Carbon additives give lead-acid batteries a bit more oomph. But with so many options out there, what is the best for your lead-acid battery design? Ruth Williams talks to the producers to find out.
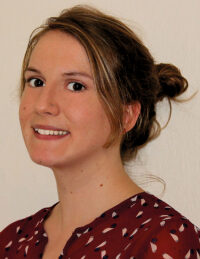
In the face of newer chemistry options, pro-lead lobbyists make the arguments that lead is familiar, reliable and cheap versus lithium-ion and the advanced battery posse. As cars change to reduce fuel usage and accommodate carbon emission rules, the lead-acid chemistry needs to adapt quickly to keep its stronghold in automotive batteries.
Lead-acid batteries can have a facelift by way of carbon additives to give it a second wind as lithium-ion encroaches on its ground. Chemical additives have been used in batteries since the 1950s with varying degrees of success to combat sulphation. The traditionally used expanders have been a blend of barium sulphate, lignosulfonate, and carbon.
Out of the classic blend, carbon has been the ‘redheaded step-child’— overlooked in studies that focussed on lignosulphonate. But now carbon is receiving plenty of attention having come to the forefront of thought as partial state of charge applications became more prominent.
Most people are aware of the partial state of charge model for lead-acid operation to accept a charge at any time in any state and use that energy on demand, such as in stop-start applications. In Europe the majority of new cars are built with stop-start engines. Indeed, Ford says it will aggressively push the technology in its models saying that 70% of its cars will have at least this level of hybridisation by 2017.
Energy conservation and the need to reduce carbon emissions feeds the second market for partial state of charge applications: Stationary batteries for use with renewable energy supplies. The stationary battery, just as the automotive battery for stop-start, needs to accept charge when energy is generated from sun or wind and deliver that energy on demand regardless of the state of charge.
The biggest problem batteries face regarding partial state of charge is sulphation. This is defined as kinetic irreversibility in formation/dissolution of lead sulphate (PbSO4) and consequently accumulation of PbSO4 in battery electrodes that leads to reduced battery cycle life. This means batteries fail because the negative active material became covered in a dense layer that builds up and acts as an insulator stopping the battery from accepting or releasing charge.
As part of a fundamental research programme undertaken in 2010 by the Advanced Lead-Acid Battery Consortium (ALABC), along with its members from the industry, the loading levels of expanders were measured to see the effect on the negative active material. In a traditional expander mix around 0.1–0.2% of carbon was added to the active material, which did nothing to prevent sulphation.
However, adding 1 – 3% of carbon to the active material created a conductive carbon network within the sulphate layer that an electrical charge could travel through to re-establish a route for the electrical current to get through. The research showed carbon additives resulted in significant improvements in cycleability, charge acceptance and reducing sulphation to the negative plate.
This has not entirely translated well into practice because incorporating the carbon additives effectively into the negative plate has proved challenging. The higher loading of carbon additives can cause difficulties in the paste formulation and pasting because it requires more water. This can lead to low paste density and poor mechanical integrity of the electrodes. So working with the right amount of additive is essential.
As an upshot of the studies, companies have begun using conductive carbons as additives that can easily be incorporated into the paste formulation and do not affect the integrity of the electrodes. Continued studies by ALABC have shown that activated carbon performs much better than graphite.
Activated carbon has larger particles than graphite and forms a wire-like structure in the active material, acting like an addition to the grid structure to increase conductivity in the paste. It also does not impact the active material or impact voltage shifts in the way graphite does, which leads to unwanted water losses.
Following the ALABC study, additives and expander companies began to work on blending different ratios of carbon to best suit different lead-acid battery applications. High structured carbons with high conductivity have been found to be very beneficial; these can be blended with graphites with a high proportion of carbon blacks together with other materials to create mixes for partial state of charge applications.
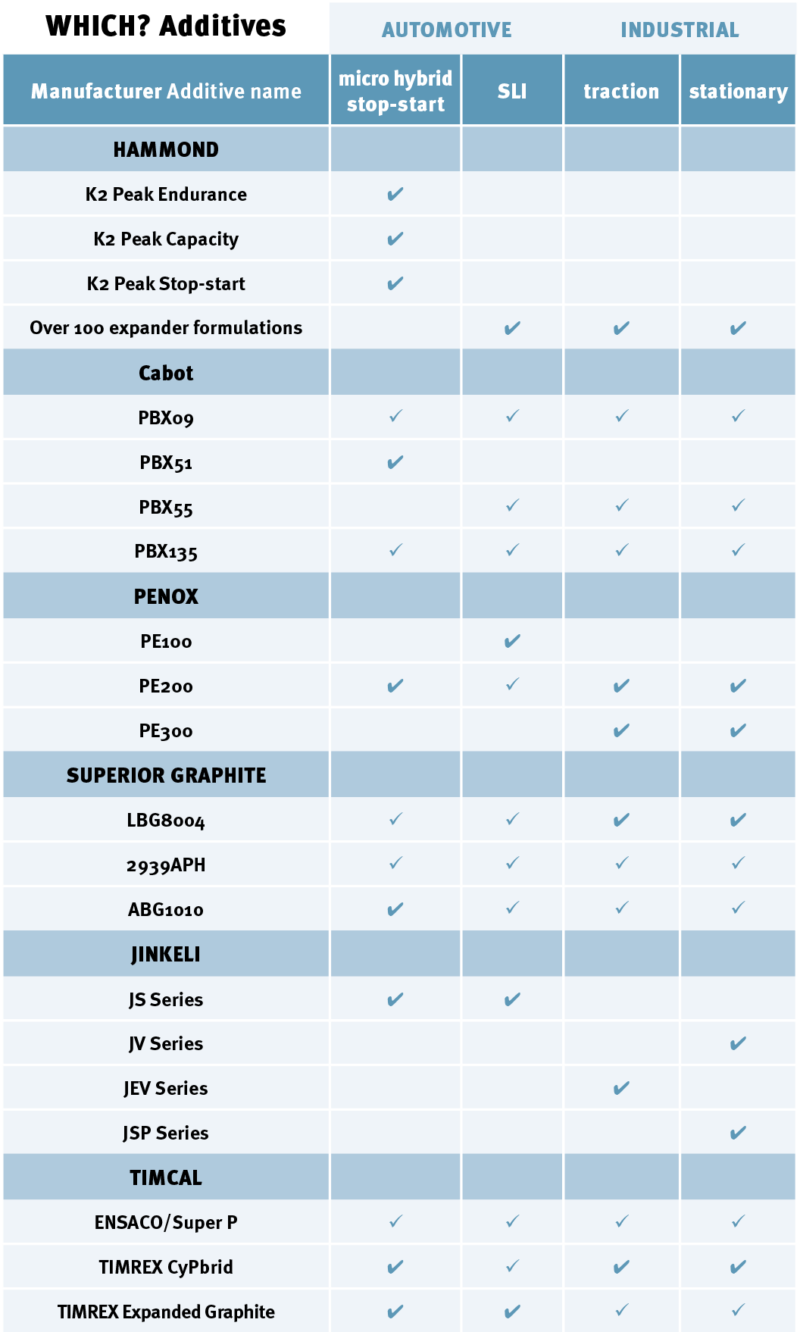
So what is available to better your battery?
Hammond Expanders, part of the Hammond Group, was heavily involved in the ALABC study programme and says it has opened up an avenue to focus their own research.
Hammond carries out its own research and development: “We decided two years ago to invest in in-house capability,” says Achim Lulsdorf, VP of product development at Hammond Expanders. “We also participate in industry studies but we wanted to carry out independent research also. We have invested in people and lab capabilities, we are expanding laboratory and testing capabilities.”
“We found early on the key to a good expander is the interaction of the lignosulphonates and the carbons. I really believe that most of what I have seen has been focused on isolating the effects of the components, I believe Hammond is among the first to methodically study the interactions. We believe the interactions are the key.”
The result of this methodical working is the K2 line and consists of three expander blends for micro hybrid stop-start vehicle batteries: Endurance, Capacity and Stop‑Start.
The blends give a range of performance enhancements depending on specific needs, but improving one aspect of performance can be detrimental to others. Lulsdorf says they recommend blends based on the exact technical specifications a manufacturer has to fulfil.
The K2 Endurance is engineered to give the maximum cycling performance for partial state of charge applications, it contains high levels of advanced carbons and graphites.
The K2 Capacity is designed for manufacturers that need a balance between the partial-state of charge performance, but still need high levels of capacity performance and cold cranking ability. The third product is the K2 Stop-Start. It mainly focuses on providing good capacity and cold crank performance, while still assuring reasonable PSoC behaviour.
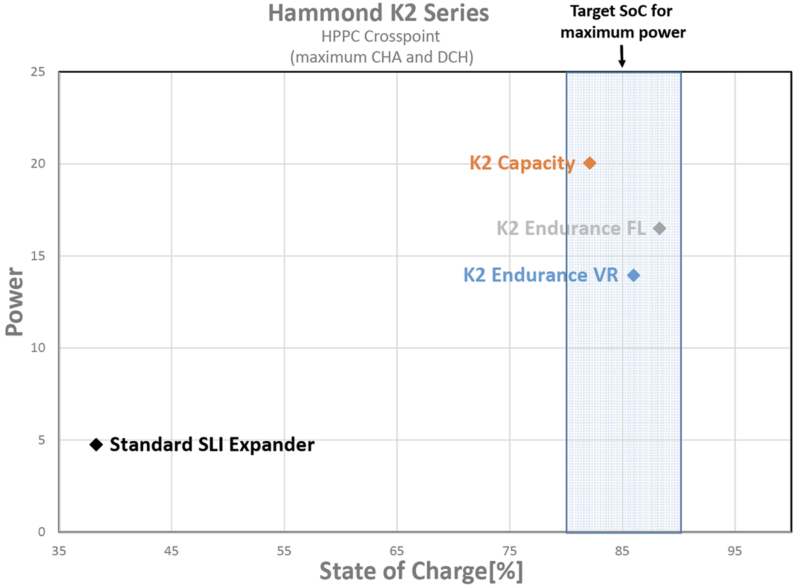
Hybrid pulse power characterisation test results comparing a standard SLI expander formulation with the K2 Peak Capacity and Endurance products. The shaded area shows the state of charge level a battery should perform in for micro-hybrid applications. The diamonds represent points at which the test cells’ charge and discharge power levels are equal.
A suitable expander for the micro-hybrid application will enable the battery to perform at high levels of SoC (>80%) with high charge and discharge power. The K2 expanders fit this requirement.
Cabot Corporation, whose battery additive department is based in New Mexico, has designed a range of carbon additives for lead-acid batteries called PBX. They have varied properties to suit the needs of different applications. They are suitable for use in VRLA and flooded advanced batteries, as well as in applications that need higher levels of charge acceptance.
The first, called PBX09, aims to balance high charge acceptance with improved cycle life. It is suited to most types of VRLA and flooded batteries for applications including stop-start, telecoms, motive power and e-bikes.
The second called PBX51 is aimed at the micro-hybrid and market where dynamic charge acceptance is the primary feature of the battery. Cabot recommends loading 0.25 – 1% to the negative plate slurry. Higher loading requires additional engineering to redress water loss and cold crank performance.
Cabot claims nearly double the dynamic charge acceptance and improves cycle life ten times, when used at 1%. Miki Oljaca, R&D manager of energy materials for Cabot Corporation, explains this marked enhancement: “The reason for this improvement is the introduction of additional conductive surface area to the negative electrode which enables high charge currents without polarisation of the negative electrode, therefore increasing cycle life.”
PBX55 is said to improve cycle life for flooded batteries that require minimal charge acceptance such as stop-start capabilities without regenerative braking in smaller vehicles. The fourth blend is PBX135, which is a multipurpose additive that gives a balance between improved cycle life and dynamic charge acceptance.
This is designed for use in flooded batteries in stop-start and motive power applications. Cabot designed its PBX carbon additives to be able to easily incorporated into the negative paste formulation, requiring less water to be added, as well as providing higher paste density and good integrity of the negative electrodes.
The long-established multinational player Penox, whose additive division is based Germany, has focussed on keeping high porosity of the active materials, especially on the negative plate.
Ian Klein, R&D manager at Penox, says focusing on porosity helps to overcome sulphation: “We think that with bigger pores you have a better possibility to transport out of the pores when you charge a battery with a high current.”
Working to this idea, Penox has developed three types of expander blends containing carbon additives. The first is PE100, which is used for standard SLI batteries. It is made of a blend of the three classic expander components with a higher proportion of carbon black.
The second blend is called PE200. It is a dedicated blend for emergency starter batteries (ESB) and AGM battery applications, as well as light traction batteries. The PE200 contains a different type of barium sulphate to support the evolution of bigger pores. It also contains a high proportion of carbon black, some of which can be substituted for graphite or activated carbon.
The third type is PE300, which is for industrial batteries only. This contains a smaller amount of carbon black and highest ratio of barium sulphate. PE300 is suitable for applications that do not have specific charge acceptance issues but still benefit from carbon in the expander mix.
“At Penox we are delivering expander mixes with a different view to the function of the single materials,” says Klein. “We think it is very important to keep high porosity, so we increase the internal conductivity of the paste but it is better to increase the porosity of the active materials, especially on the negative plate.”
The additive is added to the negative active material to act like a seed at the point sulphation begins, i.e. during discharge. The larger the seeds, the larger the pores to allow acid flow and prevent sulphation.
Following testing Penox has seen its expander mix can increase charge acceptance by more than 20% for high current applications. The company has a new range in development that will be unveiled at the European Lead-acid Battery Conference in Edinburgh this September.
TIMCAL Graphite & Carbon, a Swiss manufacturer of carbon and graphite additives, has a range of carbon blacks and graphite additives on the market: ENSACO Conductive Carbon Black and Super P Conductive Carbon Black; TIMREX expanded graphite, and the recently launched TIMREX CyPbrid material family. This carbon hybrid material was specifically developed and combines the key properties of carbon black and graphite while addressing processing requirements and avoiding blends of carbon materials.
Thomas Hucke, head of R&D for electrochemical applications at TIMCAL says: “TIMREX CyPbrid exhibits an easy handling and processing in the electrode pasting process and has a good affinity to lead for efficient lead plating and incorporation of the carbon into the negative electrode structure. The key attribute of this material family is the carbon morphology which in terms of battery performance allows a scalable charge acceptance while at the same time stable cycling at high rate micro-cycle operations at partial state of charge of the lead‑acid battery.”
TIMCAL develops its additives in-house; Hucke says the company is looking to further improve its carbons to meet the future requirements of the lead-acid battery industry. A key area of interest is increasing the charge acceptance while controlling water consumption, and the durability of the advanced lead-acid battery.
Superior Graphite, based in Chicago, also has three purified graphite additives in its Formula BT range for the micro and mild hybrid, motive power and stationary application markets.
FormulaBT LBG8004 is a high performance, high purity graphite additive designed primarily for VRLA and flooded batteries designed to excellent cycle life and high charge acceptance under high rate partial state of charge conditions. This blend is suited to stationary applications such as telecoms and grid-level batteries.
Superior Graphite says adding it to the negative active material will reduce sulphation and improve cycle life under high rate partial state of charge for dynamic charge acceptance applications and does not result in excessive water loss.
The second formula, 2939APH, is designed for the same markets and is a lower cost, multi-purpose additive that does not improve cycleability as much as the LBG8004. Joseph Li, product manager of Energy Materials at Superior Graphite says: “The 2939APH is a low-cost approach, and is suitable for automotive applications by combining with conductive carbons.”
The third is BT ABG1010, expanded graphite for VRLA and flooded batteries to boost cycle life and high charge acceptance under high rate partial state of charge conditions. This blend is most suitable for automotive applications.
Jinkeli Corporation, headquartered in Shandong Zibo, China, has designed a range of additives for the lead-acid battery industry. In response to an increase in lead-acid battery powered e-bikes and EVs in China, Jinkeli’s engineers have developed additives to boost battery capacity, offer longer cycle life and better charge acceptance.
Jinkeli’s composited additives contain high conductivity carbon, surface active lignin and humic acid. The four types of additive blends are JS Series, which is used for micro-hybrid and SLI batteries, JV Series is used for standby batteries; JEV Series is used for motive power batteries; and JSP Series which is used for storage batteries.
Jinkeli Research Centre of Battery Engineering Technology carries out its own research and development on battery additives. “We have increased the investment in people and laboratory equipments. It will enhance the testing capability of the centre obviously, and will speed the exploitation of new additive products,” says Xin Yancao, managing director of the company.
As with any new developments, manufacturers can be cautious about using additives in certain applications. Companies delivering batteries to automotive OEMs are especially wary. Klein, of Penox, explains that using new materials can mean a lengthy approval process for manufacturers of up to two years so manufacturers are stuck with the materials they are using now for the time being.
For this reason the aftersales market has been the first area to adopt additive enhanced batteries. “It was much easier to work together with companies that mainly produce for the aftermarket because there is not the same approval process that were asked by the automotive manufacturers.”
Several battery producers have begun the process of having additives approved for use in automotive batteries and Penox, for one, is hoping the benefits demonstrated will shorten the approval process.
With any of the products available there is an element of compromise –improve charge acceptance but engineer the battery to overcome the deterioration in cold cranking performance. Until the ideal blend has been found, these are the options that can be beneficial to the battery maker’s needs.
And what can be expected in the future? As a relatively new area of research, there will be scope for improvement. Hammond’s Achim Lulsdorf says: “The requirements are constantly changing and commonly accepted specifications have yet to be determined. Our main research focus is now to develop a deep understanding of the expander component’s interaction. We will certainly stay busy in this field for years to come.”