
Six figure savings from PbA formation
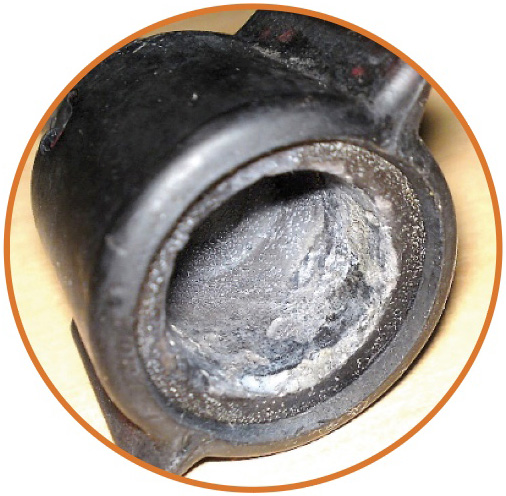
If somebody was walking out of your factory with $800,000 for every five million batteries you produced, you’d want to stop that happening.
Results from the battery formation connector testing carried out by partners UK Powertech, BESTmag and Digatron have conclusively demonstrated that lead-acid battery factories can save hundreds of thousands of US dollars per annum. The losses, identified from laboratory trials using Digatron test equipment, were predicted for a single, average-sized, lead-acid battery (LAB) factory.
The subsequent field trials in several LAB factories around the globe have provided verification of these predictions, with one company reporting savings of over $300,000 in a single plant. The company simply followed the recommended procedures that had been identified from the results of the work of the testing team.

BEST technical editor Dr Mike McDonagh has now concluded the first series of tests that relate to the battery connectors used in the formation department, which can be read in the articles linked below. It can be reported that so far, all the available results indicate the actual energy, financial and carbon savings are in line with the original predictions. Following on from this, a second series of tests are in progress and will demonstrate further savings in time and energy can be made.
As the formation process accounts for more than 50% of a LAB factory’s energy usage, manufacturers can substantially reduce energy consumption and carbon emissions, whilst adding hundreds of thousands of dollars to their bottom line.
Read the full story by clicking the links below:
1. Bad connections make your losses grow
2. Connector corrosion under the microscope
3. Peak battery performance needs the right connections
5. From theory to reality— connector-testing savings proven
6. Optimised formation saves energy
7. The importance of inter-connections in a lead-acid battery formation department