Dr Mike McDonagh talks with CTO and co-founder of battery recycler Ace Green Recycling, Vipin Tyagi. It is, he found, a company with a different approach to the conventional recyclers. It also has a track record, with prototype recovery yields that show promise.
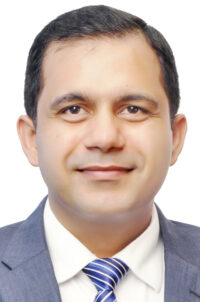
There are many emerging companies which have joined the juggernaut bandwagon of lithium-ion technology. From battery component designs to new solid or gel electrolytes, it is difficult for technical journalists to keep abreast of the latest offerings. It is followed closely by the other problems of resource availability, materials handling, safety and recycling. We have seen companies with shareholder funding drop away due to lack of progress or incorrect priorities.
BEST: The process describes ‘electrical discharging solutions’ to render the batteries safe for handling. How is this different from standard discharging methods?
Tyagi: Ace utilises electrical discharging solutions for both small format batteries and the larger EV batteries. An essential part of battery maintenance and the most reliable indicator of its state-of-health (SoH) is the capacity test, where controlled cycles of battery charging and discharging are performed to determine the amount of available energy.
Ace uses a dedicated cell diagnostic unit consisting of cyclers to find out the SoH of batteries. If it is more than 80%, then the battery qualifies for second life (repurposing and reuse) applications. If less than 80%, then the battery is discharged to a defined lower potential and sent for recycling. The energy released during discharging is harvested and used to provide lighting in the Ace warehouse.
EV battery packs with an in-built battery management system (BMS) are discharged to a certain defined potential before the BMS is removed, to the threshold potential. This is done through a deep discharger. Cells are discharged to 0.5V and deemed safe for subsequent shredding, crushing and material extraction. Rapid discharge can produce stress in the battery, from which there can be some ‘rebound’ charge recovery. Minutes or hours later, the voltage on the battery can recover, even over the critical 2.5V (Fig 1a).
Hence, the Ace process discharges the battery to 0.5V and dismantles it into individual modules before checking the SoH in a dedicated cell diagnostic unit, as shown in (Fig 1b).
The second part of the process uses battery breaking. Can you provide more detail?
Tyagi: Lithium-ion batteries are composed of cathodes, anodes, separators, and electrolyte. The battery breaking process at Ace is environmentally friendly and is a series of steps involving shredding of discharged end-of-life lithium-ion batteries, separation of polypropylene (PP), steel, aluminium, copper, and final recovery of black mass from these batteries. Post-shredding, the exhaust gases are wet scrubbed, then treated with activated carbon in the absorber and disinfected with the UV radiation before release.
The process flow in Fig 2 gives more details.
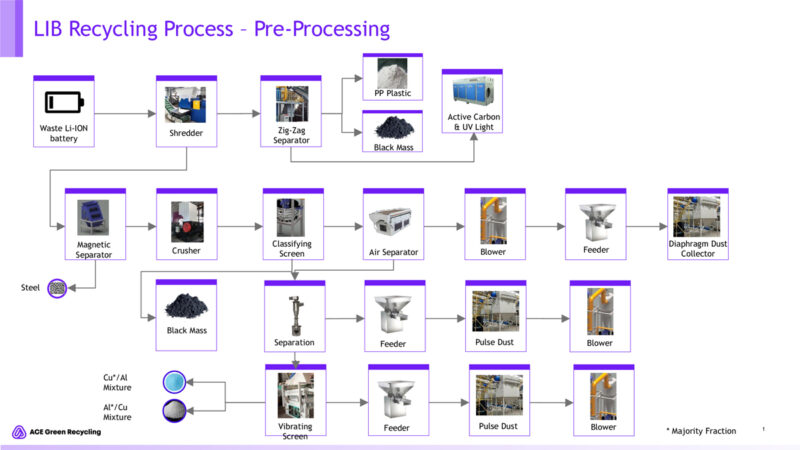
What happens to the BMS?
Tyagi: It is removed from the battery pack and sold to electronics companies for recycling.
How are the fractions after breaking and before chemical treatment segregated? Do you use industry standard mineral dressing techniques?
Tyagi: Aluminium and copper fractions are gravimetrically separated based on their respective densities. Even after this segregation, they are not completely clean, as black mass remains adhered to these fractions. Therefore, chemical treatment is undertaken to remove black mass from these fractions and produce value-added products from the aluminium and copper.
How does your process differ from the presently available processes?
Tyagi: In several respects. The first is the chemistry which is a departure from the standard extraction methods commonly used for processing mineral ores. The second is that it is capable of processing Both LIFePO4 and NMC cathodes. This is important as no current processes are designed for LFP scrap. With the present trend towards increased use of LFP technology for EVs, due mainly to safety, availability of cathode material and cost, there will be increasing demand to recycle this battery chemistry. We can do that, albeit we need higher throughputs to make the process commercial compared to NMC processing due to the lower value of the recovered material.
Figs 3a and 3b show how the two battery chemistries can be processed with the same equipment.
In both cases lithium carbonate is produced as a first step. Once the metallics are separated out, they are cleaned to remove the residual 1.5–2% black mass which is added to the black mass for chemical treatment. These products can be further refined (upcycled) to remove impurities, making them suitable for use as battery grade materials. Alternatively, they could be sold to recyclers such as Umicore for further processing to add to the battery supply chain.
The LFP process is optimised to operate at room temperature, significantly reducing the cost. This is important due to the inherently low value of FePO4. There is also the option of selling this fraction to the fertiliser industry. We also recover the graphite from the anodes. This again is very important as the great majority of graphite, particularly naturally occurring material, is from China. The US in particular wishes to be self-sufficient in all anode and cathode materials for manufacture of LIBs.
You confirmed the use of soda ash in an aqueous medium. If brine is not involved in the process, how are the metal chlorides in the by-products created?
Tyagi: Correct, brine is not involved in the process. Metal chlorides are produced as by-products of our proprietary recycling process.
According to your flow sheet, you have two stages for end products. Why?
Tyagi: We see our technology as being commercially viable at two levels: easily produced, unrefined products from the black mass, and the upcyled, refined black mass products which can be sold as battery grade materials. This gives the option of two markets – the existing battery recycling companies and the battery manufacturing companies. Because our processing and capital costs are low, we are confident that our market prices for both products will be competitive.
You use the word upcycle. What do you mean?
Tyagi: We are working on upcycling the recycled graphite to battery grade. This means we are working on correcting the microstructural defects to add more value and make it battery grade.
What do you do with the non-aqueous solvent electrolytes from the batteries?
Tyagi: They are collected in gaseous form as the batteries are shredded and subsequently scrubbed.
Does this mean the cells/batteries are heated to convert the volatile electrolytes into a vapour?
Tyagi: The initial shredding process is under negative pressure. This means the electrolyte volatiles are more readily removed. There is some small residual heat remaining in the semi-processed mass at this stage.
Graphite microstructure defects are mentioned. What are they and how do you correct them?
Tyagi: Some of the microstructure defects in the graphite are formed during the usage/lifecycle of batteries, while others are formed during the recycling process. We are working with National Renewable Energy Laboratory (NREL), a US federally-funded R&D centre, for upcycling recycled graphite back to battery grade.
What does ‘fag end’ mean? In the UK it refers to the last bit of a cigarette discarded after smoking.
Tyagi: In this context, it means ‘at the end’. Our technology is focused on our LithiumFirst approach, where lithium is extracted first, before the other battery minerals. This avoids the possibility of cross-contamination of the lithium stream if it were to be extracted at the end of the process. This approach gives higher recoveries and purities.
Do you have a minimum commercial breakpoint level?
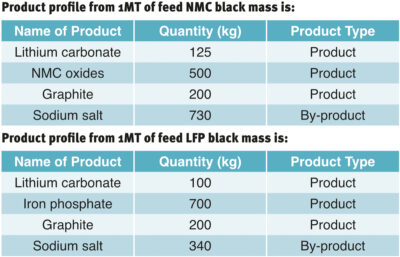
Tyagi: The commercial viability is volume and product dependent. We have already covered the value propositions relating to the black mass and the upcycled products’ potential values. The volume criteria is important as economies of scale will reduce processing costs. The values given for the breakpoints show that we expect to start achieving good economies of scale around 50,000 MT/annum of LIB scrap.
Have you retained your pilot scale and prototype facilities?
Tyagi: Yes, we have retained our pilot scale facility in India. We will continue to operate this while we expand our presence in other key geographies.
How much scrap do you process per annum?
Tyagi: Our pilot/demonstration facility in Delhi, India, can process 1,800 tonnes per annum of lithium-ion batteries. Currently, we manage 66 tonnes per annum of black mass. This is being scaled up to 300 tonnes per annum for LFP products. No other company is addressing LFP recycling. However, our expansion plans involve establishing recycling facilities with capacities to process 20,000 tonnes per annum in Texas, Korea and Mundra in India. These upcoming plants are at various stages of financing and permit approvals.
Which companies are taking material and how much is being sold?
Tyagi: We continue to develop customer relationships for offtake of our products. A brief outline of some of our reputed customers is shown in Table 2.
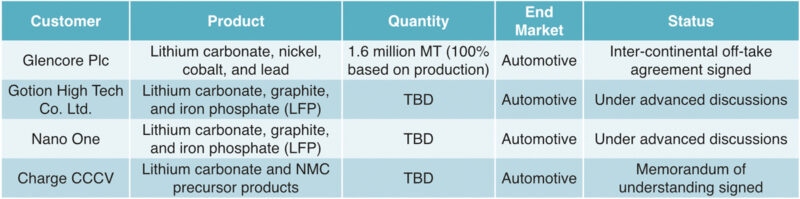
Do you arrange collection and transport of scrap? Who does it?
Tyagi: It’s done by a third party.
Technical editor’s comment
While there is still some ground to cover before the concept becomes commercial, it does seem that this approach of concentrating on recovery of the graphite and the LiPO batteries sets it apart from the mainstream companies. As we know, the current mainstream processes are mainly based on recovery of NMC cathode materials due to their high value. These processes are energy intensive and expensive. The aqueous-based recovery system, if it works as described, should provide, a cheaper, more environmentally friendly alternative to the current practices.
Add to that the total concept of recovering all the anode and cathode materials, with a further upgrade to battery-quality feedstock, then the technology should remain attractive for the future. However, as a reality check, it is understood that all processes need a minimum feedstock to make them commercially viable. As we report elsewhere, the current scrappage rate of lithium-ion batteries is insufficient to provide a living for all of the established and upcoming recycling companies.