Multiple stages of development are required before bringing a technology to market and the battery industry is no different. The technology readiness levels, just before commercialisation, can be the most difficult to navigate and fund. The opening of the UK’s Battery Industrialisation Centre (UKBIC) on 15 July, sees the gap between research and commercialisation being given due attention. BEST visited the plant in Coventry, UK and spoke to managing director Jeff Pratt to learn more about the facility.

UKBIC is a publicly funded battery manufacturing development facility that provides the missing link between battery technology, which has proved promising at the laboratory or prototype scale, and successful mass production. It is a key part of the UK Government’s Faraday Battery Challenge, which was created to fast-track the commercialisation of high-performance, low-weight and recyclable batteries that are durable, safe and cost-effective.
Firstly, the Faraday Institution harnesses the strengths of the UK’s research base to create and demonstrate new technological solutions. It manages the research projects of universities and institutions around the UK, getting them working together, rather than in competition.
Secondly, following on from the research projects, Innovate UK draws together specialist universities and academia to create marketable solutions and products. There are more than 120 organisations and 464 collaborative R&D projects so far.
Thirdly, there is UKBIC, which covers the entire production process from electrode manufacturing, cylindrical and pouch cell assembly, cell formation, ageing and testing, as well as battery module build and full battery pack assembly. It is an open-access facility— welcoming manufacturers, entrepreneurs, researchers and educators— that can be accessed by any organisation with existing or new battery technology— if that technology will bring green jobs and prosperity to the UK. However, it is also a commercial business.
The facility allows organisations to prove whether their promising technologies can be manufactured at the required volume, speed, performance and cost to be commercially successful.

Clients can bring their own employees to work with, and be trained by, UKBIC staff on the production line. Customers can also integrate processes unique to their own products into the facility on a temporary basis. Help can be given to building bespoke production lines at UKBIC to enable customers to prove higher throughput production in the early stages whilst they prove their business cases or build their own production lines.
Built for such a time as this
In 2018-21 the UK invested £130 million ($180 million) into the Battery Industrialisation Centre— because the size of the entry ticket into battery manufacturing is so large. Who could have foreseen the COVID-19 pandemic that would make this decision so important to the UK’s battery industry? Staff at the Centre worked on the facility throughout the pandemic, despite all the challenges being thrown at them.

UKBIC occupies the space between the commercial laboratory, or specialist university, with a pilot line and the gigafactory. The equipment at the plant is exactly the same ‘industrial rate’ as you’d find in a gigafactory but comprises one-off production lines rather than the multiple lines of a gigafactory— which is why it is called a manufacturing development facility. The Centre operates at the technology readiness levels TRL7-8 and manufacturing readiness levels MRL5-9, helping companies get over the line and into the market. It has electrode, cell, module, and pack manufacturing capability at an industrial rate. It is 20,000M2, about the size of three football pitches. A 30GW gigafactory would be 30 to 35 football pitches and cost in the region of £2.4 billion ($3.3 billion).
The remit is to develop new manufacturing processes and support new material development, and new cell, module, or pack structures— reducing the risk of high-volume manufacturing development. The Centre is open access, so anybody who’s currently in the UK, or looking to invest in the UK, can use the facility. The Faraday governing body determines whether a corporation can use the facility, according to whether it will benefit the UK.
However, although the Centre can produce marketable cells and batteries it is intended to operate as a commercial venture with funding from companies using the facility. Owning IP is not part of the remit for UKBIC, working with, and protecting, companies’ IP is. Jeff Pratt, managing director of UKBIC, said: “UKBIC does have some IP that it has developed, and companies are able to use that, but any IP developed through the facility by a company is that company’s IP for them to take away— it is not shared. That’s one of the key principles for this facility— to support, not to compete.”
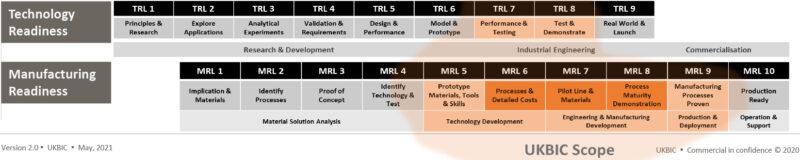
Training
We all know that there will be a seismic shift in transport as internal combustion engine vehicles, powered by diesel and petrol, are replaced with cars/vans powered by batteries. Britain plans to ban the sale of new petrol and diesel cars/vans from 2030— five years earlier than previously planned. This is part of the green revolution to cut UK carbon emissions to net zero by 2050.

Pratt said: “At UKBIC we want to inspire the next generation to get involved in this exciting technology that will transform the way we live, work and get around; help to clean up the air we breathe and stimulate awareness and knowledge. Therefore, here at UKBIC, we want to ensure that we have the right fundamentals in place for training programmes for those working in the battery sector.”
In its 2020 Gigafactory Study, the Faraday Institution projects that the UK will have domestically located electrode, cell and battery pack manufacturing. In this scenario, the overall industry workforce of the automotive and EV battery ecosystem would grow by 29% from 170,000 to 220,000 employees by 2040. This would replace the similar number of jobs the UK expects to lose from engine manufacturing and its supply chain. These estimates assume that an average of 180 battery manufacturing jobs are supported per GWh per annum.
Pratt said: “The ‘green industrial revolution’ promised by UK prime minister Boris Johnson in the 10-point plan hinges on upskilling, and it is this potential for growth which is something we are looking to develop, in conjunction with industry, the education sector and government.”
Industrial Skills Framework
Working in tandem with Warwick Manufacturing Group (WMG) and engaging with key stakeholders, UKBIC is creating an industrial skills framework (levels 2-7) (technical/degree apprenticeships) for the UK battery manufacturing industry.
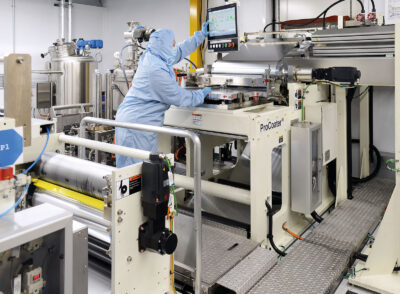
“Using our knowledge and understanding of the sector, we are working to develop and enhance the nationally accredited trailblazer apprenticeship programme with a focus on battery manufacture, maintenance and quality assurance— something we expect to have in place by the 2nd half of 2021,” said Pratt.
“These programmes will be key to stimulating jobs recovery, in an economy devastated by the coronavirus pandemic, while transitioning to net-zero greenhouse gas emissions, as we transition to battery-powered vehicles.
“Additionally, we will work with client organisations to deliver bespoke training based around short modular courses, to up-skill new recruits and cross-train existing employees. We can offer clients unique, hands-on access to production equipment used in all stages of the battery manufacturing process including electrode manufacture; cell assembly; formation ageing and testing; and module and pack assembly.”
What can be produced?
The facility is designed to support the growth of electric vehicles and fast-track battery technology for use in rail, aerospace, industrial equipment, automotive, off-highway and static energy storage. The initial set-up is for the development of lithium-ion batteries, but it is future-proofed to run the chemistries that are just coming into manufacturing. The Centre has been equipped with the latest in battery manufacturing plant and machinery for the creation of pouch (stacked) and cylindrical (wound) cells.
- Manufacturing up to 690 mm width
- Simultaneous double-sided coating capable
- Coating weights of 5-250gsm
The process equipment overview, below, shows the layout of the facility.
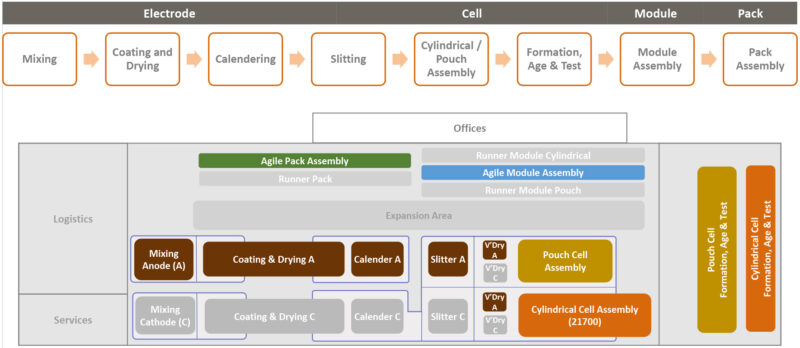
The facility can cope with NMC 811 chemistry. The Centre has developed a product for NMC 622 chemistry— so the facility can be benchmarked and improved. The facility has been protected in terms of development as it’s capable of NMC 811, and higher, nickel chemistry.
The facility has an expansion area, which can be seen in the overview diagram below. The space is protected so they can go to another format or solid-state as required because technology is continuously moving.
In terms of electrical manufacturing equipment capacity, the Centre has about 2-3GW worth of capacity, which is what you get off one pair of industrial electrode lines. And then moving on to the cell assembly, they’ve got a pouch assembly line, which is capable of 300mm by 100mm pouch cell. They have the machinery capable of producing the 500 by 100 but haven’t bought the associated tooling for that.
Pratt said: “As we were going through the process of designing, ordering and getting the equipment built, the industry started to require the bigger pouch cells and the driver for that was really to get the cost of the battery packs down. The car industry at the moment is really pushing to reduce the cost of these batteries. The size of this large pouch, 500 by 100, is two cells side by side and you’ve got the width of the car, that’s the logic. And the reason for going for the biggest cell is cost; having fewer components drives the cost down. That’s what they’re looking to do.
“We’ve actually designed a 300 by 100 cell, so we can run through and commission this facility. And we’ve got 21700 cylindrical cells, which is obviously a Tesla. And again, we’ve designed our own 21700 cells with NMC622 chemistry, because we can go out to the market and buy one. And we can build our own, put it through the process of benchmarking against one bought commercially from outside and ask ourselves: ‘does it look comparable?’ So we can confirm that the process is good and that was the reason we designed our own cells. We have a vacuum chamber to check for leaks throughout our process.”
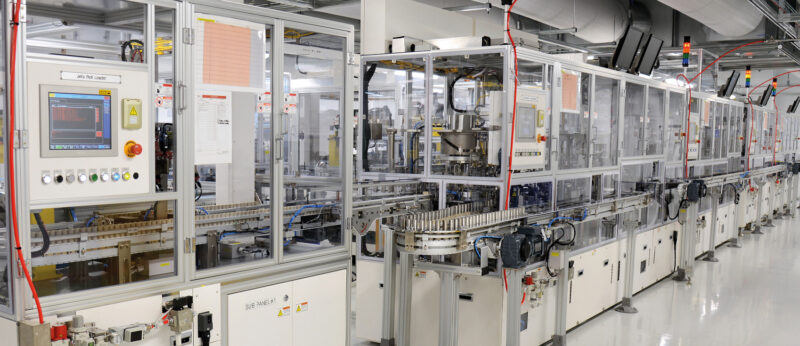
Ageing safely
During the formation and ageing, the cells are continuously monitored to detect any error caused in previous steps. In cell manufacturing, the production system works on a ‘no faults forward’ methodology. The formation equipment at UKBIC supports research into reducing formation times and temperatures, with optimisation of test protocols and related parameters.
For ageing, the cells are put through the charge/discharge cycles, or pre-initial charge, initial charge, and final charge, and then stored in a high-temperature box and a normal temperature box for 19 and six days respectively— probably the longest ageing cycle anywhere in a battery company. The reason for doing that is to start the process of forming the layers in the cells.
“In the ageing process what you’re really doing is a bit of the chemistry being finished off and then you’re ready to confirm the quality,” said Pratt. “This is ionic transfer going on in here and this part of the process has to be managed to keep it clean because if you don’t and you have contamination in there you get the contamination all coming together and forming a pyramid shape. The risk here is it pushes through the separator and you get a short— you get a thermal incident. We’ve got to be able to deal with an incident if we get one in here— so the fire systems in there are far and above what you’d see anywhere else. There’s segregation and sniffers in each zone. You can fill it with N2, which sometimes puts it out, or you can drench it with water. The water always does extinguish the fire, but you’ve lost the product.”
We’ve got to be able to deal with an incident if we get one in here— so the fire systems in there are far and above what you’d see anywhere else.
The cells and pouches are placed in the ageing racks by cranes, which are equipped with an infrared camera scanning up and down looking for anything getting hot. If it sees anything the crane takes it out and puts it into a hot box that shuts and you can just do a localised hit with N2 and then water— a staged safety. The crane does two operations, when it’s not loading or moving cells at a designated time to the next area, it’s still moving and scanning conditions continuously. There are also highly sensitive sensors in each zone, if a little bit of smoke in the vents gets through, that’s enough to trigger an alarm. “You can’t see it or smell it but it’s enough to set these sensors off. Each of the racks is enclosed in a two-hour firewall. These are segregated and enclosed in a one-hour firewall. Then you’ve got N2, you’ve got water, you’ve got the sniffer system, and you’ve got the infrared camera and the hot box. We call it 300% safety, so you’ve got three times the safety you need,” said Pratt.
At the end of the line cells or pouches can be assembled into modules and packs. Normally the pack design will be unique to the application.
Scale of operations
The process equipment overview shows one cathode and one anode line, and two cell assembly lines— one for pouch cells and one for cylindrical cells. This is the minimum necessary to prove the industrialisation processes. And then there are the formation and ageing areas for the pouch and cylindrical cell types.

Pratt said, “If this were a gigafactory, this would all be laid out in one line but we wanted to keep the building a reasonable shape so we looped it back in a horseshoe. We put an agile module assembly system in so we have a facility that can cope with a lot of different sizes, and different cell types, in different forms.
“In terms of cell capacity, we can do up to about three cells a minute on the pouch line and 20 cells a minute on the cylindrical line. In terms of capacity, we can do about 50 modules a shift, 150 in a 24-hour period. That equates to seven or eight 130kW packs a day, more if they are smaller. If it was cars we could do up to about 5,000 cars a year. We could probably cope with a niche volume sports car or a luxury car. Companies could come and use this just to make batteries.”
Container manufacture and design are not the focus at UKBIC. However, through their range of academic and industry connections, they can introduce people specialising in these areas. Likewise, with battery management systems, it depends on where demand arises and what partners request. UKBIC are open to a wide range of discussion and opportunities.
UKBIC customers
UKBICs customers potentially come from all sectors but around 90% of the discussions they have been having are with organisations that are automotive. One of the drives is to increase the breadth of support offered into the sector so they support aerospace, rail, marine and all types of stationary storage. The stationary storage market is forecast to be as big as the automotive market, eventually.
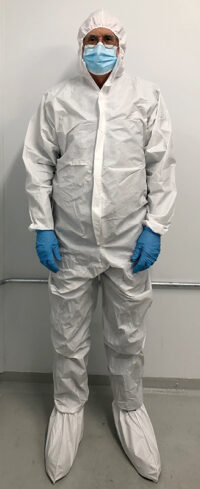
Pratt said, “We want people to come and put work through here because that’s why we’re here, but we want to get as many companies through to help as many companies as we can. So if we tie up with one company we’re not really achieving the goal of trying to generate a big battery manufacturing industry in the UK. So we’re always a little bit careful. We’ve got a governance structure, which actually manages that link back into government and government has a big say in what the facility is used for.”
The Centre supports all partners because of the UK’s demand for grid storage, both commercial and domestic. Pratt said: “There are companies— such as football grounds— that do nothing for two weeks and then they’ve got a home game on a Saturday. At that point, they need a lot of energy, so they pay massive line charges because they’ve got to have the capacity for when they’re in the match. So a lot of football companies now trickle-charge storage all the time. And then they use the battery storage on match day. So companies are investigating that sort of thing.”
Another area generating significant interest is autonomous robots or AGVs (automatic guided vehicles). These are used for applications such as warehousing, where machines can operate autonomously. As necessary, they go back and charge themselves, so people don’t have to worry about them.
Pratt said: “We’ve had discussions with most of the tier-one battery companies, and we are actually quoting to do some work with some of the earliest stage potential battery companies that are up and coming at the moment.
“We also work with the battery supply chain development. If you look at the total cost of the battery, the manufacturing cost is only about 20%. So if you have a gigafactory— and you need it strategically because you need that to draw the supply chain— manufacturing is about 20% of the cost of the battery and 80% is in parts in the supply chain. About 40% of the total cost of the battery is in the electrode.”
Waste management
The sustainability of batteries is at the heart of the government’s 10-point plan. UKBIC is taking a whole-life-cycle approach to assessing the sustainability of its batteries. This approach enables them to be sure that by fixing one issue they are not creating more issues elsewhere in the value chain. You can’t get away from the fact that battery production requires high energy use and UKBIC is actively trying to find ways to reduce energy consumption.
Waste from the facility is not recycled on site, it is taken offsite by a third party, who recycles up to 80% of all of the site waste, with the rest sent for energy usage. However, there are several projects on-going and there are plans within those projects to look at how they recycle waste materials. Pratt said: “I would like to have a waste recycling facility prototype close to this facility because we need to be able to make this circular. Most material waste is produced during the electrode manufacturing stage.”
UKBIC is also involved in project ‘RECOVAS’ which has grant support from the UK Government’s Advanced Propulsion Centre (APC UK). RECOVAS brings together partners across the whole value chain. Its objective is, to set up a circular value chain for electric vehicle batteries— by providing a reliable route for repurposing and recycling lithium-ion batteries— at a scale that can match the expected sales of electric vehicles in the UK. The recycled materials can then be used in new battery production. Waste from UKBIC will be used in this project to look at the recycling potential of waste material and to put this material back into the supply chain.
A sideways glance
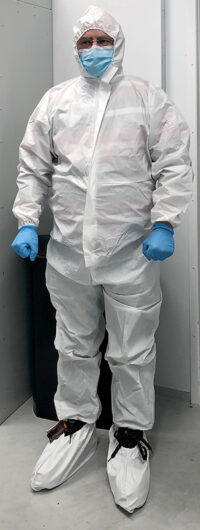
Power management innovator Chris Hale takes in the view at UKBIC and finds a facility well prepared for lithium battery cell development.
With demand for EV batteries produced in Europe predicted to reach a total of 1,200 gigawatt-hours per year by 2040 (Wallenius Wilhelmsen), sufficient to require 80 gigafactories, the UK needs to step up to the mark in order to rival other European leaders, such as Northvolt and ACC (Saft/PSA Group), in the battery manufacturing race. At present, European cell manufacture only accounts for 7% of global capacity, although the expectation is for 25% of global pipeline capacity by 2030 (Wood Mackenzie). Therefore, it has to be said that UKBIC’s mission to enable industry, through open access— to validate scale-up and commercialisation of advanced battery technologies— is truly admirable. Although initially focused towards the automotive sector the potential is far-reaching and, for the UK to have a facility allowing promising early- and mid-stage research and development to feed through to scale-up and commercial exploitation, is without a doubt essential for UK growth in the industry.
Reducing the cost of cells
Cost, of course, is a major driver for leading the cell race. If we consider lithium-ion was $2,000/kWh in 2000 and is now in the order of $200/kWh, significant gains have already been made. However, there are still a number of areas within cell manufacture that could be optimised to drive down manufacturing price overall— this accounts for around 25% of the cost of LIBs (Kwade et al. 2018). From the analysis of different manufacturing steps: formation and ageing (32.16%), coating and drying (14.96%), and enclosing (12.45%) are the top three contributors to the manufacturing cost of LIBs (Yangtao et al). These high capital investment and labour-intensive processes are the most urgent fields that need to be studied.
With formation alone, the cells are charged/discharged under a low rate, gradually increased to ensure a stable SEI layer on the surface of the anode and then stored on the ageing shelves for SEI stabilisation. A step that normally lasts several weeks, and up to 25 days at UKBIC. The bottom line: manufacturing is one thing; enabling companies to use a facility to research and develop manufacturing processes is another. Supporting companies working to improve cell technology, and techniques, to drive down cost and improve performance is surely a great enabler for the UK battery industry on the whole.
Safety is paramount
This all being said, another key factor that mustn’t be underestimated is the focus on safety. Over all the years I’ve spent within the battery industry, I’ve sadly had first-hand experience of a number of battery-related fires at factories and facilities— an issue that is constantly reported on, and ever-present danger, such as the recent event on the 30 June 2021 at a facility in Illinois, US, where a 100-ton lithium-ion fire raged for three days. Fire-fighting and containment were a real issue and the initial use of water ultimately shorted some of the battery packs causing further fire and explosion. If you add smoke damage and the impact of toxic fumes on personnel and the environment, lithium-ion fires can be devastating.
There is guidance however, the Fire Industry Association (FIA) offers advice for lithium-ion fire management, recommending action such as firebreaks between battery packs and fire-rated containment. Early detection though, is the first line of defence, allowing appropriate time to segregate the affected packs and cool the cells before thermal runaway takes hold. Detection methods such as off-gas detection (for enclosed areas) and sensitive thermal monitoring are both effective. It is therefore encouraging to see that UKBIC has taken an impressive stance on ensuring their facility is well protected with their 300% fire mitigation process.
Risk cannot be underestimated, even for cells apparently inertly sitting on a shelf.
Risk cannot be underestimated, even for cells apparently inertly sitting on a shelf. Constant cell monitoring, by incredibly sensitive thermal cameras, within UKBIC’s cell storage area as the first line of defence lends itself to the question of ‘how many detection events has it encountered to date?’ and ‘will this data be shared for highlighting the risk of cell failure to other facilities?’
A sustainable business model
In addition to all this is UKBIC’s business ethos, which in itself has to be applauded. Instead of focusing on revenue generated by production lines of its own cells, it is taking sustainable revenue from rental and education, with finite-duration agreements preventing any single company from taking up ‘residency’ to produce cells. This allows a continual turn-around of new companies or new development at a very high-quality facility. With plenty of scope for expansion, the facility should be able to grow and expand its area of expertise— not least of which are plans for a prototype recycling facility within the next few years. For me though, the key takeout from UKBIC is its attention to quality and safety. Cell failures still happen, so better cells, awareness and education across the industry need to happen, and where better than a facility such as this?
Cell failures still happen, so better cells, awareness and education across the industry need to happen, and where better than a facility such as this?