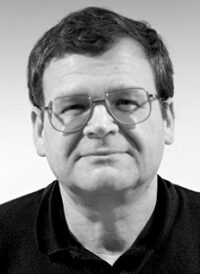
Lithium-ion battery expert Prof. Paul Christensen queries claims made by LG Chem about finding the key to suppressing thermal runaway. This distinguished academic’s questions about how a thin insulting layer between the cathode and aluminium current collector could prevent thermal runaway have not been addressed, as he explains. Additional reporting by Andrew Draper.
The paper by In-taek Song et al., (Thermal runaway prevention through scalable fabrication of safety reinforced layer in practical Li-ion batteries), published by the Nature Communications scientific journal in September, presents some potentially game-changing results with respect to increasing the safety of lithium-ion batteries.
In essence, the technology consists of a conducting polymer layer called a safety reinforced layer (SRL) between the cathode and aluminium current collector.
If the temperature rises to around 100˚C, the polymer becomes resistive, preventing current flow to the current collector, i.e. acts as a positive temperature coefficient (PTC) material. The paper also reports some very clever syntheses to tailor the desired properties of the SRL.
For me, the key data show the voltage and temperature profiles during nail penetration of a 3Ah cell without and with the SRL, six tests each. The cells with the SRL did not show any signs of thermal runaway or show any increase in temperature – despite nail penetration being arguably the most violent form of abuse.
Before I get too excited however, I would really like some clarification:
- Firstly and perhaps most importantly, I am puzzled as to how a thin insulting layer between the cathode and aluminium current collector could prevent thermal runaway, apart from during overcharging.
During overcharging, severing the connection to the power supply – for example by insulating the cathode material from the cathode current collector – will, in principle, stop thermal runaway. But this should be done in any case by the battery management system.
In contrast, during nail penetration there is no need for an external circuit for thermal runaway to occur – current flows directly between anode and cathode through the nail and the presence of the SRL layer is thus immaterial. We have carried out many nail penetration tests on our 1.7kWh modules, always with the modules at open circuit, always with thermal runaway. Hence an explanation of how the SRL prevents thermal runaway under these circumstances is essential. It may be that the insulating SRL coats the nail during penetration through the cathode: if so evidence of this should be provided. A mechanism and evidence are also required on how the SRL could prevent internal short circuit and thermal runaway following separator collapse due to e.g. thermal abuse.
The variation in the resistance of the SRL with temperature is clearly critical to its activity as a PTC, and the authors employed electrochemical impedance spectroscopy (EIS) to determine this. EIS is an analytical technique that relies heavily on the modelling of the electrode/electrolyte interface. My introduction to the world of lithium-ion batteries was way back in around 2010 when I was part of a team developing EIS methodology to assess the quality of lithium-ion cells on the production line.
Usually, EIS involves formulating an ‘equivalent circuit’ comprising electrical components (including resistors, capacitors and ‘leaky capacitors’) to represent the interface. The experimental data is plotted as a ‘Nyquist’ plot of minus the imaginary impedance versus real impedance (not imaginary vs real impedance as in supplementary Fig 6) and this is compared to the data obtained from the model. The values of the various components of the equivalent circuit are changed until the two plots match or fit. In this way parameters including the charge transfer resistance (RCT) and electrolyte resistance (RS) can be extracted from the experimental data. However, explaining and justifying the model, the latter by statistical means, is crucial.
Details missing
No details on the model the authors employed or the statistical analysis to prove the ‘fit of the experimental data to the model are presented in the paper. In addition, in order to extract the RCT and RS requires the ‘usual’ semicircular Nyquist plot.
However, only the Nyquist plots at 4.1V and possibly the plot obtained using SC40 at 3.5V in supplementary figure 6 would allow this, the remaining plots are mostly linear but some with some curvature. In addition, the plots all start at the origin, suggesting an electrolyte resistance of zero ohms and this seems unlikely.
It may be that the data have had the Rs values subtracted. If this is the case then the raw data should be available. Finally, in science, it is generally the case that a system is modified in an incremental way, i.e. changing one parameter at a time, but data for the ‘base’ system is always included for comparison: hence I should like to see the corresponding Nyquist etc. plots for the cells without SRLs, which are not included in the paper or the supplementary document.
I emailed the two principal authors with my questions on 4 October 2024, but I have received no response. I also emailed the journal, on which I am a reviewer and guest editor, again with no reply.
Editor’s note: Neither LG Chem nor Nature responded to approaches by BEST for comment, with several attempts to LG Chem. However, Lee Jong-gu, chief technology officer of LG Chem, said in a press release: “This is a tangible research achievement that can be applied to mass production in a short period. We will enhance safety technology to ensure customers can use electric vehicles with confidence and contribute to strengthening our competitiveness in the battery market.”
Lack of transparency
A report from the International Council of Academies of Engineering & Technological Sciences in October, Navigating the future: a report on the current state and future path of energy transition in the transport sector, pointed out the lack of transparency as a problem, both for fire fighters and the electric vehicle (EV) industry. The global adoption of EVs brings new fire safety challenges, the report stated. “The transportation of EVs, especially aged or second-life batteries, raises regulatory and logistical concerns,” it said.
“Future developments in battery chemistry can improve EV fire safety, yet transparency from battery producers and rigorous testing of these new chemistries are needed. Comprehensive fire safety strategies encompassing regulation, data sharing, research, and public awareness are essential for a successful transition to sustainable transportation.”
Call for more EV fire statistics
A lack of EV fire statistics – exacerbated by the novelty of EV technology and the reluctance of insurance companies to share relevant data – makes it difficult to assess risk at international level, the authors said. Legislation may be required to mandate the sharing of such information for safety research, they added.
The high costs and proprietary nature of large-scale EV fire tests means current understanding is primarily based on small-scale tests, which leaves some safety issues unresolved.
“Addressing these requires comprehensive large-scale testing, collaborations between OEMs and academic institutions, publicly funded research, standardised testing protocols, and cross-disciplinary research,” the report stated.
Understand and mitigate
An article on thermal runaway due to be published in Next Energy scientific journal in January, noted that extensive research has been conducted on the component materials of lithium-ion batteries, the causes triggering thermal runaway, and the mechanisms underlying it in laboratory settings.
“Yet, further research to fully understand and mitigate thermal runaway is necessary as it is a highly complex process that is readily influenced by both external conditions and internal reactions, said the authors Yixin Dai of the UK’s University College London and Assistant Research Professor Aidin Panahi of Worcester Polytechnic Institute in Massachusetts, the US.
They said the prevention of thermal runaway and the inhibition of heat propagation in the event of thermal runaway in lithium-ion batteries are paramount concerns for ensuring their safety and reliability. Preventive approaches are crucial, they said.
Electrode thickness can significantly impact heat generation rate during battery operation, which affects thermal safety, they went on. They called for a broader strategy including devices like the positive temperature coefficient device, current interrupt device, safety vent and thermally switchable current collector.
Passive strategies such as using phase change material and phase change composite material can mitigate the consequences of thermal runaway after it occurs, they said. Preventive strategies include a battery management system (dividable into internal and external thermal management). The BMS stands out as “one of the most reliable options to ensure battery safety and high performance,” they said.
The paper calls for the manufacture of more accurate sensors to better monitor the inner state of batteries, with modelling studies on predicting the temperature and pressure distribution inside batteries. The authors also called for further research on:
- separator shrinkage
- partial cells with thermal runaway processes
- the rate at which oxygen can lead to explosions.
Panahi told BEST LG Chem’s innovations represent “a significant step forward in enhancing battery safety.” In addition to its material that can withstand flames and delay thermal runaway, LG Chem has been working on aerogel-based thermal barriers. He said its aerogel, composed of over 95% air, is exceptionally lightweight and exhibits high heat resistance, making it suitable for thermal shielding in EV batteries.
He added, however: “While these developments are promising, I would need to review detailed technical data and independent validation studies to fully assess the efficacy of these materials in real-world applications. The ability to withstand extreme temperatures is crucial, but factors such as material integration, long-term stability, and performance under various operational conditions are also vital.”
SNE: battery manufacturers must do more
South Korean research body SNE Research said in October that although the transition to EVs is continuing, buyers’ negativity regarding EVs cannot be lightly overlooked. EV manufacturers have issues to solve, such as ease of charging, long driving range and safety from battery fires. In particular, the issue of EV battery fires is not a simple technical issue, but rather an important issue directly related to social safety, so it has to be remedied, it said.
“The EU executive is planning to implement a new battery regulation in 2026, and the core of this is the Battery Passport. Therefore, battery manufacturers also need to strengthen battery safety and transparency to respond to international regulations,” it said.
LG Chem’s claim
It said on 1 October its R&D team developed a temperature-responsive ‘safety reinforced layer’ material designed to suppress thermal runaway. The research findings were published online in the September edition of Nature Communications scientific journal.
When the battery’s temperature rises beyond the normal range, between 90°C and 130°C, the material reacts to the heat, altering its molecular structure and effectively suppressing the flow of current, it said.
The material was analysed in collaboration with Prof. Lee Minah’s team at the Department of Battery Science at Pohang University of Science and Technology. Safety verification was conducted in partnership with LG Energy Solution.
The material is highly responsive to temperature, it claimed, with its electrical resistance increasing by 5,000 ohms for every 1°C rise in temperature. “The material’s maximum resistance is over 1,000 times higher than at normal temperatures, and it also features reversibility, meaning the resistance decreases and returns to its original state, allowing the current to flow normally again once the temperature drops,” it added.
In both battery impact and penetration tests, the batteries equipped with the thermal runaway suppression material either did not catch fire at all or extinguished the flames shortly after they appeared, preventing a full-blown thermal runaway event, according to LG Chem.