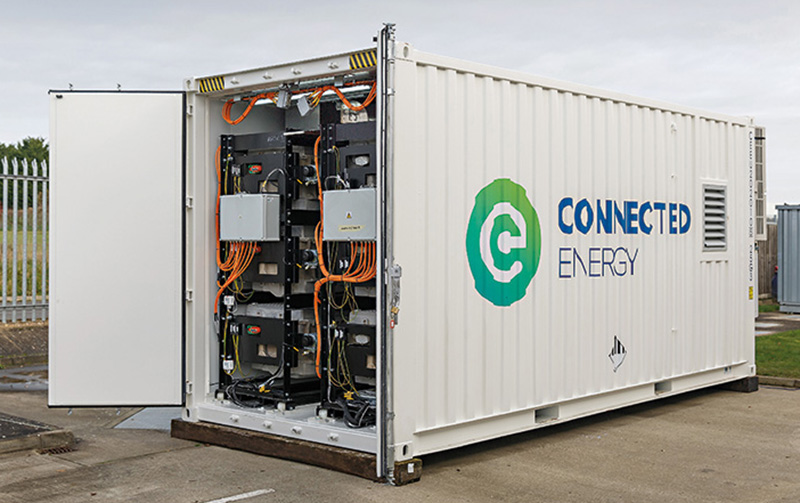
For example, Tesla’s new vehicle warranty is for eight years or between 100,000 and 150,000 miles, depending on the model. Nissan’s lithium-ion battery state-of-health guarantee (40kWh and 62kWh) is also for eight years, but only 100,000 miles— its 24kWh battery is only guaranteed up to five years or 60,000 miles.
The upshot is battery packs come to their end-of-life in EV applications despite maintaining up to 80% of total usable capacity, depending on how and where they were used.
Such batteries, therefore, are still able to perform sufficiently in less-demanding applications, such as stationary energy storage systems (ESS).
It’s no wonder the industry views repurposing battery packs from EVs to be the simplest and most efficient way to tackle both concerns in one easy fix— at least while the recycling and materials industries catch up.
Growing trend
The above factors have contributed to the growing trend in second-life ESS, with many vehicle OEMs exploring the possibilities of introducing systems, from residential to grid-scale, onto the market.
As with most things battery, the second-life market is being led by China, largely as a consequence of the massive volumes of e-busses already deployed in the country, but also because long-term contracts have been placed to procure second-life battery-based systems.
“It seems likely that the rest of the world will catch up, but the Chinese market is significantly ahead of Europe, the US and, potentially, the developing world,” says Matthew Lumsden, CEO of second-life ESS developer Connected Energy.
“Policies are starting to be developed that will encourage batteries to be reused and recycled in the market where the EVs were operational so, ultimately, the reuse of batteries is likely to become a global model.”
The key factor that will facilitate change over the course of the next decade will be battery volumes and capacities. Both will significantly reduce overall system cost— with some battery-pack manufacturers beginning to design for second-life applications. These batteries will not move into the second-life market for at least 10 years, but when they do the industry will see an impact on the ultimate cost of the systems.
Lumsden says the overall impact of this will be energy storage becoming a much lower-cost commodity, which in turn will make a big impact on the ability of non-dispatchable renewable generation to be accommodated within the system.
Today, those costs, according to a report by Reinhard Madlenera and Alexander Kirmas from RWTH Aachen University in Germany, depend on the ownership model and the upfront cost. On average, the total cost of a second-life battery ranges from $40-160/kWh, a new battery pack— in real terms— cost around $137/kWh in 2020, according to research company BloombergNEF (BNEF). Although it has reported electric bus packs under $100/kWh and predicts that by 2023, average prices will be close to $100/kWh,
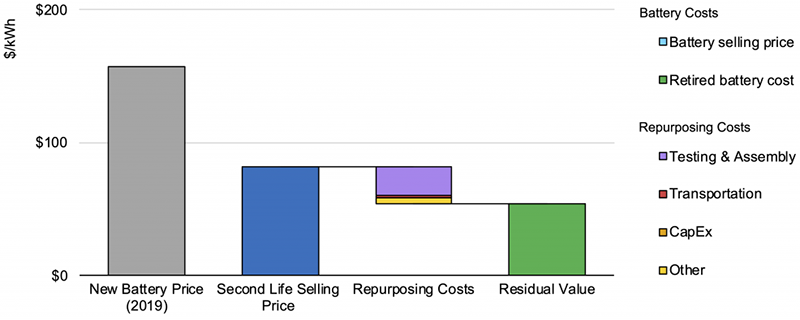
Interestingly, The National Renewable Energy Laboratory (NREL) has created a publicly available ‘battery second-use repurposing calculator’ that accounts for factors such as labour costs, warranty, and initial battery size and cost.
Second-life
BEST’s weekly newsletter is filled with stories of second-life ESS applications, from a ferry company using old Nissan Leaf batteries, to vehicle firms (including Hyundai Motor Group, Audi and Ford Motor Company) exploring the market.
In January 2019, a project exploring the use of second-life batteries in a commercial-scale lithium-ion ESS began in Germany. The joint project by MAN Truck & Bus (MAN), Verkehrsbetriebe Hamburg-Holstein (VHH) and the Volkswagen Group connected a 500kWh ESS to the charging network at VHH’s depot.
Last July, Connected Energy installed an ESS using 24 used Renault Kangoo EV battery packs in the UK. The £20 million ($25 million) 300kW/360kWh E-STOR system is helping to optimise energy use and peak loads across a system including PV, EV chargers and heating, ventilation, and air conditioning (HVAC).
The system in Norfolk is used for grid-scale services but, because the cost of degradation for second-life systems is low, the company treats its E-STOR systems as a distinct asset class in between new lithium-ion and other technologies such as flow batteries, says Lumsden.
“Functionally, our E-STOR systems can equal the parameters of new systems, but we believe the real sweet spot will be in large-scale, longer-duration systems.
“Also, as energy storage portfolios develop, we believe that there will be benefits in operating second-life systems alongside new systems to reduce the marginal costs of the overall portfolio.”
The same month, SAIC-GM-Wulin— the joint venture between US firm GM Motors and China’s SAIC Motor Corporation— created a 1MWh storage facility using second-life lithium-ion EV battery packs.
The system, at the company’s Baojun base in Liuzhou, was Guangxi province’s first cascading energy storage power station using second-life batteries. It stores wind and solar energy that is used for peak-shifting grid services.
With the glut of projects, it’s becoming clear that vehicle OEMs are getting serious about second-life— after all, governments across the world are embracing EV technology as they clamber to meet Paris Agreement targets (US president Joe Biden reversed his predecessor’s decision to withdraw just hours after being sworn into office on 20 January). It means for many countries the old workhorse ICE engines will stop being sold as early as 2030.
Testing suitability
The advantages of using second-life systems are multiple: reducing the overall life-cycle emissions of the battery, sustainability, andcost— they are cheaper than new batteries.
Their relatively low cost has two implications: first, because the batteries are low-cost, so too is the cost of degradation— which means the systems can be well suited to applications that require more aggressive duty cycles. In some cases the systems can be deployed in conjunction with new systems, to protect them from degradation while the second-life system degrades at lower cost. As a consequence of the lower battery cost, second-life systems are very well suited to longer-duration systems with a low power-to-energy ratio, says Lumsden.
However, the overall cost also relies on the diagnostic and re-purposing costs being kept low. This brings us neatly to how firms are testing the batteries to determine their suitability for re-use, and the key measurements used in deciding when a second-life system is the best option.
First, batteries are physically inspected to ensure there is no damage that could make them unsafe for use, especially if they were involved in a collision. For Connected Energy this means sourcing the packs from a known distributer. Then, there is an electronic test to make sure the battery management system is responding properly and is in control of the battery. Lumsden says his company also requires information on the state-of-health of the battery and that it’s demonstrable either through test results or drive-cycle data. If these tests are failed then the battery is safely dismantled, either for re-use at the module level or for recycling. If the above tests are passed, then the typical method is to fully charge and discharge the battery, measuring its capacity as it’s cycled.
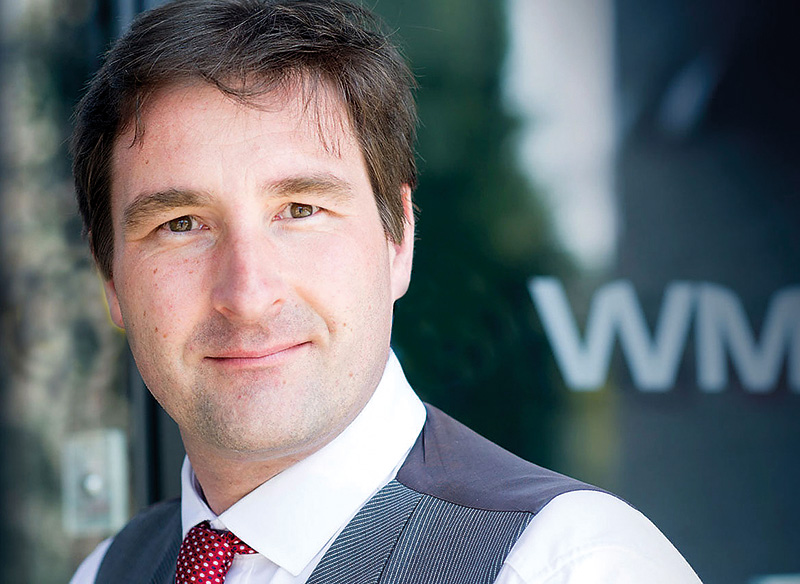
“This is a very lengthy test (typically many hours), requiring a very expensive charge and discharge system and can only be done if you are able to interface to the (manufacturer proprietary) battery management system,” says professor David Greenwood, CEO, WMG High Value Manufacturing Catapult, at WMG University of Warwick.
“We have developed alternative tests at both the battery-pack level, and at the module level, which can be run much more quickly— in just a matter of minutes— and give the same data on state-of-health for capacity (and also state-of-health for power).
“The module tests, for instance, characterise the response of the battery to AC signals over a range of frequencies, and use this to develop a ‘fingerprint’ for the battery that can be compared with the known response of batteries at different stages of ageing. The exact method is proprietary and patented— the IP now belongs to our research partner, Ametek.”
The primary metrics are: remaining useful capacity in the battery and its ability to deliver and accept power. After that it is about how expensive it will be to re-purpose.
“This depends on the design of the battery. For instance, how it is cooled, how easy it is to disassemble, how easy it is to access the BMS, and what form of casing and mountings it has,” says Greenwood.
A final factor revolves around the number of batteries likely to be available. If only a small number were sold then the business case for designing a system around them may be weak, whereas mass-market vehicles are likely to be able to provide greater quantities of second-life batteries over which to amortise design and development costs for the system.
Overcoming challenges
A major concern in identifying batteries capable of being used in second-life applications is that the BMS systems are proprietary to manufacturers. This makes it hard for third party companies to quickly diagnose the pack end-of-life, and to control it in its new application.
“At the moment, the battery must often be stripped down to module level so that a new BMS can be applied. Clearly that is undesirable, and a standardised ‘second-life interface’ for the BMS would reduce cost for the systems,” says Greenwood.
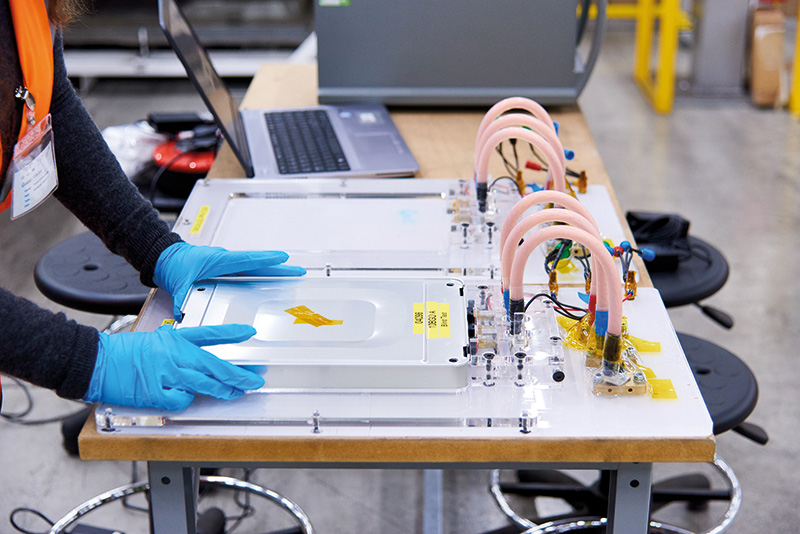
A ray-of-light is that a BMS for a second-life battery is easier than for a vehicle battery. This is due to the usage profiles, which are more predictable, and the battery being used in a much more benign environment. The main issue will be whether the original BMS can be re-used, or whether a new one must be fitted.
Connected Energy primarily uses battery packs that have an integral BMS. The key technical challenge here is communicating with hundreds, or thousands, of individual batteries, via their own BMSs, and synchronising them so they act as one.
This is important in ensuring the system is not compromised by one weak pack. Within Connected Energy’s systems, each battery is individually monitored and controlled so it can be utilised according to its real-time temperature, SoC and SoH status.
“To maximise the value of the batteries, we are developing a machine-learning layer that will focus on enabling us to more accurately manage the batteries according to a range of objectives,” says Lumsden.
“We may, for example, want to manage the batteries to maximise their lifespan, minimise their working temperature or maximise the efficiency of the system. We have a number of options, in relation to how we control the batteries, that provide differing benefits.”
A second issue is, many batteries are not designed for re-use and can be extremely difficult to disassemble, due to the use of structural adhesives and intumescent materials.
It means cost reduction for diagnosis, disassembly and re-application of batteries is critical to making a viable business case for second life— which at the moment can be marginal, especially as new cell costs are reducing, says Greenwood.
At the other end of a repurposed system’s life-cycle is its final end-of-life. The measurements for this are no different from those of a new system, and systems will need to be replaced when they no longer meet the requirements of the system operator, says Lumsden.
However, the key difference is that, given the rapid increases in battery development, low-cost replacement batteries could be higher spec and more energy dense than the original ones. “This means that operators may choose to upgrade their batteries earlier so that the system is effectively upgraded at a very low cost,” says Lumsden.
“Many revenue models for energy storage have an increasing dependence on capacity rather than power, so we see this peculiarity being attractive to operators.”
Driving growth
Clearly a buoyant EV market, coupled with a growing energy storage market will drive growth and the competitiveness of using second-life systems. This will be especially true when, or if, significant volumes of batteries become available to the sector.
“In the time-frame to 2030, a major issue will be lack of second-life battery availability; EV sales are still relatively low, and as the vehicle typically stays in the field for 10-15 years, we won’t be seeing the batteries sold in cars today returning for second-life until well after 2030,” says Greenwood.
“It is also possible that the material value of the battery (for input to new battery manufacturing supply chain) may become greater than its re-use value. In which case second life may be skipped completely and the battery taken into recycling and recovery instead.”
All going well, the influx of usable packs from EVs will follow a few different routes into the market, depending on who owns them and why they are being replaced.
“Probably the greatest challenge for the next five years, until there is an established flow of batteries, will be matching battery availability to projects,” says Lumsden. “We are dealing with this by having systems that can utilise a range of batteries that can be combined to meet the requirements of larger projects.”
A key area of focus will be linking various parts of the value-chain, to ensure the industry creates practical approaches to filtering out the reusable batteries, and valorising them, so they create worth throughout the value chain.
The more effectively the industry can do this, the better it will be able to help fleet financiers underpin the residual value of EVs, for example.
The attractive batteries will be those that not only hit the right price point but also have the data to support their state-of-health and have a degree of predictability in relation to when they will become available, says Lumsden.
“As the value chain develops we expect to have close relationships with both battery owners and recyclers, and will be able to offer additionality to both of their business models,” he adds.