The 2024 Advanced Automotive Battery Conference (AABC), held in Las Vegas in December, drew a wide range of players in the battery value chain, from materials to recycling, manufacture and technology. Andrew Draper reports.
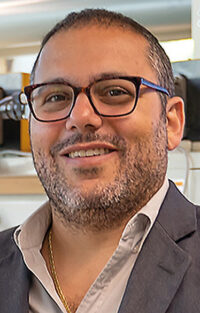
One issue facing battery manufacturers is achieving profitable battery manufacturing and meeting the competition. Tal Sholklapper, CEO of Voltaiq, gave a presentation showing the struggle to achieve quality. He asked why ramping up gigafactories takes years and costs billions of dollars.
You do not know cell quality until weeks after production, he said, and thousands of upstream processes, parameters, settings and tolerances have to be fine-tuned perfectly.
That can take dozens of iterations to get new production to full yield and throughput. Lots of costly scrap is produced as ramp-up takes place. “Delays in yield ramp can kill new factories,” he said.
It makes a system that it claims can identify quality anomalies “weeks earlier than standard quality assurance”. He said it can catch defects in hours and quickly diagnose root causes of issues.
Among battery manufacturers, Sakuú from California continued to push its 3D-printed battery and said it will be taking commercial orders from January 2025. It claims it has been successfully printing battery electrodes using customer-specific chemistries and that its Cypress Li-Metal battery cells are now reaching over 1,500 cycles (Fig 1).
The company is dry printing anodes and various cathodes from LFP and NMC electrodes, it said. This will also enable new chemistries such as aluminium-ion and sodium-ion, it said.
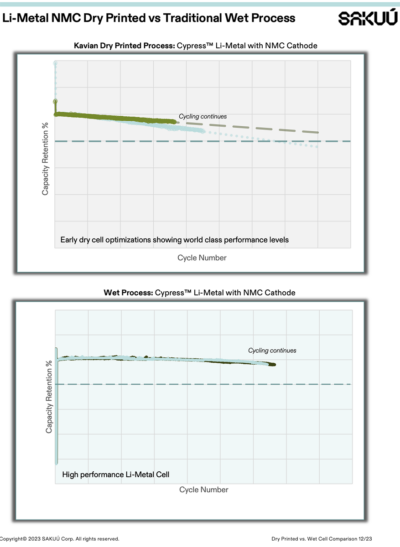
Sakuú’s high-energy, high-power lithium-metal battery cell chemistry is being augmented with its dry electrode Kavian process (Fig 2). The UN38.3 certified battery cell has achieved 1,500 cycles at 100% depth of discharge to 80% state of health at 0.3C/1C. It is claiming this as an industry lead in commercially ready lithium metal chemistry performance and up from 1,000 cycles at 100% depth of discharge in April 2024. It is securing new revenue-generating partnerships, it said.
In terms of emissions, the company is claiming:
- 55% reduction of CO2 emissions in electrode manufacturing
- 100% cut in toxic solvents and water compared to traditional wet coating
- 91,122 tonnes of CO2 emissions reduced per 3GWh/year R2R plant replaced.
Geopolitical mess
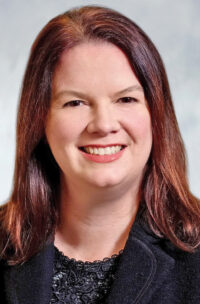
Addressing the question of supply chains in North America, independent consultant Kimberly Berman said fixing the lithium-ion battery supply chain – which she called “a geopolitical mess” – had to begin with domestic mining reform and mid-stream innovation.
She noted how automakers BYD and Tesla between them hold a third of the global market share. The US represents less than 10% of global market since 2020. Tesla is continuing to dominate the US EV market despite competition from GM, Ford and new players such as Rivian.
The supply chain of critical minerals remains at an all-time low, she said in her presentation. There are 50 minerals on the US critical minerals list: 12 are entirely based on imports and the country is 50% reliant on 31 of them. Key metals such as cobalt and copper are suffering price volatility, while mining and refining developments in the US are being impeded by cost and low prices (Fig 3).
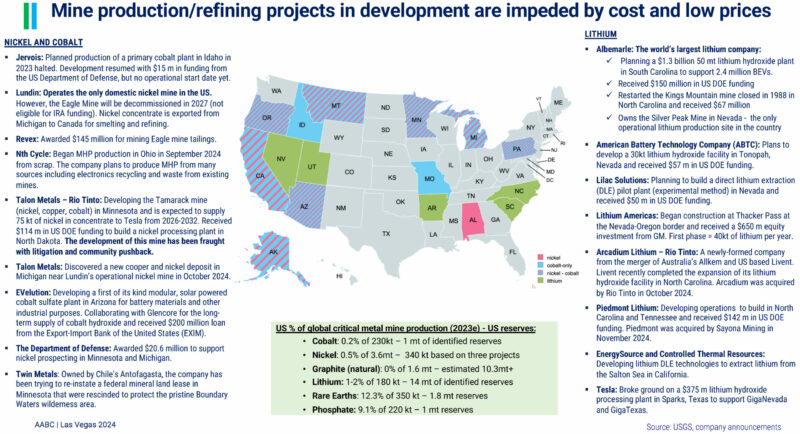
Canada to the north has plentiful battery metal reserves but lacks a cohesive mineral strategy, she argued. Provinces and territories compete with one another to win foreign investment.
Lithium production in North America is not yet cost effective, she said, noting the dominance of Australia, Chile and China. Recycling lithium is not cost effective at current prices, she said.
The US has an advantage in synthetic graphite supply if the oil and gas industry invests in upscaling pet coke, she added.
Unable to meet needs
In the session on battery testing and aging, delegates heard arguments that conventional lithium-ion batteries are unable to meet the needs of many applications, including automotive and stationary storage.
Daniel Braithwaite, senior director of cell engineering at QuantumScape, said: “Many believe that the unique cell design of solid-state lithium-metal batteries will help bridge this gap – particularly when it comes to electric vehicles – because the technology is designed to enable longer range, faster charging and enhanced safety compared to conventional lithium-ion batteries designed to enable longer range, faster charging and enhanced safety compared to conventional lithium-ion batteries.”
Fast charging was discussed and its impact on cells. Dr Eric Dufek, research scientist and group lead for energy storage and advanced vehicles at Idaho National Laboratory, said fast charging can lead to early cell failure and poorer performance. The ability to use cell parameters for the development of advanced charge protocols provides an opportunity to tailor both the time and energy accepted to specific needs while minimising degradation.
Advanced protocols and analysis, including the use of machine learning, can help identify failure modes and predict performance, he said.
Feel the heat
On temperature, fire suppression and thermal runaway, delegates heard Seung-Wan Song, professor of chemical engineering and applied chemistry, Chungnam National University, say that safety is a weakness of state-of-the-art lithium-ion batteries, EVs and ESS.
“Replacement of highly flammable lithium-ion battery electrolyte with a non-flammable liquid electrolyte is a critical step to reduce or prevent the risk of thermal runaway.” She said interface stabilisation technology on graphite-based anodes is “a must” for dendrite-free lithium-ion batteries.