Thomas A. Faust Jr., a principal technical advisor at battery maker East Penn’s R&D Centre and Six Sigma Black Belt holder, talks about his 33 years’ experience of innovation with Frank Lev.
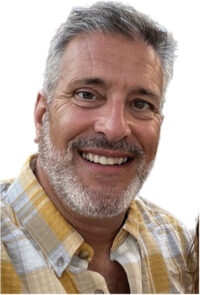
While many in the battery industry play multiple vital roles in support of manufacturing, there are those that promote a spirit of innovation and the never-ending quest to continually evolve and develop in support of their companies and industry. Thomas Faust sees his role as supporting the company’s efforts to constantly examine itself and what it does.
As the CEO of supercapacitor manufacturer Tavrima Canada, I first met Faust during a visit to East Penn in 2005 to demonstrate prototypes for a bipolar battery joint development project.
I have visited the East Penn R&D facility many times since and Faust has always provided assistance and productive collaboration in the joint development of the bipolar batteries.
The impact of innovations and improvements
Faust started his career at East Penn in 1990 as a project engineer. His first job was to find a solution to continuous pasting-paper shedding off the battery plates. Faust found the answer by mechanically treating the paper, which proved so successful that it is still used today and shared with others.
“I must say that studying the paper-making process and making paper from pulp in my college graphics class was instrumental to finding a starting point that led to a solution to the shedding problem at the time,” he said.
Faust’s Millersville University of Pennsylvania education involved many hands-on classes ranging from woodworking, offset-press photography, screen printing, welding, machining, foundry, product design, electronics, ceramics, small engines, and many others.
Creative approach to process challenges
It laid a solid foundation for his creative approach to process challenges. He also helped with the family business of making soft body armour and added automotive car detailing after work each day prior to joining East Penn. Faust said the diversity of these skills and applying solutions over these multiple disciplines has helped to make him the problem-solver he is today. Faust always looks at a problem and asks, “What other processes in any industry have a similar problem and what materials are being used?” This is the starting point for idea generation and the catalyst for creativity that leads to the solution, he said.
Faust worked 17 years at the plant manufacturing level before moving to the R&D centre. He advanced to assistant plant manager/project engineer in motive power (in the industrial battery division) during this time. In this job, he worked closely with the VP of industrial manufacturing, Andy Dietrich, on process improvement and development. Additionally, Faust interacted with leading equipment manufacturers with engineering to help solve manufacturing problems to improve quality and advance production.
This job also introduced Faust to people management and proved to be an eye-opening experience. “It is hard to imagine,” he said, “what it takes to manage hundreds of people in any one of the facilities, let alone thousands, on a site.”
Throughout this time, DeLight Breidegam, the founder of East Penn, would tour the facilities, checking on production and talking with the employees. “You never knew where or when DeLight would show up and talk to the people in the manufacturing facility one-on-one.” DeLight’s daughter and former CEO, Sally Breidegam Miksiewicz, followed in the same footsteps and was well aware of what was, and was not, working. While this kept plant management on its proverbial toes, it also served as an excellent example of the importance of staying connected with those on the production floor.
This was also a time in Faust’s career when he became involved with telecom batteries for the first time. The first was AT&T’s 2 V configurable AGM battery, followed by the large format Unigy II 2 V stationary AGM telecom product. These and similar products were in great demand due to the rapidly developing telecom market. DeLight had the foresight to build a dedicated plant for AGM and Gel.
Six years later, in 1998, Faust became the assistant plant manager of the stationary battery division as they were going through exponential growth from the telecom boom and populating the new purpose-built plant. Some of the final work he performed in the industrial battery division pertained to the stationary process development of the Unigy II 2 V. This new role involved similar process work as before but on the development side. This was Faust’s second exposure and learning experience with managing people in a much larger plant.

Asked to undergo Lean Six Sigma
In 2003, Faust was asked to undergo Lean Six Sigma training, which he accomplished and received his Six Sigma Black Belt certification. It is a process aimed at eliminating waste in work processes. According to Sigma, a certified Black Belt exhibits team leadership, understands team dynamics, and assigns their team members with roles and responsibilities. Faust’s passion for innovation led him to his current position of principal technical advisor in R&D in 2017.
People management training and vast previous experience have stood Faust in good stead in hands-on problem-solving to advance process development. He has mentored and guided people, and helped resolve conflicts.
Faust’s first R&D project as a senior development engineer was the Motive power fuel cell project in 2008, where he helped to eliminate fabrication roadblocks and resolve challenges. While the company did not fully implement the fuel cell project, Faust’s contributions benefitted subsequent projects.
Bipolar battery next up
The next project was a bipolar battery and involved several partnerships over the years as East Penn zeroed in on its own version. In the following years, there were many developments in the bipolar battery platform, and several patents were granted.
Faust put most of his time into the bipolar battery, generating many ideas and processes with the team to help develop the current East Penn platform. These earlier developments paved the way for pilot production and the path toward commercial development in areas of opportunity in applications like wheelchairs, motive power and the moderate voltage systems found in hybrid electric vehicles.
Along the way, Faust participated in many projects, contributed to creative brainstorming, and assisted in overcoming challenges outside R&D. Additional R&D projects included areas that enhanced the power capacity of lead batteries and improved their dynamic charge acceptance. Faust also helped with alternative projects, such as the detection and identification of lithium-ion batteries in the smelter, which greatly enhanced workers’ safety and helped eliminate spontaneous fires.
A string of patents
Despite having a string of patents to his name (the patents.justia.com website lists 22) Faust continues to brainstorm and problem-solve every day.
What gives him creative inspiration outside the office? He said: “I enjoy hiking frequently, backpacking, golf, kayaking, mountain biking regularly, and skiing. I can throw a frisbee exceptionally far and very accurately. I can sew (previous job), enjoy cooking, and spend time with my adult sons (both Eagle Scouts) whenever possible. All of the above despite replacing both knees 12 years ago.”
Faust has helped contribute to the evolution of lead battery process technology and development. Below are a few more highlights of his accomplishments:
(1991) Introduced pin stamp date coding to all production lines using date codes with more characters and automatic upgrade of date, shift, battery number etc. This allowed for more data and guaranteed the appropriate field changes at the correct times, which eventually became the industry standard and is still used, upgraded to a laser marking system at a significantly lower cost.
(1993) Worked directly with the equipment manufacturer and an East Penn colleague to test and provide feedback on the initial development of the Smart Dry Technology battery dry charge oven. The dry charge technology reduced the overall cycle time by 30% and consumed less power using a 10 HP motor instead of the 30 HP on standard models.
(1994) Worked with a plastic fabricator to design and manufacture reaction injection-moulded tanks with a draft angle to replace hand-made fibreglass tanks used for the battery plate formation. Unlike the fibreglass, the injection-moulded tanks required no repairs and occupied less space, allowing 5% more tanks per formation row to increase yield.
(R&D) Developed concepts for an East Penn bipole current collector design, which evolved into a preproduction bipole current collector product through the team effort.
(R&D) Developed a non-electrolytic lead addition method to increase lead thickness onto existing flat lead surfaces. The method has eliminated the time-consuming and costly plating process and improved the added surface metallurgically.
(R&D) Developed an electrically conductive cold-joining method for lead parts, which is being tested and analysed to determine where it can benefit most in the manufacturing of the bipolar and monoblock batteries.
The International Energy Agency has forecast a huge rise in global renewable power capacity requirements in the next five years. East Penn R&D Centre has always worked on improving the existing state-of-art battery technology, developing carbon-enhanced negative electrodes for the partial state of charge mild hybrid applications and other innovative designs. According to the US Department of Energy Argonne National Laboratory, there is still room for improvement in lead battery utilisation.
The market share for internal combustion engine (ICE) vehicles will still be 95% in 2030 despite the declared commitment of global automotive OEMs to discontinue their production, according to consulting and marketing analysis company Lang Marketing Resources. The existing ICE fleet will be around for many years and will need replacement lead-acid batteries, analysts say.
While East Penn will continue pursuing innovation, R&D and continuous improvement in all its processes, it will remain one of the largest lead battery manufacturers in the industry today – and developing technology – because of people like Faust and others who have infused creativity and innovative problem-solving.
East Penn routinely operates one of North America’s cleanest and most technologically advanced lead-acid battery recycling facilities. Each day, thousands of used batteries are sorted, crushed and recycled. The on-site smelter produces thousands of tons of lead alloy required to make flooded and valve-regulated lead-acid batteries (VRLA) grids and plates.
East Penn’s Lyon Station, in Pennsylvania, comprises five large automotive battery plants, an industrial battery plant, and a specialty battery plant. East Penn makes its own oxide precursor for the battery positive and negative active materials of the highest quality from the recycled lead, which, together with the high quality lead alloy grids, are the major contributing factors to the high quality of its batteries. Unlike other battery manufacturers purchasing VRLA battery valves from outside suppliers, East Penn uses its in-house-made patented valves of proven reliability.
Faust knows his work helps make a difference: “Lead battery chemistry will be here for a long time as a dependable, safe, cost-effective and established recyclable product, and it is exciting to be able to continue to play a role in unleashing so much untapped potential in such an already well-known and well-used product. I plan on continuing to develop and improve processes in the battery manufacturing arena so that this technology can serve future generations even better than it has so many in the present and past.”