As the only international conference dedicated to the world of secondary lead, the 7th International Secondary Lead Conference’s aim was once again to share and increase knowledge over all segments of the lead recycling industry. BEST listened intently as the virtual show unfolded on our computer screens.
Now in its seventh year, the two-day International Secondary Lead Conference (ISLC) has traditionally been the appetiser to the main event, the Asian Battery Conference. Scheduled to take place in Borneo, the event organisers were forced to take the show online for the first time in its history due to “COVID-19 rules”.
In a pandemic-affected world the industry is beginning to accept online conferences— or at least get used to them. Online events have, in BEST’s opinion, been hit-and-miss affairs as organisers attempt to make them as similar to live events as possible. Sometimes those efforts have fallen short of the mark— not so here.
From a platform basis, ISLC worked fantastically. The program was easy to follow and the speakers’ slides were clear to read and the opportunity for attendees to submit questions to the speakers was well organised. As has become the norm, the presentations were available post-show— a great concept for us weary journalists.
Although it’s always an advantage to network in person, the conference’s stellar delegate and speaker list included: researchers, technicians, end-users and marketers whose work involves all aspects of secondary lead smelting from plant design, smelting regimes, refractories, and burner design, to slag formation and environmental concerns.
The talks swayed between industry insights from the well-known, well-respected faces to insights into new technologies by those forging their reputation within the secondary lead family.
Starting a conversation
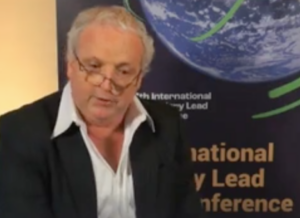
Sticking with tradition, the conference opened with Mark Stevenson, director of Global Lead Technologies and chairman of the Asian Battery and Secondary Lead conferences.
Stevenson was in a thoughtful mood, reflecting on the Bali event two years ago, he spoke of the changes wrought on the world during the global pandemic that meant the event was online only.
“We have to bring it in a different form. We would prefer to be live, but unfortunately, that’s not to be the case,” said Stevenson. “There’s been a lot of change to many of our friends and colleagues who have been severely impacted by the virus. We send our best wishes and regards.
“It is a testing time for the industry and for everybody, and that includes the way we do conferences.”
Impact on the industry
If you were to roughly split the conference into two main topics, it would be industry insights and technological developments.
Among the traditions of the event is for Huw Roberts, director CHR Metals, to start the speaker presentations. Opening the event for the seventh time, Roberts’ talk ‘Regional patterns in secondary lead production pre- and post-Covid’ covered the primary and secondary production markets.
He emphasised how the secondary lead industry was “by far” the bigger part of the global lead production industry, accounting for most of the production increase since 2005. Today, the secondary lead market’s share of the overall lead market is around 75%, according to CHR Metals— although official figures suggest it is more 65%— a rise from 61% during the past 16 years.
Production has tracked the expansion in China’s recycling capacity, with Roberts reporting that the industry now mirrored, to some extent, what it witnessed with primary lead in the 2000s.
“Back then there were new regulations, which outlawed various technologies; initially sinter pots, and then blast furnaces, and I suppose the idea at the time was that they would help consolidate the industry and limit the capacity increase. But what we saw— as many small primary smelters moved through the stages of upgrading cinder pots to blast furnaces to SKS [smelting processes] and then SKS versions two to three and four— was that very few people actually left the industry voluntarily,” said Roberts.
“So, the policy of improving the technology actually ended up resulting in a huge expansion in primary smelting capacity in China and we have a legacy of that still today with the large overcapacity.
“And exactly the same thing is now happening in the secondary lead sector; small-scale, secondary producers/recyclers who were forced to close their operations have decided, in many cases, to upgrade and expand.
“And we’re seeing expansions, all over the country, very large expansions, even in towns and cities where, when you look at the geographic location, and look at the scale of what they’re doing, you can’t imagine that there’s going to be enough batteries generated in those areas to actually see such a huge increase in capacity.”
Roberts said that looking at his firm’s data, he thought there was already capacity to recycle more than 13 million tonnes of scrap lead batteries a year; and there was potential for lead output of six-and-a-half to seven million tonnes.
Pandemic decline minimal
Despite the pandemic, which saw a fall in lead output, the decline was not as pronounced as some forecasters had predicted. In terms of the percentage, Roberts stated the largest fall directly pandemic related in 2020 was in Asia, outside of China.
Unsurprisingly, China still dominates the industry despite a steady output in Europe, North America and other countries during 2018 and 2019, before the inevitable modest falls in 2020; but there wasn’t a fall in output during 2020 in China, reported Roberts.
However, delegates were told the rate of growth typically seen in the last 15 years was going to slow and that decline would reflect a higher proportion of electric vehicle adoption, and to a lesser degree, developments in the E-bike and trike markets.
The forecast was to some extent echoed the following day of the conference by Farid Ahmed, principal analyst lead markets at Wood Mackenzie, during his talk ‘Lead markets – is there life in the old dog yet?’
The year-on-year fall in demand from 2019-2020 was 3.6% but the rebound this year will be 4.5% and he forecast that consumption next year would be another 2.8% higher than this year. After that growth rates will slacken off, partly due to pent-up demand loitering in the system, which will happen again next year, he said.
Even if the rate of automotive battery replacement demand normalises, or even dips below normal, the average growth rate for the three years after 2022 will drop to 1.6%, which Ahmed said was still not a bad rate of growth.
Following the easing of lockdown measures across the globe, demand for replacement automotive batteries had increased, with China leading the way, but Ahmed said it was the “white hot” demand in the US that really drove the market, which has not let up. He added that Europe had bounced back, as had the rest of Asia besides China, but it was the US that had led the way. A caveat to that was his firm predicted North America would see small declines in annual consumption this year and the following two years.
The industry chit-chat is the decline will be caused by too many cars running new batteries, which would mean failure rates would be low. This would translate to demand for auto replacement batteries, which is more than 60% of US consumption, “falling off a cliff” by summer 2022.
Not so, said Ahmed. “Supply chains there have been severely stretched due to the unrelenting demand for batteries,” he reasoned.
“Lead deliveries barely touch the ground before they are whisked off to the factory to be transformed into a battery, the only parts of the North American supply chain that are full right now are the scrap-battery yards, the rest is paper thin.
“It’s going to take a lot of lead to rebuild inventories of battery-makers, wholesalers, distributors and retailers, plus the stocks of refined lead at smelters and battery plants. But that will maintain lead demand well beyond the fall-off in battery failures, although certainly at a reduced urgency compared to the last year or so.
“Long term though, North America continues on its trajectory of minimal expansion and lead demand, the US and Canadian markets are somewhat saturated as rates of car ownership are high.”
Europe, which took a big hit last year, will see a strong rebound this year, but afterwards, it would remain flat for much the same reasons as North America. The region also suffers from increased imports of cheaper replacement batteries and from established brands “white-labelling batteries” made by a third party, said Ahmed.
India the power consumer
Ahmed’s charts showed that outside China’s dominance as a lead consumer, India was growing strongly, with other regions either remaining static or showing little growth.
Ahmed forecast that India’s growth would continue until it overtook the US as the second-biggest lead consumer before the end of the decade.
This growth is led by the country’s “colossal” potential for more car ownership, which would feed the auto battery demand, as well as increasing demand caused by greater industrialisation and urbanisation, which would, in turn, increase demand for standby storage and motive power batteries.
“The rest of Asia is growing quite well but is shadowed by the hugeness of China and India,” said Ahmed.
India’s rise will mirror the two-pronged rise of E-bike adoption and the country’s move to decarbonise its power supply with renewables.
At 2019’s 6ISLC in Bali, Roberts declared one of the key factors that would impact lead demand and availability of battery scrap in the near term was the development of E-bike and E-trade markets; although this was in reference to China, which now has three classes of E-bike: mopeds, motorbikes and commercial three-wheelers. The story is echoed across Asia as a whole.
“I do think that the lead battery makers should be exploring the potential for E-bikes and E-trikes in other parts of Asia,” said Roberts. “Before the cavalcade of lithium batteries begins to dominate the market we are seeing advertisements for lithium-powered E-trikes, particularly in India, and these are very slick campaigns.”
India’s primary lead production was 214,000 tonnes, between 1 April 2020 and 31 March 2021, a rise from 144,653 tonnes for the equivalent time in 2015-16. The figures from Indian mining firm Hindustan Zinc were quoted by L. Pugazhenthy, executive director of India Lead Zinc Development Association, during his presentation.
“Primary lead production has always gone up continuously, except for a dip in 2019-20.
“The numbers are continuously increasing and during the COVID year 2020-21, the production has been very high with 214,000 tonnes.
According to Pugazhenthy (known affectionately as Pug), total lead consumption in India was 1.5 million tonnes pre-COVID. Use of lead has gone up in the country, but it isn’t just the consumption of lead in which India’s star is rising despite its “secondary sector somehow suffering severely”, said Pug.
According to Pug’s slides, there are 672 authorised or registered secondary lead “units” in India recovering lead from used batteries, with 291 in north India. The authorised recycling capacity of these units was 3.5 million tonnes, pre-COVID. Of that total, secondary production was estimated to be 1.1 million tonnes.
“That is because a lot of things are happening. Diversion of the collected batteries by the dealers, the retailers to the traders and they are moving to the informal sector,” said Pug.
“That has been continuing in this country for quite some time, but certainly that has come down. The industry is aware that there’s a need to get registered and authorised so they have access to battery scrap from public auctions and they can also import from other countries.”
Most of the recycled lead is from India’s domestic sources but since 2016, when there was a change in the regulations, India has become an important importer, said Roberts.
This could be to blame for the poor performance of the country’s secondary lead markets during COVID. The majority of battery scrap in India is coming from sub-Saharan Africa and the Middle East, which between the two regions account for more than half of the 100kt gross of imports.
While the pandemic impacted all of the industry’s import trade, the sector has seen a strong recovery, especially from the Middle East and Africa. Year-to-date volumes are significantly higher than the same month of 2019, not just 2020-2019, delegates heard.
“It does look to me like the pandemic has caused the build-up of some unprocessed battery scrap,” said Roberts.
“And I think that anecdotal evidence is probably right because we are hearing from the recycling sector in a couple of regions that there are now good supplies of battery scrap. If only they could get the containers and the lorries to get them back to the smelters.
“So, production is recovering in 2021. And I think that as we begin to work through the accumulation of battery scrap, which is shown there by the recycling rate falling below 95% in 2020. I think in 2022 we could see a reasonably sizeable pickup in recycling.”
Established pyrolysis methods
The other side of the conference’s agenda focused on technology. This year delegates were treated to news of a mix of advancements in conventional pyrolytic technologies from established commercial companies, and new, largely solvent and electrochemical methods, from companies in the development or pilot scale stage.
In the second part of this report, BEST takes a representative cross-section of the companies and splits them into two groups: the established and the emerging technologies.
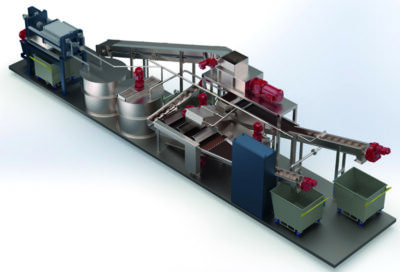
If you want conventional recycling equipment, then Wirtz Manufacturing is first on the list.
It was this time two years ago that Wirtz launched its Ready to Run system during 6ISLC. The system is housed in a 40ft-shipping container and is able to process 1-24 metric tonnes per day. The system can separate the battery into the metallic lead, lead oxide, separators and polypropylene. The skid-mounted system can be up and running within 24 hours of delivery.
The US company offers everything from battery collection bins through to breaking, smelting, refining, component and process-semis segregation and collection. It also provides the effluent treatment plant, fume extraction and filtration.
Being Wirtz, it also offers high quality and innovation such as its CS system providing continuous screen separation. Typical is the 15 MT/h fully automated CS breaker with four product streams. Unsurprisingly, they are able to offer full turnkey solutions.
Engitech gave a presentation based on its Integrate CX and FAST processing methods. This was a summary of their conventional used lead-acid battery (ULAB) recycling breaker-desulphurising-foundry-refinery technology. There were some innovations designed to improve efficiency and lower processing cost.
The Italian firm designs and manufactures breakers from two tonnes/hour (t/h) up to 60 t/h to suit the size of the operation and scrap availability. Engitech customises plant design with the possibility of dual desulphurising. This means a choice of soda ash/caustic soda treatment or standard route and ammonia options. It also claims this can achieve sulphur contents of less than 0.5%. The foundry technology includes large tilting rotary furnaces of more than 130 t/day with refining and air pollution abatement equipment also on offer.
New innovations include reagent metal dissolution, then electrochemical deposition of lead from solution. According to Engitech, a demo stage at Doe Run has been successfully operated. Their new FAST process using electrolysis in ammonium chloride removes the desulphurisation process. They are currently engaged in R&D for salt splitting to convert Na2SO4 to NaOH and H2SO4, both of which are saleable commodities.
Emerging technologies
ULEAD presented two innovations. The first was turning to urea to desulphurise paste, giving fertiliser— ammonium sulphate— as a by-product. The second innovation is the LEAD3 process for the chemical dissolution of the desulphated paste using acetic acid. The precipitate from this then goes to a secondary calcination treatment for the production of nano lead oxide (Slide 1).
The process of using deep-eutectic solvents first caused a stir in Bali in 2019 when 6ISLC delegates heard the process gave the major advantage of removing the desulphurisation process. The process has moved on since then and the limited company Solveteq was formed in 2020 as a spinout from the Imperial College London in the UK.
The process enables the dissolution of lead paste and then the precipitation of a lead salt, with high purity, to be recovered. There is a choice of which lead species is precipitated. This gives flexibility in deciding on subsequent lead forms for compatibility with subsequent calcining and LAB processing routes. Slide 2b shows similar conversion rates for both sulphated and desulphated pastes.
Solveteq’s technology is based on the use of deep eutectic solvents, which were developed as a green alternative to ionic liquids. The process can work from room temperature to a maximum of 70°C and is designed to be modular and scalable. The proprietary solvents were developed at Imperial College London to process de-sulphurised and sulphurised paste directly from the battery-making process and, depending on the requirements, can produce a metallic lead or lead oxide.
“So the goal of our efforts is to have a system that can easily fit into the existing operations, either as an add-on capacity for battery recycling companies, as a retrofit, or alternatively, as a small- or medium-scale recycling standalone plant that can be suitable for SMEs,” said Hekselman.
The company is expecting 70% lower energy consumption than the incumbent technology. Its estimates are indicating a 50% reduction in CO2 emissions using the process. It’s important to point out that the process is not waste-free. It does produce minimal waste, during the filtration stages, with resulting waste having to “most likely” go to a smelting furnace process.
Ever Resource claims its pilot-stage recycling plant can break and separate up to 24t/h with a 99% separation of paste from metallics. They also maintain that their desulphurisation process with a novel reagent is 99% effective and has a lower carbon footprint. This is followed by wet chemistry dissolution of the resultant paste to produce a lead organic salt; then chelation to form a lead citrate, followed by calcination.
The end product is nano-structured Pb.PbO. They have also, since their first public announcements on their process, asserted that the patented calcination process can be fine-tuned to give variable lead content and control the alpha/beta oxide ratio (Slide 3).
Singapore’s ACE green recycling process claims to be non-polluting, zero greenhouse gas-emitting, and low-cost method of producing high-purity lead ingots directly from ULABs at room temperature. It replaces the smelting operation with the chemical dissolution of the entire lead content of the battery, followed by electrolytic deposition of pure lead to produce compressed ingots. These are then sent to the refinery for further treatment as with pyrolytic methods.
The chemistry relies on basic electrolyte media, mostly NaOH, which also removes sulphur. This results in the creation of Na2SO4, which is sold as fertiliser. There are some unspecified wastes that ACE claims are much less than those of smelting. They also say that they can treat smelter slag, which reduces waste by up to 65% compared to pyrolysis.
GME Recycling claims to improve the cost-effectiveness of ULAB recycling by improving the efficiency of the breaking and separation procedures that are currently in use. There are several key points in its process: auto feeding, which contains a vibrator with a magnetic separator and a metal detector to prevent mill damage; a novel hammer mill that precisely crushes and separates grids and paste etc; an inertial separator to isolate grids from poles.
The Italian firm’s contention is that by improving the separation stage, they reduce waste and equipment wear in the smelting phase, to give lower lead bullion production costs.
The new normal
As a virtual media conference, the presentations and questions were handled perfectly, with the content very topical, showing a thoughtful balance between new, emerging technologies and traditional pyrolytic methods.
A “take-home” highlight for BEST was the assertion by some companies that they have viable methods for the treatment of slag waste. If this is correct then it will remove a very large fly in the lead battery recycling ointment.