Innovation in battery recycling is needed, it seems. Scooters left lying on the streets of Brussels paint a vivid picture of the care and consideration taken over this high-tech form of transport. Could this level of care be part of the reason for the proliferation of lithium battery fires that were being discussed at the International Congress on Battery Recycling (ICBR) held this year in Salzburg. Vic Giles asks if lithium batteries should be treated as the ‘problem child’ of the battery industry.
There is no doubt in the mind of this writer that lithium batteries have the potential for great good, but also great harm. The ‘problem child’ needs to be well managed if society is to be spared the worst of its behaviour.
In his opening address at the International Congress on Battery Recycling (ICBR), the chairman of the steering committee, Arie de Jong, set a challenging, if somewhat dismal, scene for the state of lithium battery recycling in Europe.
“Expect new challenges,” he said. “Who among us dared to predict last year that an energy crisis would hit a large part of Europe? CO2 targets are untenable for many countries, as we rely again on high CO2-emitting fossil energy sources. In addition, the price of energy has exploded, which is a huge burden for the battery industry, since a lot of energy is needed for processing discarded batteries.”
He said the capacity for recycling lithium batteries in Europe is very limited. Last year there were several calamities that worsened the situation.
“For collecting organisations, it is a huge challenge to have to collect the batteries to be recycled because the factories cannot take them in for processing after calamity.
“And speaking from experience, I know that lithium iron phosphate and lithium thionyl chloride batteries are hardly processed by any European recycling plant.” Exporting lithium batteries for processing outside the OECD countries has become virtually impossible as authorities increasingly classify them as hazardous waste with all the associated restrictions, he added.
He went on to say that battery regulation is another challenge facing EU countries. New battery categories will be defined in terms of waste, battery passport, use of recycled materials, carbon footprint, recycling percentage of various materials, and strict rules for industrial batteries and collection percentage for portable batteries of 65%. And that is very far away from the actual result of many compliance schemes.
“Also, safety is a huge challenge,” he said. “Fires caused by lithium batteries are reported from all around the world. We can’t get around it. There’s work to be done in many areas to increase the safety around lithium batteries. Of course, lithium batteries should be prevented from ending up in household waste, scrap collected or anywhere else where it does not belong. There are also measures employed at collection and sorting companies and fire detection is necessary. Discarded e-bike batteries are often identified as the cause of fire.”
Innovation in battery recycling is needed, he said. Many materials are still being lost and the upcoming battery regulation in the EU will probably require a high recycling rate.
EPAC battery reverse logistics
When it comes to portable batteries it is the reverse logistics that presents one of the greatest problems for the recycling industry (Fig 1). Getting many millions of portable batteries back to collection points relies firstly on consumers realising the inherent value of the cell and being motivated to return it for recycling. Secondly, it must be a safe process because we’re talking about class-9 waste, the state of health of which is often unknown.
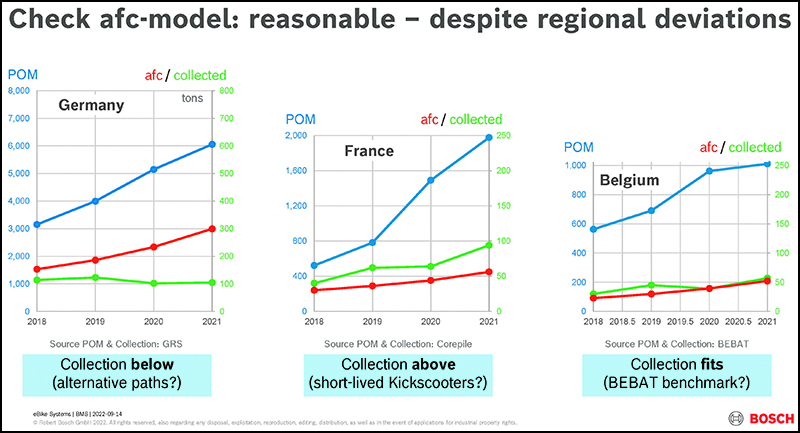
For example, electrically power assisted cycle (EPAC) sales are forecast to double that of cars by 2030 reaching some 30 million bike sales per year. With a usability average of eight years, a hoarding average of three years and an average collecting point retention of 0.8 years, estimates show it will take around 20 years to collect all ‘available for collection’ batteries.
Gunter Flinspach, eBike systems, management consulting (BMS) at Bosch is adamant that packs should not be repaired. He said these are hazardous goods stored in houses. “Batteries are very compact, as they are a lifestyle product – this leads to batteries being made as safe as possible, which leads to a problem when opening, repairing and closing the battery. This has an impact on safety and certification, which will be lost upon opening.
“There are consumers who think the battery is an investment rather than a consumable. This also leads to hoarding of used battery packs.”
Flinspach told BEST that batteries have software built in that, and when a fault is detected, it can disarm the battery; it could then start a deactivation process and notify a collection agent that the pack is available for dispatch to a recycler (3D battery recycling might catch the imagination).
The pyro vs hydro question
Bart Verrecht of Umicore said: “It’s not pyro vs hydro, it’s always a combination of a certain type of pre-treatment of which pyro is an example; followed by a further hydro refining of the alloy or the black mass that is produced. The type of pre-treatment, your performance and efficiency determines the yield of your valuable metals – so the economics. It also determines the ease, cost and complexity of your further hydro processing (Fig 2).
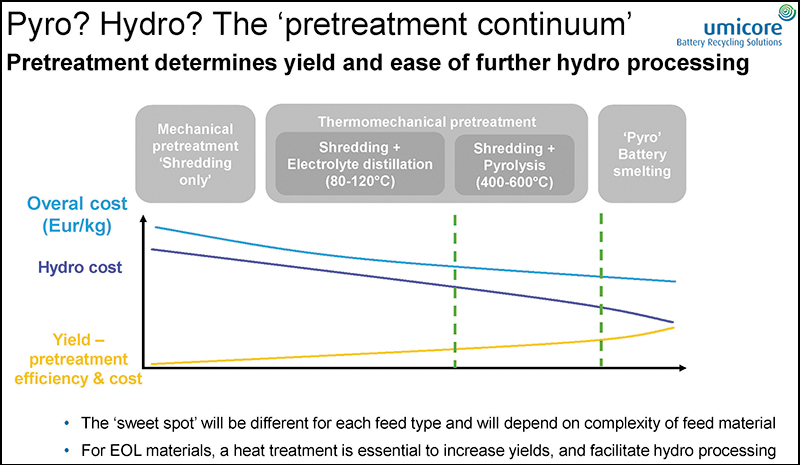
“If you cut your batteries to pieces in a shredding process you will inevitably lose some of your precious metals (Ni, Co, Li) in the different side-streams and those losses can be significant (up to 5-10% of these important metals).”
Umicore admit to having created the market perception that tends to favour hydro over pyro processes in terms of CO2 footprint. However, this is often based on incorrect, incomplete, or outdated LCA claims, said Verrecht. “We are likely partly to blame for that at Umicore. In 2007 we actually wrote a patent describing a shaft furnace for battery recycling, which required a large amount of coke and that’s what we call the old pyro process” (Fig 3).

The new process uses the chemical energy from the battery to deliver energy for the process and also act as reductants. No external energy is needed and excess energy is created for uses such as heating and the hydro processes.
“Sustainable battery recycling is key for the transition to sustainable electric mobility. Both pyro and hydro flowsheets have challenges and opportunities towards decarbonisation, but the lowest end-to-end CO2 footprint is obtained through a smart combination of pyro and hydro,” said Verrecht.
Composition of black mass
Tobias Elwert, global expert in battery recycling technology at BASF, evaluated the metallurgical process options for black mass. He said: “Black mass is a mixture of the electrode active materials contaminated with a wide range of impurities.” As there is a wide range of cathode active materials (NCM, NCA, LCO, LFP, etc) and graphite/silicon on the anode side, it follows that the chemical composition of black mass can vary considerably (Fig 4). The main impurities are aluminium and copper from the electrode foils, then flourine and phosphorous from the conducting salt and certain plastics. Depending on how you source and produce the black mass you may also have different types of organics along with elements from mis-sorted batteries (Cd, Pb, etc).
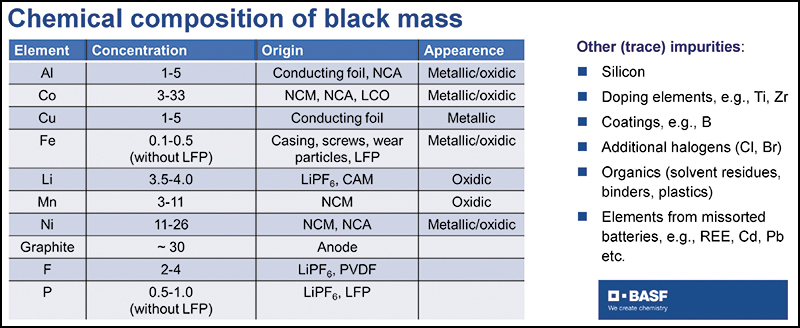
If black mass is thermally treated the organics can be destroyed, along with the CAM structure, which means different leaching conditions are required in the subsequent hydro stage.
In the co-processing of black mass, Elwert said: “You use organics and graphite as reductants. I know this is controversial but, as Bart said, as long as we don’t have industrial solution for graphite recycling I would also see it as an advantage of this type of process.” The disadvantage is that without prior separation lithium is lost due to dilution in the slag, which means the process will be unable to comply with regulatory requirements for element-specific quotas. “Without these types of adaptions… these processes will disappear from the market.” The highly corrosive content (lithium and flourine) treatment of the feedstock and a comprehensive off-gas treatment means smelting capacity is limited.
Elwert said that in Europe there is a trend towards shredding under N2/drying, which means the majority of black mass is not optimised for direct hydrometallurgical processing. However, the majority of planned investments in Europe are hydrometallurgical plants aimed at producing battery-grade chemicals.
How to decrease carbon footprint
The electrification project is all about reducing carbon footprint. But how much difference does it make? And how much effect does recycling have?
Professor Mari Lundström of Aalto University said that recycling can fulfil <10% of raw material needs for batteries in 2030 (~50% in 2040). Mining and primary production in the EU need to be enhanced, all recycled battery materials and pre-production scrap will need to be accessed, and consumption needs to be reduced.
Battery recycling processes need life-cycle analysis (LCA). All input of a recycling process must have an output, from the current collectors and active materials to the binders, separators, electrolytes and casings.
Research at Aalto University shows that using hydrometallurgy to treat 1kg of battery waste in LIB-NiMH recycling would generate ~4kg CO2-eq. The burden came mostly from the neutralisation chemicals. The burden to produce the equivalent materials from primary product was ~6kg CO2-eq. To improve on this saving they looked at removing Al or Cu prior to leaching. The results can be seen in Fig 5. A major reason for the saving is that virgin aluminium production is an energy-heavy process.
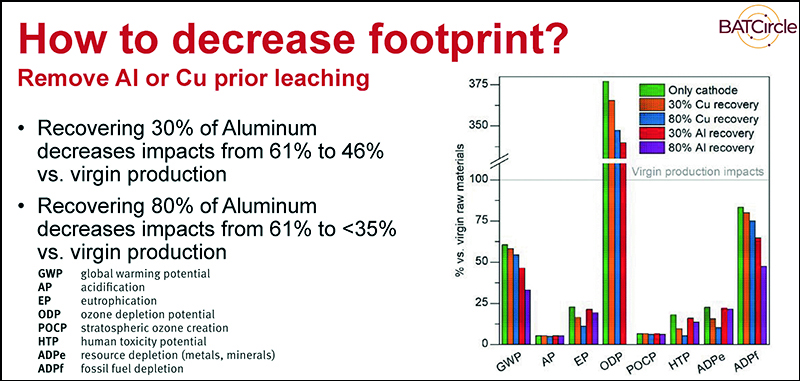
Project ReDesign
At present LIBs are designed for manufacturing and application, not recycling. Sebastian Hippmann of Fraunhofer said: “It is not possible to meet the raw material demand for Ni, Co, Li through mining alone. The concentration of these critical metals is so high in batteries we must have urban mining to secure the materials. Distinctive fractions are the necessary materials for the production of new batteries. In an ideal world, these will be easy to produce and more cost-effective for producing new batteries.”
Call it what it is – not to do this is short-sighted and damaging to the very environment EVs are trying to save. Crushing and shredding battery packs results in contaminated fractions that present difficulties in purifying. “At the end-of-life (EoL) state of the battery it can be more cost-effective for the producers when the cost for recycling is lower because of the better recycling concept in the design,” said Hippmann.
New trends are not always positive. Cell-to-body raises more transport, safety and separation issues. The complexities of all-solid-state batteries are still being investigated. The foam packing materials used in the Tesla Model Y mean the pack is very difficult to disassemble. ‘Better batteries’ may not always be best, there is a trade-off between performance, lifetime and recyclability.
However, EPR means that the producer is responsible for the cost to recycle the battery at EoL. The more complex and difficult it is to recycle the battery, the more that will be paid to the recycler – this is independent of the value of the battery. That cost, of course, will be passed on to the consumer who will have little option or say in the matter.