Brazilian Nickel, operator of the Piauí Nickel Project in north-east Brazil, is producing battery nickel via the heap leaching method. It claims it is a pioneering, low carbon approach to mining the critical mineral. Anne Oxley, chartered metallurgical engineer and founder/technical director of Brazilian Nickel, tells the story.
Nickel’s unique properties ensure it maintains a key role in various green applications. It enhances corrosion resistance in hydroelectric facilities and geothermal plants and, when used in lithium-ion batteries, improves energy density, battery longevity, and ensures the better overall performance of electric vehicles (EVs).
Elon Musk, arguably the most visible player in the sector, has endorsed nickel and reaffirmed its centrality to batteries used within EVs. Speaking in 2020, the Tesla CEO remarked that “our batteries should be called nickel-graphite, because it’s mostly nickel-graphite.” About 50kg of nickel goes into each Tesla battery. With a supply deficit predicted as early as 2027, Tesla “recognise their biggest risk, from a strategic supply point of view, is nickel,” according to Bloomberg.
The advancement of the global battery industry thus hinges on harnessing a secure and sustainable supply of nickel, which Brazilian Nickel is well placed to help achieve.
Sulphides or laterites
Nickel resources occur either as sulphides or laterites, the latter constituting three-quarters of global resources. Nickel laterites are currently processed, almost exclusively, through either a pyrometallurgical or a hydrometallurgical route. Most pyrometallurgical processes, notably ferronickel, nickel pig iron and matte smelting, require a high-energy-intensity smelting process.
Whilst high pressure acid leaching (HPAL), the primary method of hydrometallurgical nickel production, has a lower energy intensity than smelting, estimates suggest that for every tonne of nickel ore processed via HPAL, around 1.5 tonnes of waste is also produced.
Heap leaching is a well-established process for the treatment of other metals, including copper, gold, and uranium. In 2015, it accounted for one-third of global copper and gold production. Its use for the treatment of nickel laterites has, however, only had very limited application, despite it having the potential to be the lowest capital cost and most environmentally sustainable nickel laterite recovery process.
Its underrepresentation in the sector means its application is often perceived as relying on new technology. However, in practice it is the combination of well-known industry unit operations, standard equipment, and standard construction materials. Its relative simplicity allows for flexibility on a project-to-project basis, which can be optimised with the relevant industry know-how.
When compared to HPAL, heap leaching is less energy intensive as it operates at ambient conditions, has only dry residues and, because HPAL can only treat selective parts of the ore body, has much better resource utilisation.
The ore from the Piauí Nickel Project has excellent metallurgical properties for heap leaching, being high in silica. This results in fast leach kinetics, high nickel and cobalt extractions and, most importantly, low acid consumption. That cements the project as a highly viable, low cost, and low impact method of providing a vital resource for the green economy.
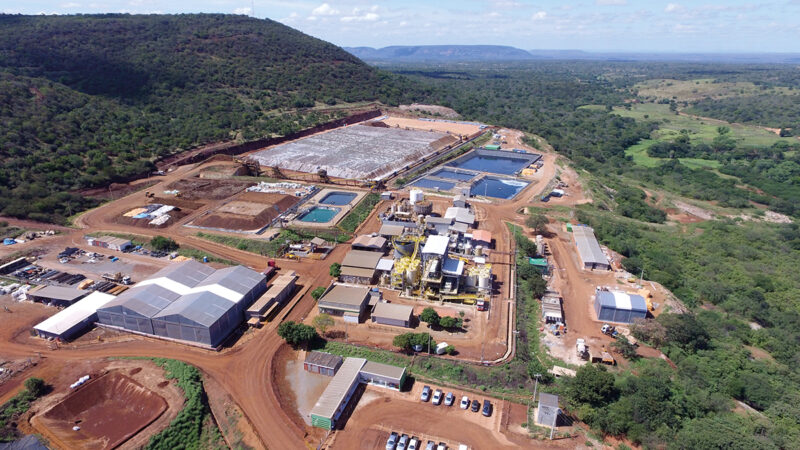
Heap leaching method
The heap leaching method involves various steps before a final mixed nickel and cobalt hydroxide product (MHP) is produced. First, conventional open-pit methods mine the resource, and then the ore preparation circuit receives, crushes, and agglomerates the ore. It is then conveyed and stacked on to the heap leach pads. The pads are constructed with a compacted layer of earth or clay with a synthetic liner on top, creating a double impermeable layer to protect the environment.
Acid-resistant rounded gravel is added to this to aid the percolation of the solutions to the collection system. The agglomeration step prior to stacking improves initial leach characteristics, allows for taller heaps, which reduces leaching of impurities and helps to achieve overall better extraction of nickel and cobalt.
Once the heap is established, the fundamental process of nickel laterite heap leaching is similar to its copper and uranium equivalents, although the technical expertise of the Brazilian Nickel team is key to optimising this method in the context of nickel laterites. Correct selection of application rate and lixiviant acid strength, along with a counter-current leaching, results in the selective leaching of nickel over iron and other impurities.
It in turn aids the reduction of acid consumption. Brazilian Nickel’s utilisation of an optimal heap height results in good reaction kinetics, appropriate selectivity in the leach, suitable neutralisation capacity and effective permeability. The optimal leach conditions are the product of extensive work over two decades.
The pregnant leach solution resulting from the leaching process is collected in ponds for further use in the heap leaching counter-current process or feeds the downstream processing plant. In the processing plant, the pH is increased to remove impurities from the solution before a series of ion-exchange units both remove further impurities and concentrate the value metals of nickel and cobalt into solution.
Intermediate nickel and cobalt
The process at the Piauí project was first developed at different pilot plant testing facilities globally, including in Colombia, Turkey, and the Philippines. This process was later replicated at the company’s own Piauí Nickel demonstration plant in 2016 and 2017. It highlighted that target nickel extractions could be met, and even exceeded, with low acid consumption and attractive leach kinetics.
Construction of smaller operation
As a final step before full-scale commercialisation, construction commenced in 2021 on a smaller operation, named the PNP1000. Production capacity is approximately 1,000 tonnes per annum of nickel contained in the intermediate MHP. The systems and processes at the PNP1000 are transferable to the full-scale operation. When nickel was first produced in June 2022, Brazilian Nickel’s heap leaching method was validated, and work could focus on replicating this process at the larger-scale project.
The company has produced saleable nickel that has since been qualified by various CAM customers including CNGR as very suitable for their process. It has also sold to other customers in both Europe and Asia, mostly for the battery supply chain. It has also technically been validated many times in its various funding rounds by independent engineering groups for investors. This is still ongoing for the full-scale funding but is almost at an end.
The transferability of the PNP1000 also extends to the workforce, who can now carry over their experience to the full-scale project.
Brazilian Nickel joined the Nickel Institute’s Nickel Mark pilot programme in March 2023. It is a spin-out of the more established Copper Mark programme and aims to demonstrate responsible practices, transparency, and accountability.
Full-scale project target for 2026
The company’s primary target is to achieve first nickel production at the full-scale project in 2026, and plans to replicate the project at other nickel laterite deposits, where it also hopes to incorporate CO2 reduction strategies. Other projects will follow, both in Brazil and elsewhere, including Australia and the US.
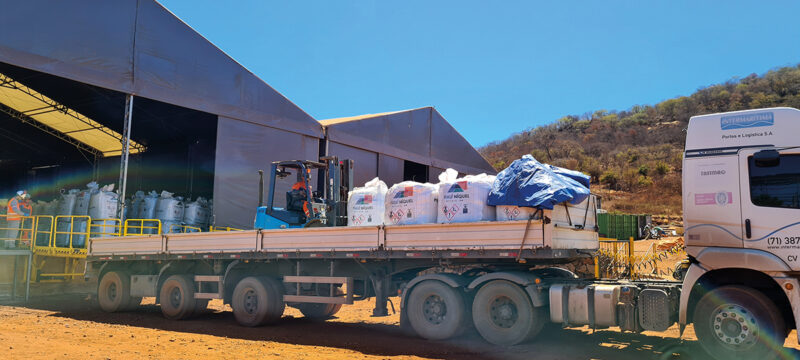