The announcement about a start-up from Hyderabad launching the production of India’s first home-produced supercapacitor attracted attention. Frank Lev talked to Mahesh Godi, CEO of GODI India, to find out more about the first-in-India 3000 F supercapacitor.
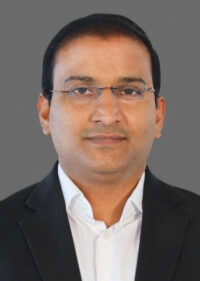
Supercapacitors are used in cyclic applications at high C-rates owing to their low internal resistance, high round-trip efficiencies, and outstanding cyclic endurance. In the supercapacitor world, a 3000 F cell is one of the top products by which the state of technology is often gauged.
Skeleton, Eaton, Maxwell, and many other OEMs have a long history of product development and manufacturing to be internationally competitive and have 3000 F supercapacitors in their line of products. Maxwell recently updated its 3000 F supercapacitor cell for longer operational life, better power performance and lower cost.
I started my teleconference interview by asking Mahesh Godi to provide personal information such as his education and entrepreneurial experience. Mahesh appears to have a winning combination of excellent education, solid work experience and natural talent. He received a Master’s degree in Data Science and Engineering from Johns Hopkins University and studied Statistical and Machine learning at Stanford University. His employment history includes 17 years of software engineering positions at prestigious American companies like Apple, PayPal, Morgan Stanley and Bank of America. He is a seasoned inventor with numerous patents to his name.
BEST: Mahesh, can you briefly describe how your business was founded?
Mahesh: GODI was formed in January 2020 with a vision to enable the future of energy by making India independent in energy storage technology. We have a mission to make the world’s most sustainable batteries and supercapacitors.
What products do you make?
GODI India will manufacture 3000 F high-power supercapacitors at its Hyderabad facilities. Integrating GODI India’s supercapacitors with battery packs would improve battery life in EVs and renewable ESS applications.
We produce cost-effective and plant-based carbon-carbon supercapacitors using water-based electrode processing. We have a variety of supercapacitor products ranging up to 3000 F. At present, we are in the process of developing high-voltage lithium-ion capacitors as well.
Kindly elaborate about your supercapacitor products. I want to start with activated carbon, as this material is indispensable for all types of supercapacitors.
We are using different bio-waste-derived activated carbons available in India with a specific surface area of 1500-2000 m2/g, which is competitive and promising compared to the internationally well-known brands currently being used worldwide.
Electrolyte. Is it organic or aqueous?
We are using an organic electrolyte formulated in-house.
What metal do you use for the current collectors, and how do you reduce an interface resistance between the active material and the metal?
Aluminium foil with a specific thickness and surface area is being used as a current collector. A particular grade of aluminium has been selected to reduce the equivalent series resistance (ESR) of the current collector. The thickness of the current collector, active material thickness (loading), active material porosity; and separator with desired porosity, with specific thickness, have been optimised to reduce the interface resistance of the cell.
Please describe the housing material and production technology used to assemble the supercapacitors:
The housing is made of aluminium. We have a 50 kWh semi-automatic production line and are planning to upscale the production capacity to 200 kWh this year. We are following an environmentally friendly water-based slurry preparation to make the supercapacitors at GODI.
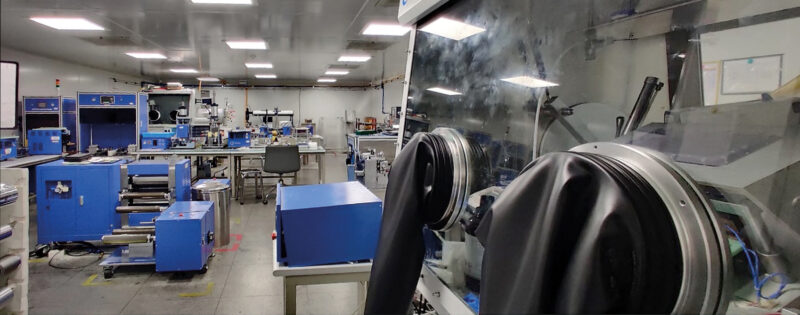
What testing and equipment do you use to validate your products?
We have good in-house capabilities for testing and validation. Moreover, we are collaborating with several OEMs and testing agencies for field testing of our product.
Tell us about your supercapacitor performance and other characteristics:
The baseline characteristics are as follows:
- Capacitance: 3000 F
- Rated voltage: 2.7 V, surge voltage: 2.85 V
- ESR: less than 0.20 mOhm
- Operating temperature: -40 to 65oC
- Specific energy: 3.08 Wh/kg
- Specific power: 6.2 kW/kg
- Life expectancy: 500,000 cycles
- Weight: 480 g.
Could you describe your strategies to reduce ESR?
We have implemented a tab-less cell design and proper welding of the current collector directly with the positive and negative terminals. Specific grades of the aluminium current collectors and cell cases have been selected to reduce the ESR. The thickness of the current collector, active material loading thickness, active material porosity and separator with desired porosity with specific thickness have been optimised to reduce the ESR of the cell.
Almost all existing supercapacitor OEMs have supercapacitor modules in their product lines. Please describe your plans for them.
We are collaborating with several OEMs and module manufacturers to design supercapacitor modules per the customer’s requirement.
Skeleton has recently introduced a SuperBattery to fill the technology gap between a lithium-ion battery and EDLC supercapacitor in the energy storage market Describe your metal-ion supercapacitor.
The metal-ion capacitor is one kind of hybrid capacitor, where capacitance is contributed by both EDLC and Faradaic reaction. The carbon/carbon supercapacitor utilises only EDLC capacitance and provides energy density in the range of 5-7 Wh/kg.
In the case of metal-ion supercapacitors, both EDLC and Faradaic reactions produce a high energy density of 40-50 Wh/kg along with a power density of 5-8 kW/kg.
We are currently developing a metal-ion capacitor that would offer a power density of 5 kW/kg and an energy density of 40-50 Wh/kg. The metal-ion capacitor will be designed with a rated capacitance of 2000-9000 F depending on customer requirements, offering a working voltage of 2-3.8 V.
Provide examples of applications for your supercapacitors, such as for synergetic work with batteries and alone.
There are numerous applications such as diesel engine starting, uninterrupted power supply, electric vehicles, regenerative braking systems, energy recovery for elevators, wind turbine pitch control, high inertia motors, automated guided vehicles, and solar batteries. We are pursuing the following markets: electric vehicles, ESS, engine cranking, and speciality applications.
Why are you in these markets?
GODI is a technologically innovative organisation focused on the R&D and manufacturing of lithium-ion batteries and supercapacitors. We are tenacious in achieving a zero-carbon footprint by promoting and adopting environmentally benign technologies in the fastest and safest way possible.
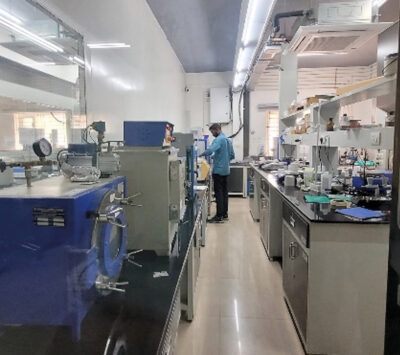
As the world is moving towards renewable and green energy solutions, we need to store the generated energy from different sources in more efficient ways. A supercapacitor can store energy without any faradaic reaction and provides a life of 10-15 years. Supercapacitor electrodes are made of bio-waste carbons. India is a large producer of agricultural bio-waste that could be converted into supercapacitor-grade carbon.
Additionally, India is a major producer of aluminium. Hence, we are manufacturing supercapacitors with indigenous technology, resourcing all the raw materials within India. Hybridising the battery and supercapacitor can enhance the battery life by 3-4 times at least, reducing the carbon footprint by limiting the battery waste.
India is a tropical country and experiences a warm to hot and moist climate year-round. Hence, we need to develop an energy storage or power delivery technology which can tolerate a wide range of temperatures and humidity. In that case, the supercapacitor is a suitable candidate to address these concerns.
Please describe your production processes, equipment, and strategies in your fight against climate change.
Our goal is to make innovative and environmentally-friendly products for our customers. We are working on products that may not require toxic solvents for manufacturing. We have demonstrated dry coating technology by making cell and supercapacitors. We want to utilise the technology in our commercial manufacturing facility in the future, which may lead to toxic solvent elimination from the cell manufacturing process. For supercapacitors, we are using waste raw materials from agriculture, which may reduce the dependency on imported raw materials.
What about your laboratory capabilities, including equipment and information about scientists, patents, and publications?
GODI has an R&D laboratory and pilot production facility in Hyderabad to develop innovative products in the field of supercapacitors and lithium/sodium-ion cells. We have more than 25 PhDs in our team working on cutting-edge developments in rechargeable cell technology. We have a team with more than 300 years of cumulative work experience in R&D and manufacturing operations.
We have a cell manufacturing facility in Chennai in collaboration with CSIR-CECRI.
The GODI team has filed 14 patents, and five are under immediate filing.
What strategies do you use to develop, retain, and increase your customer base?
By providing the best quality product and outstanding after-sales services.
How do you see the future of your company in India and abroad?
GODI is the first company in India to have made large-sized supercapacitors. GODI will eventually grow as one of the largest companies in India for supercapacitors and next-generation hybrid capacitors for various applications. GODI also has plans to start operations in the US in the near future.
Mastering the art
GODI masters the art of making contemporary supercapacitors and make a valuable contribution to India’s energy storage solutions. The characteristics of its 3000 F supercapacitor are almost in the same ballpark as the world’s leading brands. They can easily improve the specific energy and life expectancy by implementing an activated carbon with a higher iodine value and sustainability. The ESR is good, which is a testament to a high level of manufacturing technology.